Эволюция ГРМ: шестерни, цепь и ремень
Любите спорить на автомобильную тему и рассуждать, что лучше — ремень или цепь? Ничто так не придает спорщику значимости, как знание истории развития механизмов! Мы расскажем вам о том, как появились и ушли в небытие разные приводы ГРМ.
Два слова о ГРМ
Клапанный механизм газораспределения, сокращенно ГРМ, — это то, без чего четырехтактный двигатель существовать в принципе не может. Он открывает впускные клапана, впуская воздух или горючую смесь в цилиндры на такте впуска, открывает выпускные на такте выпуска и надежно запирает горящую в цилиндре смесь во время рабочего хода. От того, насколько хорошо он обеспечивает «дыхание» мотора — подачу воздуха и выпуск отработавших газов — зависит и мощность, и экологичность мотора.
Клапаны открывают и закрывают своими кулачками распределительные валы, а крутящий момент на них передается с коленвала, в чем, собственно, и состоит задача привода ГРМ. Сегодня для этого используют цепь или ремень. Но так было не всегда…
Старый добрый нижний распредвал
В начале ХХ века проблем с приводами распредвала не было — его раскручивали обычные шестерни, а к клапанам от него шли штанги толкателей. Клапаны располагались тогда сбоку, в «кармане» камеры сгорания, прямо над распределительным валом, и открывались-закрывались штангами. Потом клапаны стали ставить один напротив другого, чтобы уменьшить объем и площадь поверхности этого «кармана» — в результате неоптимальной формы камеры сгорания моторы имели повышенную склонность к детонации и плохой термический КПД: много тепла уходило в стенки головки блока цилиндров. И наконец, клапаны перенесли в область прямо над поршнем, и камера сгорания стала совсем небольшой и почти правильной формы.
Расположение клапанов сверху камеры сгорания и привод клапанов более длинными толкателями (так называемая схема OHV), предложенные еще в начале ХХ века Дэвидом Бьюиком, оказались самыми удобными. Такая схема вытеснила варианты моторов с боковыми клапанами в гоночных конструкциях уже к 1920 году. Например, именно она применяется в знаменитых двигателях Chrysler Hemi и моторах Corvette и в наше время. А моторы с боковыми клапанами могут помнить водители ГАЗ-52 или ГАЗ-М-20 «Победа», где данная схема применялась в двигателях.

И ведь так удобно все это было! Конструкция очень проста. Распредвал, оставаясь внизу, находится в блоке цилиндров, где прекрасно смазывается разбрызгиванием масла! Даже штанги и кулачки рокеров с регулировочными шайбами можно оставить снаружи при необходимости. Но прогресс не стоял на месте.
Почему отказались от штанг?
Проблема — в лишнем весе. В 30-е годы скорость вращения гоночных моторов на земле и авиационных моторов на самолетах достигла величин, при которых появилась необходимость облегчить механизм газораспределения. Ведь каждый грамм массы клапана вынуждает увеличивать и силу пружин, которые его закрывают, и прочность толкателей, через которые распредвал жмет на клапан, в результате потери на привод ГРМ быстро возрастают при увеличении оборотов мотора.
Выход был найден в переносе распределительного вала наверх, в головку блока цилиндров, что позволило отказаться от простой, но тяжелой системы с толкателями и значительно уменьшить инерционные потери. Поднялись рабочие обороты мотора, а значит, увеличилась и мощность. Например, Роберт Пежо создал в 1912 году гоночный двигатель с четырьмя клапанами на цилиндр и двумя верхними распредвалами. С переносом распределительных валов наверх, в головку блока, возникала и проблема их привода.
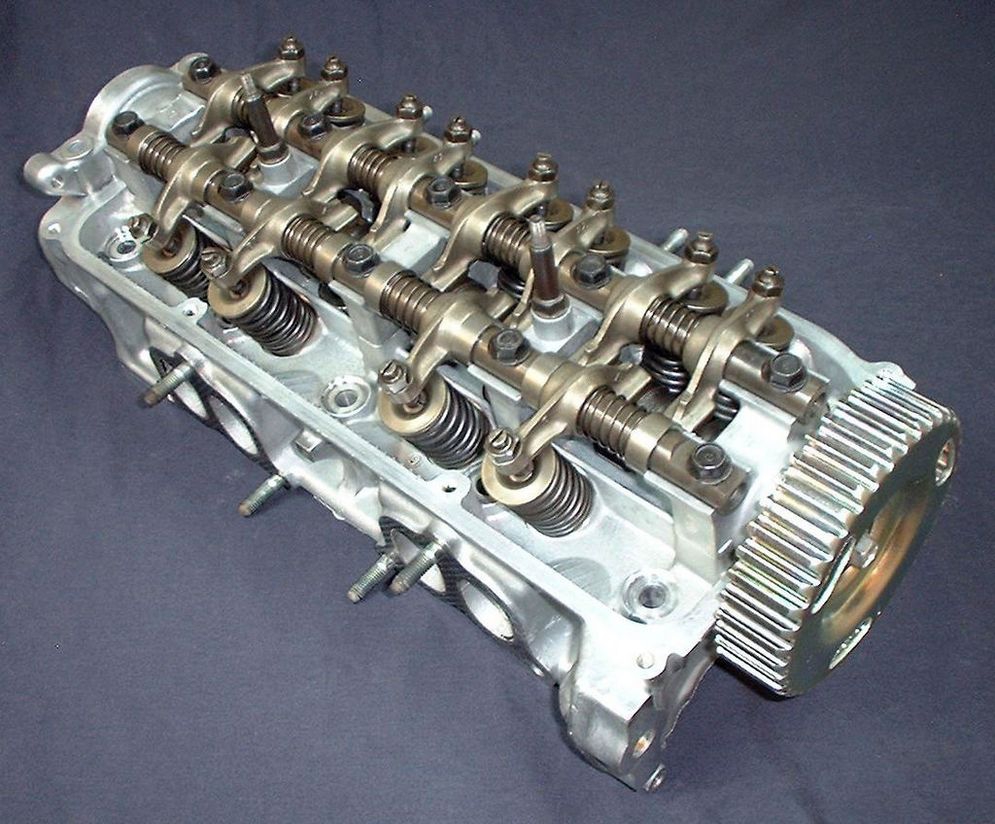
Первым решением было ввести промежуточные шестерни. Существовал, скажем, вариант с приводом дополнительным валом с коническими шестернями, как, например, на всем танкистам знакомом двигателе В2 и его производных. Такая схема применялась и на уже упомянутом моторе Peugeot, авиамоторах Curtiss К12 образца 1916 года и Hispano-Suiza 1915 года.
