3. Способы смесеобразования. Типы камер сгорания
Распределение топлива по КС осуществляется за счет кинетических энергий топлива и движущегося воздушного заряда. Соотношение этих энергий обусловлено способом смесеобразования и формой КС. В современных автомобильных дизелях нашли применение объемное, пристеночное (пленочное), комбинированное, предкамерное и вихревое смесеобразования. КС в сочетании с топливоподающей аппаратурой определяют условия протекания процессов смесеобразования и сгорания. Камеры сгорания предназначены обеспечивать:
полное сгорание топлива при минимально возможном коэффициенте и в предельно короткий срок у ВМТ;
плавное нарастание давления при сгорании и допустимые значения максимального давления цикла рz;
минимальные потери теплоты в стенки;
приемлемые условия работы топливной аппаратуры.
Объемное смесеобразование. Если топливо распыливается в объеме однополостных (неразделенных) камер сгорания и лишь небольшая часть его попадает в пристеночный слой, то смесеобразование называют объемным. Такие КС имеют малую глубину и большой диаметр, характеризуемый безразмерной величиной – отношением диаметра КС к диаметру цилиндра: dкс/D = 0,750,85. Такая КС располагается обычно в поршне, причем оси форсунки, КС и цилиндра совпадают (рис. 6б).
Рабочий цикл дизелей с объемным смесеобразованием характеризуется следующими особенностями:
смесеобразование обеспечивается путем мелкого распыливания топлива при высоких максимальных давлениях впрыскивания (р
впрmах=50150 МПа), турбулизация в КС возникает вследствие вытеснения воздуха из зазора между буртом поршня и головкой цилиндра при подходе поршня к ВМТ;равномерное распределение топлива в воздухе обеспечивается посредством взаимного согласования формы КС с формой и расположением топливных факелов;
протекание процесса сгорания на номинальном режиме осуществляется при α = 1,50–1,6 и более, т.к. в результате неравномерного распределения топлива по объему КС при меньшем α не удается обеспечить бездымного сгорания, несмотря на согласование форм камеры и факелов, а также применения высокого давления впрыскивания;
рабочий цикл характеризуется высокими максимальными давлениями сгорания рz и большими скоростями нарастания давления Δр/Δφ;
двигатели с объемным смесеобразованием имеют высокий индикаторный к.п.д. из-за сравнительно быстрого сгорания топлива у ВМТ и меньших потерь теплоты в стенки КС, а также хорошие пусковые качества. [5, c. 345]
Важное
значение имеет поверхность топливных
струй, через которую происходит диффузия
паров топлива в окружающий воздух. Угол
рассеивания топливных струй обычно не
превышает 20°. Для обеспечения полного
охвата струями всего объема камеры
сгорания и использования воздуха число
распыливающих отверстий форсунки
теоретически должно быть i
Величина проходного сечения распыливающих отверстий fc определяется типом и размерами дизеля, условиями перед впускными органами. Она существенно влияет на продолжительность и давление впрыскивания, ограничена условиями обеспечения хорошего смесеобразования и тепловыделения. Поэтому при большом количестве распыливающих отверстий их диаметр должен быть небольшим. Чем меньше количество распыливающих отверстий, тем более интенсивно приводится во вращательное движение для полного сгорания топлива воздух, т.к. в этом случае заряд за характерный промежуток времени, принимаемый обычно равным продолжительности впрыскивания топлива, должен повернуться на больший угол. Это достигается применением винтового или тангенциального впускного каналов.
Создание
вращательного движения заряда при
впуске приводит к ухудшению наполнения
цилиндров воздухом.
Увеличение
максимального значения тангенциальной
скорости tmax вызывает уменьшение
При таком смесеобразовании КС может быть расположена соосно с цилиндром, а форсунка смещена к ее периферии. Одна или две струи топлива направляются либо под острым углом на стенку КС, имеющей сферическую форму (рис. 6г), либо вблизи и вдоль стенки КС (рис. 6д). В обоих случаях заряд приводится в достаточно интенсивное вращательное движение (тангенциальная скорость движения заряда достигает 5060 м/с), способствующее распространению топливных капель вдоль стенки камеры сгорания. Топливная пленка испаряется за счет теплоты поршня.
После начала горения процесс испарения резко возрастает под действием теплопередачи от пламени к пленке топлива. Испарившееся топливо уносится потоком воздуха и сгорает во фронте пламени, распространяющегося от очага воспламенения. При впрыскивании топлива из-за затрат теплоты на его испарение существенно снижается температура заряда (до 150200°С по осям струй). Это затрудняет воспламенение топлива вследствие уменьшения скорости химических реакций, предшествующих возникновению пламени.
Существенное
улучшение воспламеняемости низкоцетановых
топлив обесценивается при увеличении

В дизелях нашла применение КС, разработанная Центральным научно-исследовательским дизельным институтом (ЦНИДИ) (рис 6в). Топливные факелы в такой камере попадают на ее боковые стенки под входной кромкой. Отличительная особенность смесеобразования – встречное движение струй топлива и заряда, вытесняемого из надпоршневого пространства, что способствует увеличению количества топлива, взвешенного в объеме КС, и сближает этот процесс с объемным смесеобразованием. При использовании камеры ЦНИДИ применяют 35 сопловых отверстий. Параметры впрыскивания топлива близки к тем, которые имеют место в КС типа ВТЗ и ЯМЗ.
Объемно-пристеночное смесеобразование. Такое смесеобразование получается при меньших диаметрах КС, когда часть топлива достигает ее стенки и концентрируется в пристеночном слое. Часть этого топлива непосредственно соприкасается со стенкой КС. Другая часть располагается в пограничном слое заряда. Частичное попадание топлива на стенки камеры сгорания и интенсивное перемешивание воздуха и частиц топлива снижают количество паров топлива, образующихся в период задержки воспламенения. В результате снижается и скорость тепловыделения в начале сгорания. После появления пламени скорости испарения и смешивания резко возрастают. Поэтому подача части топлива в пристеночную зону не затягивает завершение сгорания, если температура стенки в местах попадания на нее струй находится в пределах 200300°С.