Еще одним вариантом стала установка нескольких цилиндрических шестерен, например в двигателях болидов Формулы-1 периода 60-х годов. Удивительно, но «многошестеренная» технология находила применение и совсем недавно. Например, на нескольких модификациях дизельных 2.5-литровых моторов Volkswagen, ставившихся на Transporter T5 и Touareg — AXD, AXE и BLJ.

Почему пришла цепь?
У шестеренчатого привода было много «врожденных» проблем, главная из которых — шумность. Помимо того, шестерни требовали точной установки валов, расчета зазоров и взаимной твердости материалов, а также — муфт гашения крутильных колебаний. В общем, конструкция при кажущейся простоте была мудреной, а шестерни — отнюдь не «вечными». Нужно было что-то другое.
Когда впервые применили цепь для привода ГРМ, точно неизвестно. Но одной из первых массовых конструкций был двигатель мотоцикла AJS 350 с цепным приводом в 1927 году. Конструкция оказалась удачной: цепь не только была тише и проще в устройстве, чем система валов, но и снижала передачу вредных крутильных колебаний за счет работы своей системы натяжения.

Как ни странно, цепь не нашла применения в авиационных моторах, и в автомобильных появилась значительно позже. Сначала она появилась в приводе нижнего распредвала вместо громоздких шестерен, но постепенно стала набирать популярность и в приводах с верхними распредвалами, однако особенно стала актуальна, когда появились моторы с двумя распредвалами. Например, цепью приводился ГРМ в двигателе Ferrari 166 1948 года и в поздних версиях мотора Ferrari 250, хотя ранние варианты его имели привод коническими шестернями.
В массовых моторах нужды в цепном приводе долго не возникало — до 80-х годов. Маломощные двигатели выпускались с нижним распредвалом, и это не только «Волги», но и Skoda Felicia, Ford Escort 1.3 и множество американских машин — на V-образных моторах штанги-толкатели стояли до последнего. А вот на высокофорсированных моторах европейских производителей цепи появились уже в 50-е годы и до конца 80-х оставались преобладающим типом привода ГРМ.
Как появился ремень?
Примерно тогда же у цепи появился опасный конкурент. Именно в 60-е развитие технологий позволило создать достаточно надежные зубчатые ремни. Хотя вообще-то ременная передача — одна из старейших, она использовалась для привода механизмов еще в античности. Развитие станочного парка с групповым приводом механизмов от паровой машины или водяного колеса обеспечило развитие технологий производства ремней. Из кожаных они стали текстильными и металлокордными, с применением нейлона и других синтетических материалов.

Первый случай использования ремня в приводе ГРМ относят к 1954 году, когда в гонках SCCA победил Devin Sports Car конструкции Билла Девина. Его мотор, согласно описанию, имел верхний распредвал и привод зубчатым ремнем. Первой же серийной машиной с ремнем в приводе ГРМ считается модель Glas 1004 1962 года небольшой немецкой компании, позднее поглощенной BMW.
В 1966 году, Opel/Vauxhall начал производство массовых моторов серии Slant Four с ремнем в приводе ГРМ. В том же году, несколько позже, появились моторы Pontiac OHC Six и Fiat Twincam, тоже с ремнем. Технология стала по-настоящему массовой.
Причем мотор от Fiat чуть было не попал на наши» Жигули»! Рассматривался вариант его установки вместо нижневального мотора Fiat-124 на будущий ВАЗ 2101. Но, как известно, старый мотор просто переделали под верхние клапаны, а в качестве привода поставили цепь.
Как видно, сначала ремень использовался исключительно на недорогих моторах. Ведь его основными преимуществами была низкая цена и малая шумность привода, что актуально для небольших машин, не обремененных шумоизоляцией. Но его нужно было регулярно менять и следить, чтобы на него не попадали агрессивные жидкости и масло, причем интервал замены уже тогда был немаленьким и составлял 50 тысяч километров.

Серьезно снижало ресурс и замасливание — тут не всегда помогал даже герметичный кожух, ведь моторы тех лет имели весьма примитивную систему вентиляции картерных газов и масло все равно попадало на ремень.
Впрочем, все нюансы применения некачественных ремней ГРМ у нас знакомы владельцам переднеприводных ВАЗ. Мотор 2108 разрабатывался как раз в 80-е, на пике увлечения ремнями. Тогда их стали ставить даже на большие моторы вроде ниссановского RB26, и надежность лучших образцов была на уровне. С тех пор споры о том, что лучше — цепь или ремень, не утихают ни на минуту. Будьте уверены, прямо сейчас, пока вы читаете эти строки, на каком-нибудь форуме или в курилке два апологета разных приводов спорят до полного изнеможения.
В следующей публикации я подробно разберу все плюсы и минусы цепных и ременных приводов. Оставайтесь на связи!
Читайте также:
Газораспределительный механизм. Назначение и устройство ГРМ :: SYL.ru
В легковом автомобиле двигатель не сможет функционировать должным образом без четкой и слаженной работы ГРМ. Он отвечает за своевременный впрыск горючего в цилиндры, а также выводит из системы отработанный газ. Еще одна важная особенность — метки ГРМ. Нужно четко соблюдать их, в противном случае впрыск и выпуск газов собьются.

Это устройство обладает сложной конструкцией. ГРМ состоит из таких деталей и механизмов: приводные элементы, распределительный вал и распределительная шестерня, элементы привода клапана, непосредственно клапан и пружины, а также направляющие втулки. Работа газораспределительного механизма синхронизируется с зажиганием и впрыском.
Распределительный вал
Работа распределительного вала заключается в том, чтобы открывать клапаны в том порядке, который необходим для правильного функционирования двигателя. Для производства этих деталей используют чугун либо же специальную сталь. Чтобы уменьшить износ детали, ее поверхности закаляются при помощи тока высокой частоты, при этом они нагреваются.
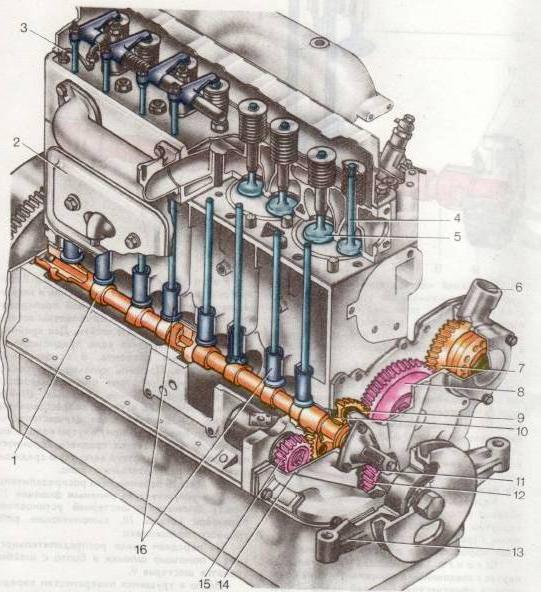
Классификация двигателей в зависимости от числа распредвалов
В зависимости от количества распредвалов двигатели подразделяют на двойные (DOHC — Double Overhead Camshaft) и одинарные (SOHC — Single Overhead Camshaft). Если рассматривать двигатель типа DOHC, то там один распредвал управляет впускными, а другой — выпускными клапанами. В SOHC эти функции выполняет один распредвал.
Привод клапанов выполняется с помощью кулачков, которые закреплены на распредвале. Их число напрямую зависит от количества клапанов. В зависимости от конструкции двигателя оно может колебаться от двух до пяти на один цилиндр. Есть различные конфигурации клапанов: два впускных и один выпускной, по два каждого типа, три впускных и два выпускных. Форма же кулачков отвечает за то, как именно будет открываться и закрываться клапан, время его открытия и высоту подъема.
Привод распредвала: общая информация
Привод распредвала от коленвала может осуществляться тремя различными способами: с помощью ремня (ременная передача), цепи (цепная передача), а если конфигурация двигателя предусматривает нижнее расположение распредвала, то с помощью зубчатых шестеренок. Самым надежным по праву считается именно цепной привод, но он отличается сложностью конструкции и высокой ценой. Ременной же привод гораздо проще, но и ресурс работы у его ремня ниже, а если тот порвется, последствия могут быть плачевными.
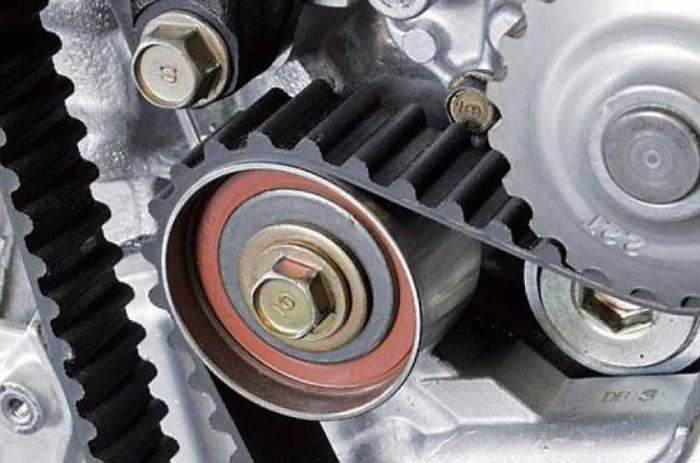
Если ремень обрывается, то работа распредвала останавливается, а коленвал продолжает работать. Чем же это грозит? Если двигатель многоклапанный, то при работе поршни будут ударяться о клапаны, которые остаются в открытом состоянии. Это может не только повредить стержни, но и направляющие втулки. Может даже разрушиться сам поршень. В простых двуклапанных двигателях такой проблемы нет, поэтому там ремонт ограничивается всего лишь заменой ремня.
Если обрывается ремень газораспределительного механизма на дизельном двигателе, то последствия будут еще тяжелее, чем на бензиновом. Поскольку камера сгорания находится в поршнях, у клапанов очень мало места. Так что если клапан зависает в открытом положении, то разрушаются на только стержни и втулки, но и распредвал, подшипники, толкатели, есть высокий шанс деформации шатунов. А если ремень обрывается на высоких оборотах, то можно даже повредить блок цилиндров.
Привод газораспределительного механизма: разновидности
В зависимости от расположения распредвала существует несколько видов привода ГРМ. Если распредвал имеет нижнее расположение, то усилие на клапаны передается с помощью толкателей, штанг и коромысел. Если же распредвал находится вверху, есть три варианта работы привода: коромыслами, толкателями и рычагами.
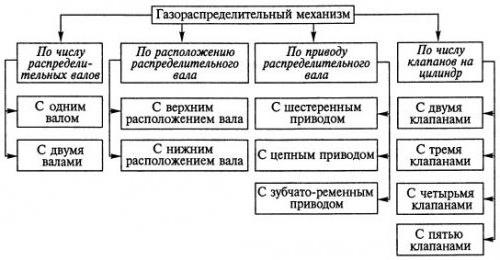
Коромысла также называют рокерами или роликовыми рычагами, они изготавливаются из стали, крепятся на ось, которая установлена в головке цилиндра на стойки. Коромысла упираются в кулачки распредвала, а также воздействуют на торец стрежня клапана. Для того чтобы уменьшить трение во время их работы, в отверстие запрессовывают специальную втулку.