При dкс/D = 0,5–0,6 (рис. 6а, б, ж) в связи со значительным ускорением вращения заряда при перетекании его в КС удается использовать 35 распыливающих отверстий достаточно большого диаметра. Значение тангенциальной составляющей скорости движения заряда достигает 2530 м/с. Максимальные значения давлений впрыскивания, как правило, не превышают 5080 МПа.
В
связи с тем, что на такте расширения во
время обратного перетекания заряда из
камеры часть несгоревшего топлива
переносится в пространство над
вытеснителем, где имеется еще не
использованный для сгорания воздух. Он
не полностью участвует в процессе
окисления. Поэтому стремятся уменьшить
до минимума объем заряда, находящегося
в пространстве между поршнем (при
положении в ВМТ) и головкой цилиндра,
доводя высоту его δ
Смесеобразование в разделенных камерах сгорания. Разделенные камеры сгорания состоят из основной и вспомогательной полостей, соединенных горловиной. В настоящее время применяют в основном вихревые КС и предкамеры.
Вихревые камеры сгорания.
Как правило, в вихревых камерах сгорания используются закрытые форсунки 1 штифтового типа, обеспечивающие полый факел распыленного топлива.
При поступлении воздуха из цилиндра в вихревую камеру во время такта сжатия воздух интенсивно завихривается. Воздушный вихрь, непрерывно воздействуя на формирующийся топливный факел, способствует лучшему распыливанию топлива и смешиванию его с воздухом. В ходе начавшегося горения воздушный вихрь обеспечивает подвод к факелу свежего воздуха и отвод от него продуктов сгорания. При этом скорость вихря должна быть такой, чтобы за время впрыскивания топлива воздух мог совершить в камере сгорания не менее одного оборота.
Сгорание вначале происходит в вихревой камере. Повышающееся при этом давление вызывает перетекание продуктов сгорания и топливовоздушной смеси в цилиндр, где процесс сгорания завершается.
На рис. 9 представлены конструктивные элементы вихревых камер. Нижняя часть камеры, как правило, образуется специальной вставкой из жаропрочной стали, которая предохраняет головку от обгорания. Высокая температура вставки (800–900 К) способствует сокращению периода задержки воспламенения топлива в КС. Интенсивное вихреобразование и наличие вставки позволяют получить устойчивое протекание рабочего цикла в широком диапазоне нагрузочных и скоростных режимов.
Вихрекамерный рабочий цикл обеспечивает бездымное сгорание топлива при малых коэффициентах избытка воздуха (α = 1,2–1,3) вследствие благоприятного влияния интенсивного воздушного вихря. Сгорание значительной части топлива в дополнительной камере, расположенной вне цилиндра, обусловливает снижение максимального давления сгорания (рz=7–8 МПа) и скорости нарастания давления (0,3–0,4 МПа/°ПКВ) в надпоршневой полости цилиндра на полной нагрузке.
Рабочий цикл вихрекамерного двигателя менее чувствителен к качеству распыливания топлива, что позволяет использовать однодырчатые распылители с невысокими максимальными давлениями впрыскивания (рвпр = 20–25 МПа) и сопловым отверстием сравнительно большого диаметра – до 1,5 мм.
Основные недостатки вихрекамерного двигателя: повышенный удельный эффективный расход топлива, достигающий на режиме полной нагрузки 260270 г./(кВт·ч), а также худшие по сравнению с двигателями с неразделенными КС пусковые качества. Однако при использовании свечей накаливания в вихрекамере пусковые качества существенно улучшаются.
Более низкая экономичность вихрекамерных дизелей объясняется увеличением теплоотдачи в стенки основной и дополнительной КС вследствие более развитой их поверхности, наличия в КС интенсивного вихреобразования, больших гидравлических потерь при перетекании рабочего тела из цилиндра в вихревую камеру и обратно, а также зачастую увеличением продолжительности процесса сгорания. Ухудшение пусковых качеств двигателя обусловлено понижением температуры воздуха при перетекании в вихревую камеру и увеличением теплоотдачи в стенки вследствие развитой поверхности дополнительной КС. К числу двигателей с вихрекамерным смесеобразованием относятся тракторные дизели СМД, ЗИЛ-136, Д50, Д54 и Д75, автомобильные дизели «Перкинс», «Ровер» (Великобритания) и др. [5, c. 355–358]
Предкамерные дизели. Объем предкамеры (рис. 10) составляет 25–35% общего объема сжатия Vс. Площадь проходного сечения соединительных каналов равна 0,3–0,8% площади поршня. В КС используется однодырчатая (обычно штифтовая) форсунка 1, обеспечивающая впрыскивание топлива в направлении соединительных каналов 3.
В предкамерном дизеле воздух в процессе сжатия частично перетекает в предкамеру, где продолжает сжиматься. В нее же в конце сжатия впрыскивается топливо, которое воспламеняется и горит, вызывая быстрое повышение давления. В объеме предкамеры сгорает часть топлива, т.к. количество воздуха в ней ограничено. Несгоревшее топливо продуктами сгорания выносится в цилиндр, где дополнительно распыливается и тщательно перемешивается с воздухом за счет образующихся интенсивных газовых потоков. Сгорание переносится в надпоршневое пространство, вызывая повышение давления в цилиндре.
Таким образом, в предкамерных дизелях для смесеобразования используется энергия газа, перетекающего из предкамеры вследствие предварительного сгорания части топлива в ее объеме.
Использование для смесеобразования газового потока позволяет интенсифицировать перемешивание топлива с воздухом при сравнительно грубом распыливании топлива форсункой. Поэтому в предкамерных дизелях сравнительно низкие начальные давления впрыскивания, не превышающие 10–15 МПа, а коэффициент избытка воздуха на режиме полной нагрузки составляет 1,3–1,
Другое важное преимущество предкамерных дизелей – небольшая жесткость сгорания топлива . Давление газа в надпоршневом пространстве – не более 5,56 МПа вследствие дросселирования газа в соединительных каналах.