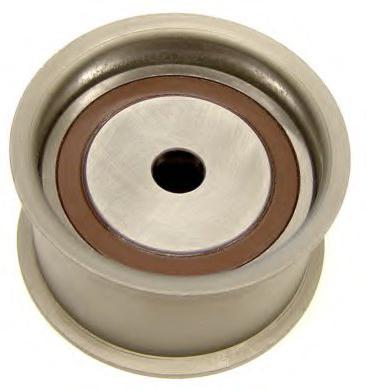
Если распредвал располагается над клапанами, то они приводятся в движение посредством рычагов. Кулачки распредвала воздействуют на стержень клапана. Есть разновидности ГРМ, в которых ставится гидрокомпенсатор между рычагом и клапаном. Такие экземпляры не требуют регулировки зазора.
В третьем варианте распредвал воздействует непосредственно на сам толкатель клапана. Толкатели бывают механическими, гидро- и роликовыми. Первые практически не используют, так как они слишком шумные, а также требуют регулировки зазора. Самым популярным является второй тип, поскольку гидротолкатели не требуют такой регулировки и работают на порядок тише. Они действуют на основе моторного масла, оно постоянно заполняет внутренние полости и таким образом смещает поршень при появлении зазора.
Часто роликовые толкатели используют в форсированных двигателях, так как они улучшают динамику за счет снижения трения. Все дело в том, что при взаимодействии кулачок катится по толкателю, а не трется, так как в том месте расположен ролик.
Клапаны
Клапанное распределение получило наибольшее распространение в силу своей простоты и высокой надежности. Оно позволяет наиболее эффективно воплощать в жизнь назначение газораспределительного механизма.
Задача клапанов — это открытие впускных и выпускных каналов в определенное время. Сам клапан имеет довольно простое строение — головка и стержень. Для впускных и выпускных клапанов головки имеют разные диаметры. Поскольку выпускные при работе нагреваются гораздо больше (так как они контактируют с отработанными нагретыми газами), их делают из теплоустойчивой стали.
На стержнях в верхней части есть выточка для крепления деталей клапанной пружины. Сами они изготовлены полыми, с наполнением из натрия (обеспечивается лучшее охлаждение). Стержни закреплены во втулках, которые делаются из металлокерамики или чугуна. Втулки, в свою очередь, запрессовываются в головки цилиндра.
Возможные неисправности в ГРМ
Так как газораспределительный механизм состоит из большого количества деталей, логично будет предположить, что существует большой риск его поломки. Среди самых распространенных причин можно выделить следующие:
— износ подшипников или толкателей клапана — можно определить по повышенному шуму мотора;
— неполадки с гидрокомпенсаторами — проявляются в виде стука при работе двигателя;
— прогорание клапанов или образование нагара в системе;
— износ сальников клапана — масло попадает в систему и начинает сгорать в цилиндрах;
— износ ремня или цепи ГРМ — падает мощность двигателя, он шумит, происходят сбои в фазах работы.
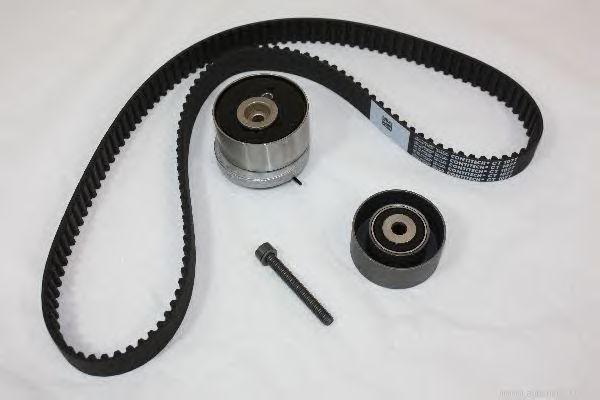
Стоит сказать, что на современных авто ГРМ выполнен достаточно качественно, это значительно повышает его эксплуатационный срок. Ведь если, например, взять газораспределительный механизм ВАЗ 2106, то можно увидеть, что он нуждался в постоянном уходе, регулировке клапанов и замене тех или иных деталей.
Признаки, по которым можно определить, что газораспределительный механизм неисправен, — это посторонние звуки в выпускном и впускном трубопроводах (хлопки или шум), уменьшение компрессии, металлический стук или падение мощности двигателя. Появление этих признаков сигнализирует о том, что ГРМ неисправен и необходим его ремонт.
Рабочий цикл двигателя и ГРМ
По стандарту рабочий цикл ДВС осуществляется за 2 поворота коленвала. В этот промежуток времени должны открыться и закрыться в определенной последовательности клапаны каждого цилиндра. Поэтому распредвал всегда вращается медленнее, чем коленвал. Соответственно, размеры шестерен у этих валов разные (у распредвала больше). Клапаны же открываются в зависимости от направления и движения цилиндров в двигателе. То есть во время такта впуска впускные клапаны открыты, и наоборот — при выпуске они закрыты. Именно с этой целью на шестерни наносятся метки ГРМ.
Газораспределительные фазы
Теория говорит, что клапаны должны открываться в моменты прохождения цилиндров через мертвые точки. Но поскольку процесс инерционен, а также при учете повышенных оборотов коленвала, этого времени явно недостаточно для впрыска смеси и выпуска отработанных газов. Поэтому впускной клапан открывается еще до того как цилиндр займет положение в верхней мертвой точке (с упреждением примерно 9-24 градуса поворота коленвала), а закрытие происходит во время прохождения цилиндром нижней мертвой точки (упреждение 51-64 градуса).
Выпускной клапан открывается примерно за 44-57 градусов до того как цилиндр займет положение в нижней мертвой точке. Закрывается он примерно на 13-27 градусах прохождения ее цилиндром.
В процессе работы двигателя бывают моменты, когда открыты оба клапана. Это положение предназначено для продувки цилиндров свежей горючей смесью с целью их очистки от излишних продуктов сгорания. Оно называется перекрытием клапанов.
Моменты, когда происходит открытие или закрытие клапана относительно мертвых точек, называются фазами газораспределения, они рассчитываются в градусах поворота коленвала.
Ремонт газораспределительного механизма
Естественно, что такая важная часть автомобиля, как ГРМ, просто не потерпит небрежного обращения. Конечно, газораспределительный механизм двигателя — достаточно надежный узел, но даже его можно сломать полностью. Одной из причин поломок может стать некачественный ремонт. Поэтому стоит внимательно относиться к этому.
Что нужно знать?
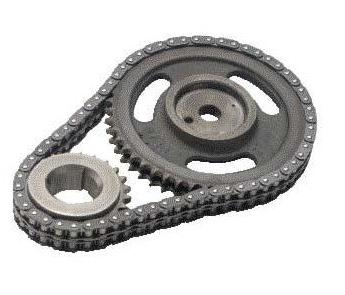
Первое, что нужно знать, перед тем как проводить ремонт газораспределительного механизма своими руками, — то, что его выполнить очень трудно. Для этого нужны технические навыки, которые вряд ли есть у обычного автомобилиста. Также будут необходимы определенные инструменты, которые можно найти далеко не в каждом гараже. Да и любое неосторожное движение может вызвать последствия, которые окажутся гораздо хуже, чем первоначальная поломка. Поэтому всегда стоит доверять ремонт ГРМ своего автомобиля только проверенным специалистам.
Устройство газораспределительного механизма таково, что чаще всего в процессе его эксплуатации выходят из строя движущиеся части: клапаны, кулачки, распредвал. Ели повреждения или неисправности не критические, вполне можно обойтись и без замены каких-либо деталей. Но если они будут серьезными, нужно быть готовым тратить деньги на покупку и установку новых запчастей. Определенную сумму придется также выложить и за саму процедуру ремонта.
Полезные советы
Как и любая другая техника, автомобиль может работать долго и безотказно, если его правильно эксплуатировать. И наоборот, небрежное обращение с ним только увеличит шанс поломок.
Газораспределительный механизм — это одна из важнейших частей, без которых двигатель не сможет функционировать. Поэтому забота о нем — фактор, который не стоит упускать из виду.
Как же уберечь ГРМ от поломок?
Во-первых, всегда нужно использовать только качественное топливо. Если оно будет с посторонними примесями, могут засориться выходы клапанов, будет давать перебои двигатель. То же самое касается и комплектующих — бракованные запчасти долго не проработают и нанесут только вред. Так что всегда стоит выбирать для своего авто только лучшие детали и расходные материалы.
Не менее важный фактор — правильная эксплуатация. Не стоит подвергать автомобиль перегрузкам, которые будут вредными для него. Перегрев двигателя, работа с неисправными узлами, длительная эксплуатация без техобслуживания снижают срок работы машины и разрушают ее узлы и детали. Поэтому правилами эксплуатации авто также не стоит пренебрегать.
устройство, принцип работы, назначение, техническое обслуживание и ремонт
ГРМ — это один из наиболее ответственных и сложных узлов в автомобиле. Газораспределительный механизм управляет впускными и выпускными клапанами двигателя внутреннего сгорания. На такте впуска ГРМ выполняет открытие впускного клапана, благодаря чему воздух и бензин попадают в камеру сгорания. На такте выпуска открывается выпускной клапан и удаляются отработанные газы. Давайте подробно рассмотрим устройство, принцип действия, типичные поломки и многое другое.
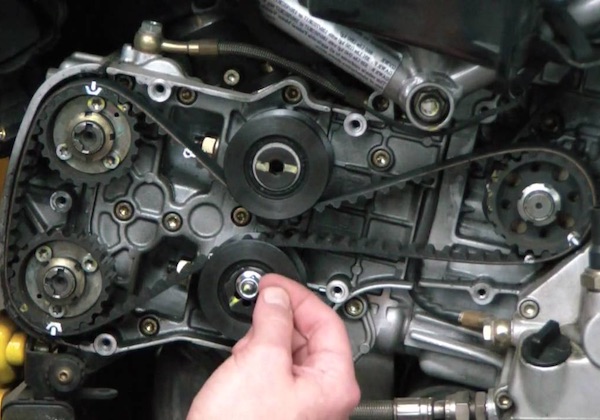
Основные узлы ГРМ
Основным элементом газораспределительного механизма является распредвал. Их может быть несколько или же один в зависимости от конструктивных особенностей ДВС. Распределительный вал выполняет своевременное открытие и закрытие клапанов. Изготавливается из стали или чугуна, а устанавливается в блоке цилиндров или картере. Отсюда можно сделать вывод, что есть несколько конструкций двигателей — с верхним и нижним расположением распределительного вала. На валу имеются кулачки, которые при вращении распредвала оказывают действие через толкатели на клапан. Для каждого клапана предусмотрен свой толкатель и кулачок.
Впускные и выпускные клапаны необходимы для подачи топливно-воздушной смеси в камеру сгорания и удаления отработанных газов. Впускные клапаны выполняют из стали с хромированным покрытием, а выпускные — из жаропрочной стали. Клапан имеет стержень, на котором крепится тарелка. Обычно впускные и выпускные клапаны отличаются между собой диаметром тарелки. Также к ГРМ стоит отнести штанги и привод.
Устройство газораспределительного механизма
Стоит еще несколько слов сказать об устройстве впускных и выпускных клапанов. Стержень клапана имеет цилиндрическую форму и канавку для установки пружины. Движение клапанов возможно только в одном направлении — к втулкам. Для того чтобы моторное масло не попадало в камеру сгорания, ставят уплотнительные колпачки из маслостойкой резины.