К преимуществам предкамерных дизелей следует отнести также меньшую чувствительность рабочего цикла к виду применяемого топлива и к изменению скоростного режима работы. Первое объясняется влиянием на условия воспламенения разогретой поверхности днища предкамеры, второе – независимостью энергии газового потока, вытекающего из предкамеры, от скорости движения поршня. Максимальная частота вращения для предкамерных дизелей малой размерности цилиндра (малого диаметра) составляет 30004000 мин-1.
Основные недостатки предкамерного дизеля: низкая топливная экономичность вследствие тепловых и гидравлических потерь, возникающих при перетекании газов, из-за растянутости процесса сгорания, а также увеличенной суммарной поверхности КС. Среднее давление механических потерь рм у предкамерных дизелей на 2535% выше, чем у двигателей с неразделенными камерами, а удельный эффективный расход топлива равен 260290 г./(кВт·ч).
Как и вихрекамерные, дизели с предкамерным смесеобразованием имеют низкие пусковые качества. Поэтому эти дизели часто отличаются повышенной (до 18–20) степенью сжатия и снабжены пусковыми свечами накаливания.
Особенности смесеобразования при наддуве. Существенно большая цикловая подача топлива должна осуществляться за время, не большее, чем топливоподача в базовом дизеле без наддува. Для увеличения цикловой подачи топлива и сохранения общей продолжительности впрыскивания дп можно увеличить до приемлемого предела эффективное проходное сечение распыливающих отверстий.
Вторая возможность – увеличение давлений впрыскивания. На практике обычно прибегают к сочетанию этих мероприятий. Увеличение давлений впрыскивания при прочих одинаковых условиях обеспечивает более мелкое и однородное распыливание топлива, что может способствовать повышению качества смесеобразования. Необходимую степень увеличения давлений впрыскивания устанавливают исходя из требуемой степени ускорения процесса смесеобразования. При впрыскивании в более плотную среду увеличивается угол рассеивания топливных струй.
Характеристика смесеобразования
Вид смесеобразования | αmin | pz, МПа | Δp/Δφ, МПа/ 0ПКВ | ре, МПа | gе, г/(кВт·ч) | |
объемное и объемно- пристеночое | 1,41,8 | 1416 | 7059 | 1,5 | 0,70,8 | 225255 |
пристеночное | 1,1 | 1416 | 6,58,0 | 1,0 | 0,70,8 | 220240 |
вихрекамерное | 1,21,3 | 1618 | 6,07,0 | 0,5 | 0,70,85 | 260290 |
предкамерное | 1,31,4 | 1720 | 5,56,0 | 0,5 | 0,650,75 | 260300 |
Отмеченная величина дп при необходимости может быть сокращена также другими, более трудоемкими способами, в частности путем увеличения диаметра плунжера топливного насоса и увеличения крутизны его кулачков. При модернизации дизелей с наддувом часто вносятся существенные изменения во все основные его системы и механизмы: снижают степень сжатия, частоту вращения n, изменяют угол опережения впрыскивания и т.д. Эти мероприятия, естественно, влияют и на смесеобразование в КС.
В
случае газотурбинного наддува плотность
заряда в цилиндре увеличивается с ростом
частоты вращения n
и нагрузки, а продолжительность периода
задержки воспламенения по времени
сокращается. Чтобы обеспечить требуемое
проникновение топливных струй в слой
воздуха за период задержки воспламенения,
топливоподающая аппаратура должна
обеспечить более резкое увеличение
значений давления впрыскивания с
увеличением частоты вращения n
и нагрузки, чем на дизеле без наддува.
При высоких степенях форсирования
наддувом применяются насосы-форсунки
и топливные системы аккумуляторного
типа. В малоразмерных вихрекамерных
дизелях легковых автомобилей =21–23.
[5, c.
363–368]
4. Типы основных камер сгорания гтд и организация процесса горения в них
Рис. 9.3. Типы основных камер сгорания
Основные камеры сгорания авиационных ГТД могут иметь разнообразные формы проточной части и различное конструктивное выполнение. Применяются практически камеры сгорания трех основных типов (рис. 9.3): а трубчатые (индивидуальные), б трубчато-кольцевые и в кольцевые.Трубчатая (вверху на рис. 9.3) камера сгорания состоит из жаровой трубы 1, внутри которой организуется процесс горения, и корпуса (кожуха) 2. На двигателях обычно устанавливалось несколько таких камер. В современных авиационных ГТД трубчатые камеры сгорания практически не используются.
В трубчато-кольцевой камере все жаровые трубы заключены в общий корпус, имеющий внутреннюю и наружную поверхности, охватывающие вал двигателя.
В кольцевой камере сгорания (внизу на рис. 9.3) жаровая труба имеет в сечении форму кольца, также охватывающего вал двигателя.
Расположение и тип форсунок, используемых для подачи топлива в камеры сгорания, также могут быть различными. Однако, несмотря на большое разнообразие схем и конструктивных форм основных камер сгорания, процесс горения в них организуется практически одинаково.
Одной из важнейших особенностей
организации процесса горения в основных
камерах сгорания ГТД является то, что
он должен протекать при
сравнительно больших коэффициентах избытка воздуха.
При реализуемых в настоящее время
температурах газа перед турбиной порядка = 1800…1600 К и ниже, как уже отмечалось,
значение коэффициента избытка воздуха
(среднее для всей камеры) должно составлять
2,0…3,0 и более. При таких значениях
однородная топливо-воздушная смесь,
как было указано выше, не воспламеняется
и не горит. При резком уменьшении
подачи топлива в двигатель, которое
может иметь место в условиях
эксплуатации, коэффициент избытка
воздуха может достигать еще существенно
больших значений (до 20…30 и более).