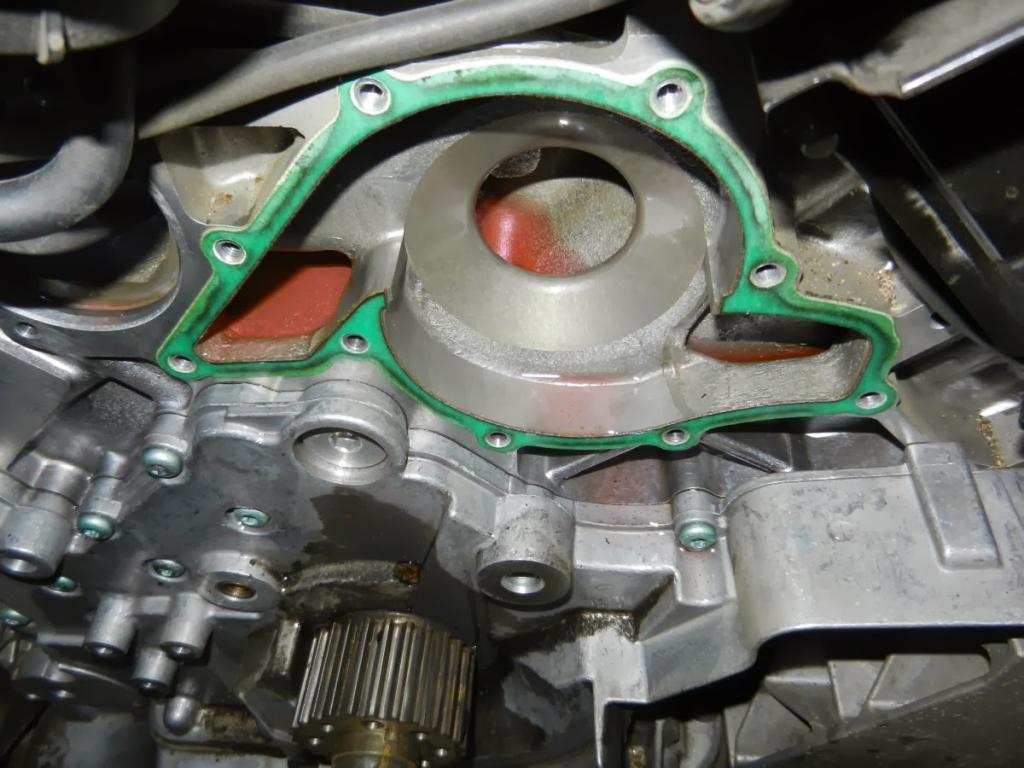
Есть еще такой узел, как привод ГРМ. Это передача вращения с коленчатого на распределительный вал. Примечательно то, что на два оборота коленвала приходится один распределительного. Собственно, это является рабочим циклом, при котором происходит открытие клапанов. Стоит заметить, что мотор с двумя распределительными валами более мощный и имеет выше КПД. Особенно это заметно на высоких оборотах. К примеру, когда ДВС оснащается одним распредвалом, то маркировка выглядит так: 1,6 литра и 8 клапанов. А вот два вала — это уже всегда в два раза большее количество клапанов, то есть 16. Ну а сейчас пойдем дальше.
Работа газораспределительного механизма
Принцип действия на всех моторах, если речь идет о таких типах, как ДВС, практически одинаков. Всю работу можно условно разделить на 4 этапа:
- впрыск топлива;
- сжатие;
- рабочий цикл;
- удаление отработанных газов.
Подача горючего в камеру сгорания осуществляется за счет движения коленчатого вала из верхней мертвой точки (ВМТ) в нижнюю мертвую точку (НМТ). При начале движения поршня открываются впускные клапаны, и топливно-воздушная смесь подается в камеру сгорания. После этого клапан закрывается, коленвал за это время проворачивается на 180 градусов от исходного положения.
После того как поршень доходит до НМТ, он поднимается вверх. Следовательно, начинается фаза сжатия. Когда достигается ВМТ, фаза считается законченной. Коленвал в это время проворачивается на 360 градусов от своего начального положения.
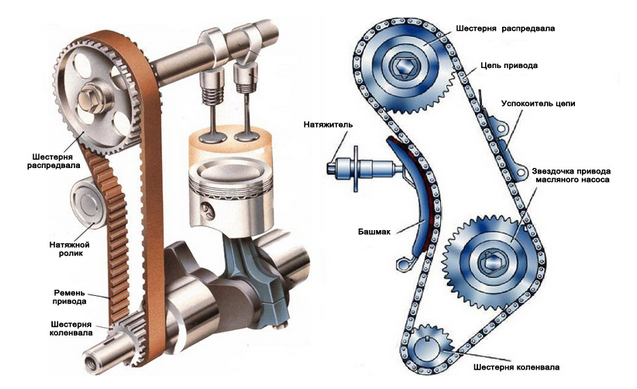
Рабочий ход и удаление газов
Когда поршень достигает ВМТ, происходит воспламенение рабочей смеси от свечей зажигания. В это время достигается максимальный момент сжатия и оказывается высокое давление на поршень, который начинает движение к нижней мертвой точке. Когда поршень опустится, то рабочий ход можно считать законченным.
Заключительная фаза — удаление отработанных газов из камеры сгорания. Когда поршень достиг НМТ и начинает свое движение к ВМТ, происходит открытие выпускного клапана и избавление камеры сгорания от газов, которые образовались в результате горения топливно-воздушной смеси. При достижении поршня НМТ фазу удаления газов принято считать законченной. При этом коленчатый вал от своего начального положения проворачивается на 720 градусов. Для достижения максимальной точности необходима синхронизация газораспределительного механизма двигателя с коленчатым валом.
Основные неисправности ГРМ
От того, насколько своевременно и качественно будет проводиться техническое обслуживание мотора, зависит его техническое состояние. В процессе эксплуатации все элементы подвергаются износу. Это касается и ГРМ. Основные неисправности механизма выглядят следующим образом:
- Низкая компрессия и хлопки в выпускной системе. В процессе эксплуатации двигателя внутреннего сгорания образуется нагар, который становится причиной неплотного прилегания клапана к седлу. На клапанах появляются раковины, а иногда и сквозные отверстия (прогар). Также компрессия падает из-за деформации головки блока цилиндров и прохудившейся прокладки.