Вторая важная особенность этих камер состоит в том, что скорость потока воздуха или топливо-воздушной смеси в них (выбираемая с учетом требований к габаритным размерам двигателя) существенно превышает скорость распространения пламени. И, если не принять специальных мер, пламя будет унесено потоком за пределы камеры сгорания
Поэтому организация процесса
горения топлива в основных камерах
ГТД основывается на следующих двух
принципах, позволяющих обеспечить
устойчивое горение топлива при больших
значениях и высоких скоростях движения потока
в них:
1. Весь поток воздуха, поступающий в камеру сгорания, разделяешься на две части, из которых только одна часть (обычно меньшая) подается непосредственно в зону горения (где за счет этого создается необходимый для устойчивого горения состав смеси). А другая часть направляется в обход зоны горения (охлаждая снаружи жаровую трубу) в так называемую зону смешения (перед турбиной), где смешивается с продуктами сгорания, понижая в нужной мере их температуру;
2. Стабилизация пламени в зоне горения обеспечивается путем создания в ней зоны обратных токов, заполненной горячими продуктами сгорания, непрерывно поджигающими свежую горючую смесь.
Рис. 9.4. Схема основной камеры сгорания
Для примера на рис. 9.4 показана схема одного из вариантов трубчато-кольцевой камеры сгорания. Камера состоит из жаровой трубы 1 и корпуса 2. В передней части жаровой трубы, которую называют фронтовым устройством, размещаются форсунка 3 для подачи топлива и лопаточный завихритель 5. Для уменьшения скорости воздуха в камере на входе в нее (за компрессором) выполняется диффузор 4, благодаря которому скорость воздуха перед фронтовым устройством обычно не превышает 50 м/с. Воздух, поступающий в камеру
сгорания из компрессора, делится на две
части. Одна часть направляется в зону
горения, а вторая часть
в зону смешения. Часть воздуха, поступающая
в зону горения, в свою очередь делится
еще на две части. Первая часть, так
называемый первичный воздух (см. рис. 9.4), поступает непосредственно
через фронтовое устройство к месту
расположения факела распыла топливной
форсунки и используется для формирования
богатой топливной смеси такого состава,
который обеспечивал бы на всех режимах
достаточно быстрое и устойчивое
сгорание.
Вторая его часть (так
называемый вторичный воздух )
через боковые отверстия в жаровой трубе
поступает в камеру для завершения
процесса горения (первичного воздуха
для этого недостаточно). Общее количество
воздуха, поступающего в зоны горения
(т.е.
)
обеспечивает в ней коэффициент избытка
воздуха порядка
= 1,6…1,8, что соответствует устойчивому
горению, полному сгоранию и температуре
порядка 1800…1900 К.
Если допустимая температура газов перед турбиной ниже этой величины, необходимый для её уменьшения третичный (или смесительный) воздух поступает в жаровую трубу через задние ряды отверстий или щелей, быстро снижая их температуру до допустимой. При этом важно подчеркнуть, что, если какая-то часть топлива не успеет сгореть до попадания в зону смешения, то дальнейшее ее догорание практически уже не произойдет, так как коэффициент избытка воздуха возрастает до значений, превышающих предел устойчивого горения.
Число, расположение и форма отверстий для подвода третичного воздуха подбираются таким образом, чтобы обеспечить желаемое поле температур газа перед турбиной.
Подвод первичного и вторичного воздуха в жаровую трубу должен быть организован так, чтобы в зоне горения создавалась нужная структура потока. Эта структура должна обеспечить хорошее смешение топлива с воздухом и наличие мощных обратных токов, обеспечивающих надежное воспламенение свежей смеси на всех режимах работы камеры.
Рис. 9.5. Зона обратных токов
в основной камере сгорания
Структура потока в передней части жаровой трубы камеры сгорания с так называемым лопаточным завихрителем показана схематично на рис. 9.5. Воздух поступает сюда через завихритель 1, лопатки которого закручивают поток (подобно лопаткам входного направляющего аппарата компрессора). Далее воздух движется вдоль поверхности жаровой трубы в виде конической вихревой струи. Вихревое движения воздуха приводит к понижению давления в области за завихрителем, вследствие чего в эту область устремляется газ из расположенных дальше от фронтового устройства участков жаровой трубы. В результате здесь возникает зона обратных токов, граница которой показана на рисунке линией 5. Топливо-воздушная смесь, образовавшаяся за фронтовым устройством, при запуске двигателя поджигается огненной струей, создаваемой пусковым воспламенителем 6 (см. рис. 9.4). Но в последующем горячие продукты сгорания вовлекаются в зону обратных токов и обеспечивают непрерывное поджигание свежей смеси. Кроме того, горячие газы, циркулирующие в этой зоне, являются источником теплоты, необходимой для быстрого испарения топлива.Могут использоваться и другие схемы основных камер сгорания с несколькими форсунками (несколькими рядами форсунок), с другими способами создания зоны обратных токов и т.д. Но общие принципы организации рабочего процесса в них остаются такими же.