- Заметное падение мощности и тяги, посторонние металлические стуки и троение. Основная причина — неполное открытие впускных клапанов в результате большого теплового зазора. Часть воздушно-топливной смеси не попадает в камеру сгорания. Это происходит из-за выхода из строя гидрокомпенсаторов.
- Механический износ деталей. Происходит в процессе эксплуатации двигателя и считается нормальным явлением. В зависимости от периодичности и качества обслуживания ДВС признаки критического износа на одном типе силового агрегата могут проявляться при различном пробеге.
- Износ цепи или ремня ГРМ. Цепь растягивается и может перескочить или вовсе порваться. Это касается и ремня, срок службы которого ограничен не только пробегом, но и временем.
Как выполняется диагностика ГРМ?
Газораспределительный механизм ВАЗ или любой другой машины работает по одному принципу. Следовательно, способы диагностики и основные неисправности, как правило, одни и те же. Основные поломки — неполное открытие клапанов и неплотное прилегание к гнездам.
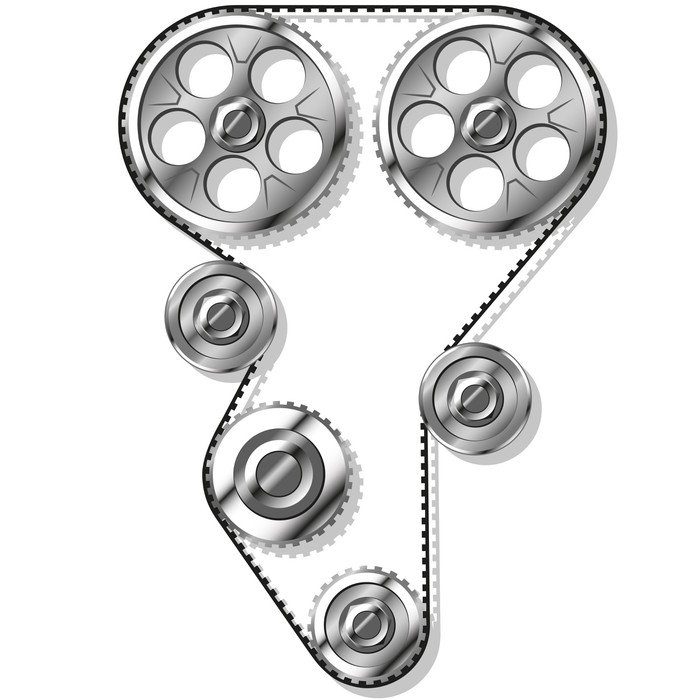
Если клапан не закрывается, то появляются хлопки во впускном и выпускном коллекторах, а также снижается тяга и мощность мотора. Происходит это из-за нагара на гнездах и клапанах, а также по причине потери упругости пружин.
Диагностика проводится довольно просто. Первым делом проверяют фазы газораспределения. Дальше замеряют тепловые зазоры между коромыслом и клапаном. Помимо этого проверяется зазор между седлом и клапаном. Если говорить о механическом износе деталей, то больше всего поломок связано с критическим износом шестеренок, в результате чего ремень или цепь неплотно прилегают к зубу и возможно проскальзывание.
Фазы ГРМ и тепловой зазор
Самостоятельно продиагностировать состояние фаз газораспределительного механизма довольно сложно. Для этого необходим набор таких инструментов, как малка-угломер, моментоскоп, указатель и др. Процедура выполняется на заглушенном двигателе. Малка-угломер устанавливается на шкив коленчатого вала. Проверяется период открытия клапана всегда в 1-м цилиндре. Для этого вручную проворачивают коленчатый вал до появления зазора между клапаном и коромыслом. С помощью малки-угломера на шкиве определяют зазор и делают выводы.
Самый простой, но наименее точный метод замера теплового зазора выполняется с помощью набора пластин длиной 100 мм и максимальной толщиной 0,5 мм. Выбирается один из цилиндров, на котором будут проводиться замеры. Его необходимо довести до ВМТ с помощью ручного поворота коленчатого вала. В сформировавшийся зазор вставляются пластины. Метод не дает 100%-й точности и результата. Ведь допустимая погрешность зачастую слишком велика. Кроме того, если имеется неравномерный износ бойка коромысла и штока, то полученные данные вообще можно во внимание не брать.