ФОРСАЖНЫЕ КАМЕРЫ СГОРАНИЯ И ОРГАНИЗАЦИЯ ПРОЦЕССА
ГОРЕНИЯ В НИХ
Рис. 9.6. Схема форсажной камеры сгорания
Состав горючей смеси в форсажной камере отличается от такового в основных камерах сгорания прежде всего тем, что на расчетном режиме их работы температура газа на выходе из неё составляет 2000…2300 К, что может быть достигнуто только при суммарном коэффициенте избытка воздуха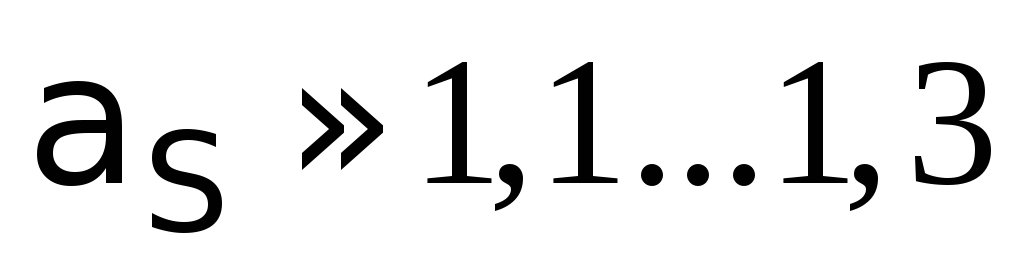
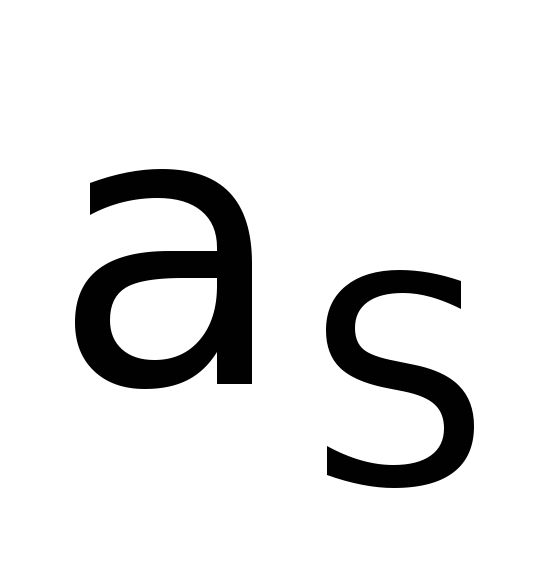
На рис. 9.6 показана типичная схема форсажной камеры сгорания, установленной за турбиной ТРД. На входе в камеру имеется небольшой диффузор 7. За ним расположено фронтовое устройство, состоящее из нескольких стабилизаторов пламени 5 (пластин или колец vобразного сечения) и большого числа (часто нескольких десятков) форсунок 1, объединенных в несколько топливных коллекторов (на рис. 9.6 их два). Большое число форсунок обеспечивает равномерность состава смеси по объему камеры, а наличие нескольких коллекторов позволяет путем их частичного отключения сохранить на пониженных режимах (т.е. при сниженном общем расходе топлива) необходимый для устойчивого горения состав смеси около тех форсунок, которые еще не отключены.
Камеры сгорания В современных бензиновых двигателях с верхним расположением клапанов преимущественно используются камеры сгорания следующих типов: полусферические, полисферические, клиновые, плоскоовальные, грушевид- ные, цилиндрические. Существуют смешанные варианты камер сгорания. Форма камеры сгорания определяется расположением клапанов, формой днища поршня, расположением свечи, а иногда и двух свечей зажигания, наличием вытеснителей. При проектировании двигателя с учетом применяемого топлива и заданной степени сжатия к камерам сгорания предъявляются следующие требования: обеспечение высоких скоростей сгорания, снижения требований к октановому числу топлива, минимальных потерь с охлаждающей жидкостью, низкой токсичности, технологичности производства. Это определяется следующими условиями: —компактностью камеры сгорания; камеры сгорания к рабочему объему цилиндров. Как уже отмечалось, одним из способов повышения эффективного КПД двигателя является увеличение степени сжатия. Основной причиной ограничения степени сжатия является опасность появления аномальных процессов сгорания (детонации, калильного зажигания, грохота и др.). У современных серийных двигателей, имеющих достаточно высокие степени сжатия, дальнейшее их увеличение даст сравнительно небольшой эффект и связано с необходимостью решения ряда проблем. Прежде всего — это возникновение детонации. Именно она определяет требования к величине степени сжатия и форме камеры сгорания. После воспламенения рабочей смеси от искры фронт пламени распространяется по камере сгорания, давление и температура в этой части заряда растут до 50…70 бар и 2000…2500 С, в наиболее удаленной от свечи части рабочей смеси происходят предпламенные химические реакции. При невысокой частоте вращения коленчатого вала, особенно в двигателях с большим диаметром цилиндров, время на эти реакции иногда оказывается достаточным, чтобы остаточная часть заряда сгорала с высокими скоростями (до 2000 м/с). Детонационное сгорание вызывает появление ударных волн, распространяющихся по камере сгорания с высокой скоростью, вызывая металлические стуки, иногда неправильно называемых стуком пальцев. Ударная волна, разрушая пристеночный слой газов с пониженной температурой, способствует повышению теплоотдачи в стенки цилиндра, камеры сгорания, тарелки клапанов, днище поршня, вызывая их перегрев и увеличивая тепловые потери в двигателе. Работа с сильной детонацией приводит к общему перегреву двигателя, ухудшению мощностных и экономических показателей. При длительной езде с интенсивной детонацией начинается эрозия стенок камеры сгорания, оплавление и задиры поршня, повышенный износ верхней части цилиндра из-за срыва масляной пленки, поломка перемычек между канавками поршневых колец и задиры зеркала цилиндра, прогар прокладки головки цилиндров. К числу факторов, влияющих на требования к октановому числу топлива, относится компактность камеры сгорания, характеризуемая степенью нарастания объема сгоревшей части смеси (в % к полному объему камеры сгорания) по мере удаления условного фронта пламени от свечи. Наиболее компактными являются полусферические, шатровые камеры сгорания, имеющие пониженные требования к октановому числу. Однако для повышения степени сжатия до 9,5… 10,5 в полусферических или полисферических камерах иногда приходится днище поршня делать выпуклым, что существенно ухудшает степень компактности и соответственно повышает требования к октановому числу, которые возрастают на 3…5 единиц. В современных двигателях с 4 клапанами в одном цилиндре свеча располагается в центре камеры сгорания. Это обеспечивает максимальную степень нарастания объема. Другим параметром, характеризующим антидетонационные качества, является степень турбулизации смеси в процессе сгорания. Интенсивность турбулизации зависит от скорости и направления потока смеси на входе в камеру сгорания. Одним из способов создания интенсивной турбулизации является увеличение площади вытеснителя (объема расположенного между днищем поршня и плоскостью головки цилиндров) с целью турбулизации заряда для увеличения скорости сгорания. Вытеснители имеют клиновые, овальные, грушевидные камеры сгорания. При замене плоскоовальной камеры сгорания на грушевидную, увеличении за счет этого площади вытеснителя при одновременном уменьшении его высоты на двигателях автомобилей УАЗ удалось без изменения требований к ОЧ топлива поднять степень сжатия на 0,5, за счет чего расход топлива уменьшился на 5…7%, а мощность увеличилась на 4… 5%. У двигателей УЗАМ 331 и у некоторых двигателей грузовых автомобилей (ЗИЛ-508.10) для создания вихревого движения заряда перед впускным клапаном канал выполнялся улиткообразным. Однако при высоких скоростях смеси это приводило к увеличению сопротивления и соответственно снижению мощностных показателей. Поэтому последние модели двигателей УЗАМ выпускаются с обычным впускным каналом. Полусферические, полисферических цилиндрические камеры сгорания практически не имеют вытеснителя, поэтому их антидетонационные качества (по индексу детонации) уступают камерам с вытеснителями. При массовом производстве двигателей за счет отклонения размеров деталей кривошипно-шатунного механизма и объема камеры сгорания фактическая степень сжатия двигателя одной модели может отличаться на значительную величину (в пределах одной единицы). Поэтому для автомобиля одной и той же модели часто требуются бензины с разным октановым числом. Фактическую степень сжатия приблизительно можно определить при помощи компрессометра. а — полусферическая; б — полусферическая с вытеснителем; в — сферическая; г — шатровая; д — плоскоовальная; е -клиновая; з — цилиндрическая камера сгорания в поршне; ж — полуклиновая с частью камеры в поршне; Общие знания о двигателях внутреннего сгорания на главную 0-100 км/ч 0-100
|
1. Общая компоновка и основные типы камер сгорания.
Камера сгорания независимо от способа выполнения состоит из двух основных частей – жаровой трубы, в которой происходит сжигание топлива, и внешнего кожуха, расположенного вокруг жаровой трубы. Топливо впрыскивается через форсунки в начальную, фронтовую часть жаровой трубы.
Воздух из компрессора поступает в пространство между кожухом и жаровой трубой, откуда проходит внутрь трубы через имеющиеся в ее стенках отверстия. Продукты сгорания топлива и избыточный воздух, т. е. газовая смесь, из жаровой трубы выходят в турбину.
По общей компоновке различают три основных типа камер сгорания: трубчатая или индивидуальная (рис. 3.2), кольцевая (рис. 3.3) и трубчато-кольцевая (рис. 3.4).
Рис. 3.2. Схема трубчатой камеры сгорания:
1 — жаровая труба; 2 — кожух; 3 — фиксатор; 4 — форсунка;
5 — соединительный патрубок
Кольцевая камера сгорания представляет собой жаровую кольцевую трубу, размещенную между наружным и внутренним цилиндрическими кожухами. В двигателе всегда используется только одна кольцевая камера, расположенная коаксиально с ротором (см. рис. 3.3).
Рис. 3.3. Схема кольцевой камеры сгорания:
1 И 5 — внешняя и внутренняя стенки жаровой трубы; 2 и 6 — наружный и внутренний кожухи; 3 — фиксатор жаровой трубы; 4 — форсунка
Трубчато-кольцевая камера имеет наружный и внутренний кожухи, между которыми размещены цилиндрические жаровые трубы, т.е. она представляет собой комбинацию двух предыдущих типов (см. рис. 3.4).
Рис. 3.4. Схема трубчато-кольцевой камеры сгорания:
1 — жаровая труба; 2 и 6 — наружный и внутренний кожухи; 3 — фиксатор;
4 — форсунка; 5 — соединительный патрубок
В рабочем состоянии температура жаровой трубы намного выше, чем кожуха. Поэтому для устранения тепловых напряжений при всех компоновочных решениях жаровая труба фиксируется в осевом направлении по отношению к кожуху только в одном месте, причем способ фиксации предусматривает возможность свободной деформации трубы в радиальном направлении.
Установка форсунки во фронтовой части трубы и способ присоединения выходной ее части допускают свободное осевое перемещение трубы, но фиксируют ее положение в радиальном направлении.
В трубчатых и трубчато-кольцевых камерах отдельные жаровые трубы связаны друг с другом соединительными патрубками. Этим повышается надежность действий камер, поскольку при срыве пламени в одной из жаровых труб горючая смесь поджигается раскаленными газами, поступающими через патрубок из соседней, работающей трубы. Кроме того, применение соединительных патрубков упрощает систему запуска, так как позволяет устанавливать пусковые устройства (пусковые воспламенители) не на всех жаровых трубах.
Трубчатая камера сгорания более проста для экспериментальной отработки, чем кольцевая; в случае каких-либо дефектов в эксплуатации ее смена не требует разборки двигателя, что невозможно при кольцевой камере. Вместе с тем комплект трубчатых камер на двигатель при одинаковой общей площади поперечного сечения, что и у кольцевой камеры, имеет существенно больший диаметральный габарит и массу. Применение трубчатых камер связано с необходимостью двукратной перестройки потока (с кольцевой формы на ряд цилиндрических струй при поступлении из компрессора в камеры и наоборот при выходе из камер в турбину), что приводит к дополнительным гидравлическим потерям и усложняет конструкцию двигателя. Кожухи кольцевой камеры в отличие от трубчатых кожухов могут использоваться в качестве силовых элементов двигателя.
Трубчато-кольцевая камера сгорания во многих отношениях позволяет объединить преимущества трубчатой и кольцевой камер. Однако в сравнении с кольцевой камерой при одинаковом поперечном габарите она имеет меньшие площади поперечного сечения газового тракта и хуже согласуется с входом в турбину.
В настоящее время применяются в основном только кольцевые и трубчато-кольцевые камеры. Трубчатые камеры используются лишь в маломощных двигателях, в которых можно ограничиться одной камерой.
Виды конструкций камер сгорания:
Существует несколько типов конструкций камер сгорания дизельных двигателей, каждая из которых призвана обеспечить наиболее эффективный вихревой поток.
Виды конструкций камер сгорания:
- Камера сгорания с прямым впрыском
- Камера сгорания с непрямым впрыском.
Камера сгорания с прямым впрыском
В камере сгорания с прямым впрыском топливо впрыскивается непосредственно у закрытого конца цилиндра. Давайте рассмотрим подробнее схему камеры сгорания открытого типа.
Камеры сгорания, как правило использовались на тяжелых автомобилях, но после модификации стали использоваться на автомобилях с 2-х литровым двигателем. Как вы видите в поршне имеется глубокая выемка в которой находится воздух, в тот момент когда поршень находится в ВМТ (верхней мертвой точке) в непосредственной близости к головке цилиндров. Поэтому, чтобы получить требуемую степень сжатия, необходимо использование верхнеклапанного механизма. Для головок цилиндров в головке поршня имеются неглубокие выемки для обеспечения необходимых зазоров. При неправильной регулировке клапанов, последние будут бить по поршню.Для подачи тонко распыленного топлива с давлением 175 бар с струю воздуха применяется форсунка, затем топливовоздушная смесь поступает в выемку поршня (камеру сгорания). Завихрение в этом случае образуется в вертикальной и горизонтальной плоскостях.
При подъеме поршня воздух заходит в выемку и перемещается примерно так, как изображено на рисунке. Когда поршень находится в ВМТ, это движение еще больше ускоряется благодаря завихрению поршня между поршнем и головкой. Горизонтальное или вращающееся завихрение может быть получено путем использования завихрителя на впускном клапане.
Комбинация двух вихревых потоков создает «круговорот» воздуха в выемке и обеспечивает необходимую подачу кислорода в область горения.
Камера сгорания с непрямым впрыском
При непрямом впрыске может впрыск более равномерный, за счет этого необходимо меньшее давление впрыска. Непрямой впрыск обеспечивает работу двигателя в большом диапазоне оборотов.
Фирма Ricardo Comet сконструировала большинство камер сгорания с непрямым впрыском. В камерах непрямого впрыска имеется вихрекамера, которая соединяется каналом с главной камерой. Благодаря этому конструкция позволяет работать с более высокими температурами.
При такте сжатия нагнетание воздуха происходит через канал вихрекамер. В быстро движимую массу воздуха происходит впрыск топлива, после чего оно распыляется на мельчайшие частички. После горения в вихревой камере уже горящее топливо с несгоревшим топливом поступает в основную камеру сгорания, которая находится в днище поршня. При увеличении времени впрыска для поддержания необходимой мощности двигателя, основная часть топлива, впрыскиваемая уже в конце периода впрыска, тщательно смешивается с воздухом в основной камере и уже потом загорается. Благодаря этому период горения может продолжаться в течении длительного времени до тех пор, пока топливу не будет хватать кислорода для горения. С этого момента начнет появляться черный смог. Он показывает максимум топлива, которое может быть впрыснуто для работы двигателя с максимальной мощностью и без потери экономичности.
7.4. Типы основных камер сгорания гтд и организация процесса горения в них
Практически применяются камеры сгорания трех основных типов (рис. 7.2): а трубчатые (индивидуальные), б трубчато-кольцевые и в кольцевые.
Трубчатая камера сгорания (рис. 7.2 а) состоит из жаровой трубы 1, внутри которой организуется процесс горения, и корпуса 2.
В трубчато-кольцевой камере (рис. 7.2 б) все жаровые трубы заключены в общий корпус, имеющий внутреннюю и наружную поверхности, охватывающие
Рис. 7.2. Типы камер сгорания
вал двигателя.В кольцевой камере сгорания (рис. 7.2 в) жаровая труба имеет в сечении форму кольца, также охватывающего вал двигателя.
Однако, несмотря на большое разнообразие схем и конструктивных форм камер сгорания, процесс горения в них организуется практически одинаково.
Одной
из важнейших особенностей организации
процесса горения в основных камерах
сгорания ГТД является то, что он должен
протекать при
сравнительно больших коэффициентах
избытка воздуха.
При реализуемых в настоящее время
температурах газа перед турбиной порядка = 1800…1600 К и ниже, как уже отмечалось,
значение коэффициента избытка воздуха
(среднее для всей камеры) должно составлять
2,0…3,0 и более. При таких значениях
однородная топливо-воздушная смесь,
как было указано выше, не воспламеняется
и не горит. При резком уменьшении подачи
топлива в двигатель, которое может иметь
место в условиях эксплуатации, коэффициент
избытка воздуха может достигать еще
существенно больших значений (до 20…30
и более).
Вторая важная особенность этих камер состоит в том, что скорость потока воздуха или топливо-воздушной смеси в них существенно превышает скорость распространения пламени. И, если не принять специальных мер, пламя будет унесено потоком за пределы камеры сгорания
Поэтому
организация процесса горения топлива
в основных камерах ГТД основывается на
следующих двух принципах, позволяющих
обеспечить устойчивое горение топлива
при больших значениях и высоких скоростях движения потока в
них:
1. Весь поток воздуха, поступающий в камеру сгорания, разделяешься на две части, из которых только одна часть (обычно меньшая) подается непосредственно в зону горения (где за счет этого создается необходимый для устойчивого горения состав смеси). А другая часть направляется в обход зоны горения (охлаждая снаружи жаровую трубу) в так называемую зону смешения (перед турбиной), где смешивается с продуктами сгорания, понижая в нужной мере их температуру;
2. Стабилизация пламени в зоне горения обеспечивается путем создания в ней зоны обратных токов, заполненной горячими продуктами сгорания, непрерывно поджигающими свежую горючую смесь.
Для примера на рис. 7.1 показана схема трубчато-кольцевой камеры сгорания. Камера состоит из жаровой трубы и корпуса. В передней части жаровой трубы, которую называют фронтовым устройством, размещаются форсунка для подачи топлива и лопаточныйзавихритель. Для уменьшения скорости воздуха в камере на входе в нее (за компрессором) выполняется диффузор, благодаря которому скорость воздуха перед фронтовым устройством обычно не превышает 50 м/с.
Воздух,
поступающий в камеру сгорания из
компрессора, делится на две частии
.
Одна часть
направляется
в зону горения, а вторая часть
в зону смешения. Первая часть, так
называемый первичный воздух
,
поступает непосредственно через
фронтовое устройство к месту расположения
факела распыла топливной форсунки и
используется для формирования богатой
топливной смеси такого состава, который
обеспечивал бы на всех режимах достаточно
быстрое и устойчивое сгорание.
Вторая
его часть (так называемый вторичный воздух )
через боковые отверстия в жаровой трубе
поступает в камеру для завершения
процесса горения (первичного воздуха
для этого недостаточно). Общее количество
воздуха, поступающего в зоны горения,
обеспечивает в ней коэффициент избытка
воздуха порядка
= 1,6…1,7, что соответствует устойчивому
горению, полному сгоранию и температуре
порядка 1800…1900 К.
Если
допустимая температура газов перед
турбиной ниже этой величины, необходимая
для её уменьшения часть воздуха поступает в жаровую трубу через задние
ряды отверстий или щелей, быстро снижая
их температуру до допустимой. При этом
важно подчеркнуть, что, если какая-то
часть топлива не успеет сгореть до
попадания в зону смешения, то дальнейшее
ее догорание практически уже не
произойдет, так как коэффициент избытка
воздуха возрастает до значений,
превышающих предел устойчивого горения.
Рис. 7.3. Зона обратных токов
в основной камере сгорания
Структура потока в передней части жаровой трубы камеры сгорания с так называемым лопаточным завихрителем показана схематично на рис. 7.3. Воздух поступает сюда через лопаточный завихритель, лопатки которого закручивают поток (подобно лопаткам входного направляющего аппарата компрессора). Далее воздух движется вдоль поверхности жаровой трубы в виде конической вихревой струи. Вихревое движения воздуха приводит к понижению давления в области за завихрителем, вследствие чего в эту область устремляется газ из расположенных дальше от фронтового устройства участков жаровой трубы. В результате здесь возникает зона обратных токов. Топливо-воздушная смесь, образовавшаяся за фронтовым устройством, при запуске двигателя поджигается огненной струей, создаваемой пусковым воспламенителем (рис. 7.1). Но в последующем горячие продукты сгорания вовлекаются в зону обратных токов и обеспечивают непрерывное поджигание свежей смеси. Кроме того, горячие газы, циркулирующие в этой зоне, являются источником теплоты, необходимой для быстрого испарения топлива.Глава 7 камеры сгорания гтд
7.1. Назначение камер сгорания и основные
Требования к ним
Камеры сгорания ГТД (рис. 7.1) предназначены для подвода теплоты к рабочему телу в двигателе за счет преобразования химической энергии топлива в тепловую при его сгорании с участием кислорода, содержащегося в воздухе.
Рис. 7.1.Схема камеры сгорания ГТД
Камера сгорания один из важнейших элементов ГТД, от совершенства которого в значительной мере зависят надежность двигателя и его экономичность. Соответственно к камерам сгорания предъявляются нижеследующие основные требования.1. Высокая полнота сгорания топлива. Потери теплоты в процессе горения связаны, в основном, с неполным сгоранием. Теплоотдача через стенки камеры сгорания во внешнюю по отношению к двигателю среду обычно пренебрежимо мала.
2. Возможно малые потери полного давления. Снижение полногодавления потока, проходящего через камеру, из-за наличия гидравлических и других потерь отрицательно сказывается как на тяге, так и на экономичности двигателя.
3. Минимально возможные габариты при данном количестве выделяемой при сгорании топлива теплоты.
4. Устойчивый процесс горения в широком диапазоне режимов работы и условий полета. Иначе возможно самовыключение двигателя из-за «срыва» пламени.
5. Обеспечение необходимого и стабильного поля температур на входе в турбину. Нестабильность и окружная неравномерность температурного поля отрицательно сказываются на тепловом режиме сопловых и рабочих лопаток турбины и, следовательно, на их надежности и ресурсе.
6. Низкий уровень выброса твердых частиц (сажи) и вредных (токсичных) веществ в продуктах сгорания. «Дымление» двигателей приводит к загрязнению атмосферы, к нарушению нормального теплового режима деталей газового тракта (при отложении сажи на их поверхности) и т. д.
7. Надежный запуск («розжиг») на земле и в воздухе. Камеры сгорания ТРД должны обеспечивать надежное воспламенение топлива в них на высотах по крайней мере до 6 …10 км.
7.2. Основные параметры камер сгорания гтд
Для оценки совершенства камер сгорания и эффективности их рабочего процесса используются следующие основные параметры камер сгорания:
1. Коэффициент
полноты сгорания. Он представляет
собой отношение количества теплоты,
реально подведенной к единице массы
воздушно-газового потока в камере
сгорания, к теоретически возможному
его значению
,
которое выделилось бы в камере при
полном сгорании топлива и при отсутствии
потерь теплоты через её стенки
.
(7.1)
Если теплотворность
топлива равна (для авиационных керосинов она составляет
42900…43100 кДж/кг), то
,
где расход воздуха через камеру сгорания,
расход топлива и
относительный расход топлива.
На расчетном режиме
обычно .
2. Коэффициент восстановления полного давления. Так называется отношение осредненного полного давления на выходе из камеры сгорания к полному давлению на входе в неё
.
(7.2)
Обычно .
3. Коэффициент
избытка воздуха ,
равный отношению действительно
поступающего в камеру сгорания в единицу
времени количества воздуха
к теоретически необходимому для полного
сгорания топлива
,
поступающего в камеру за то же время.
Количество воздуха, теоретически
необходимое для полного сгорания одного
килограмма топлива, обозначается
.
Тогда
.
(7.3)
Для авиационного
керосина .
Присмесь топлива с воздухом называетсястехиометрической. При
, т.е. когда воздуха не хватает для полного
сгорания (топливо содержится в избытке)
смесь называетсябогатой, а если
бедной.
Смесь может бытьоднородной,
если во всех микрообъемах занимаемого
ею пространства значение коэффициентаодинаково, инеоднороднойв противном случае.
Температура
продуктов сгорания однородной смеси
керосина с воздухом зависит, главным
образом, от её состава (т.е. коэффициента
избытка воздуха ).
При сгорании стехиометрической смеси
(т.е. при1)температура продуктов
сгорания достигает 2500 …
2600 К.В камерах сгорания современных
авиационных ГТД температура газа перед
турбиной (на выходе из камеры сгорания)
составляет 1500…1800 К, что соответствует
коэффициенту избытка воздуха
примерно
2…2,5.