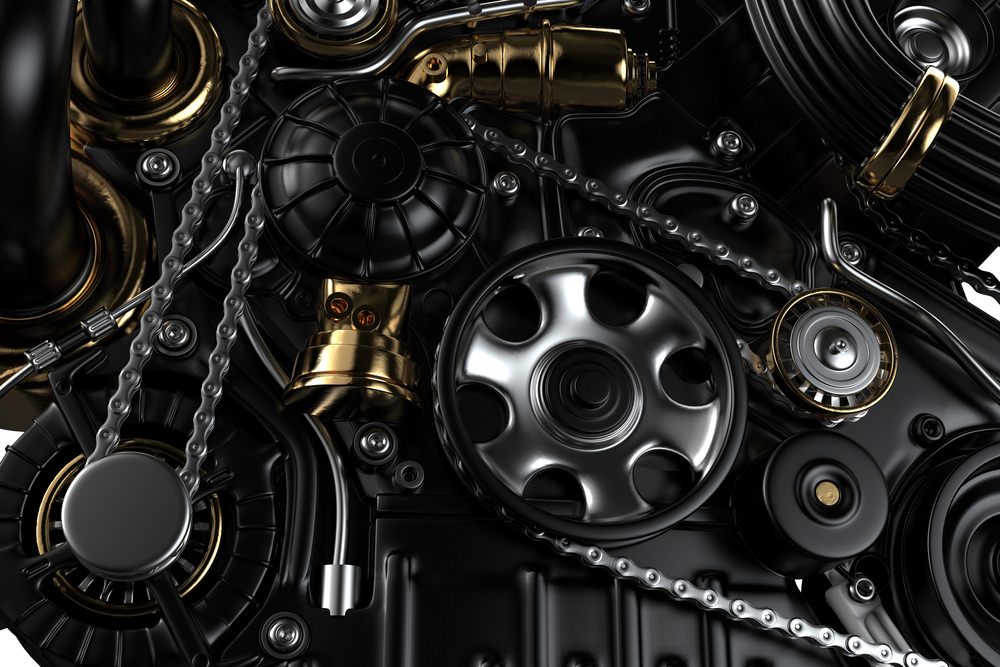
Обслуживание ГРМ
Как показывает практика, большая часть поломок газораспределительного механизма связана с несвоевременным ТО. К примеру, производитель рекомендует менять ремень каждые 120 тысяч километров. Владелец же не берет во внимание эти данные и использует ремень по 200 тысяч. В результате последний рвется, сбиваются метки ГРМ, клапаны сталкиваются с поршнями и требуется капитальный ремонт. Это же касается и такого элемента механизма, как водяной насос. Он создает необходимое давление охлаждающей жидкости для ее циркуляции по системе. Разрушение крыльчатки или выход из строя уплотнительной прокладки приводят к серьезным проблемам с двигателем. Ролики и натяжитель тоже подлежат замене. Любой подшипник рано или поздно выходит из строя. Если своевременно менять ролики и сам натяжитель, то шанс столкнуться с такой проблемой минимален. Заклинивание ролика очень часто приводит к обрыву ремня. Именно поэтому необходимо выполнять своевременное техническое обслуживание газораспределительного механизма.
О ремонте ГРМ
В большинстве случаев при обрыве ГРМ на средних и высоких оборотах требуется капитальный ремонт двигателя. Практически всегда замене подлежит цилиндро-поршневая группа. Но даже при нормальной эксплуатации детали подвергаются износу. Первым делом страдают шейки, кулачки, а также существенно увеличиваются зазоры в подшипниках коленвала. Выполняются все работы только специалистами при помощи высокоточного оборудования. Все проточки делаются под ремонтные размеры, которые закладываются заводом-изготовителем. Обычно предусмотрено 2 капитальных ремонта, после чего двигатель необходимо менять на аналогичный.
Немного информации о метках
Как уже было отмечено выше, ГРМ — узел сложный и крайне ответственный. Если привод газораспределительного механизма не синхронизирован, то завести автомобиль не выйдет. Основная причина рассинхронизации — сбитые метки. Ремень или цепь могут ослабиться из-за выхода из строя натяжителя или естественного износа. Метки выставляются относительно коленчатого вала. Для этого снимается шкив, что позволит нам увидеть шестеренку, на ней есть метка, которая должна совпадать с отметкой на масляном насосе или блоке. Соответствующие метки имеются и на распределительных валах. Используя инструкцию по эксплуатации, выставляют метки ГРМ. Очень важно понимать, что от правильности выполнения работ зависит результат. Перепрыгнувший на один зуб ремень — это не страшно, мотор будет работать, но с отклонениями. Если же метка уйдет на несколько делений, то завести авто будет невозможно.
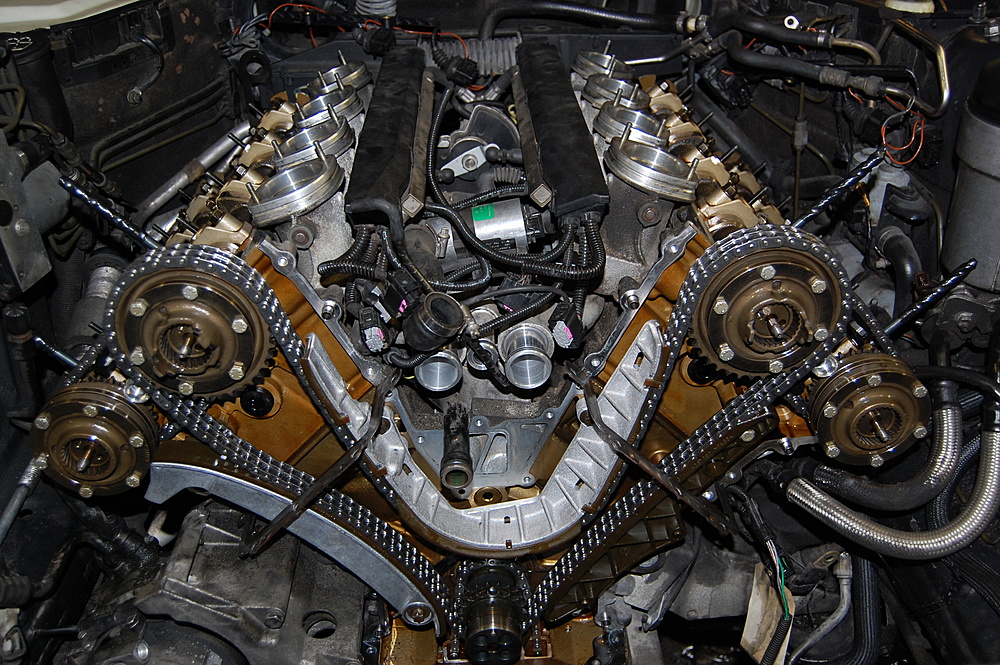
Качественные запасные части
Мы разобрались с тем, каково назначение газораспределительного механизма. Вы уже знаете, что это очень ответственный узел, который должен регулярно обслуживаться. Но важно учитывать еще и качество запасных частей. Ведь именно от них зачастую зависит срок службы ГРМ. Квалифицированная установка оригинальных комплектующих системы газораспределительного механизма практически полностью гарантирует бесперебойную работу узла в течение срока до планового обслуживания. Что касается сторонних производителей, то тут нет никаких гарантий, особенно если речь идет о комплектующих из Китая посредственного качества.
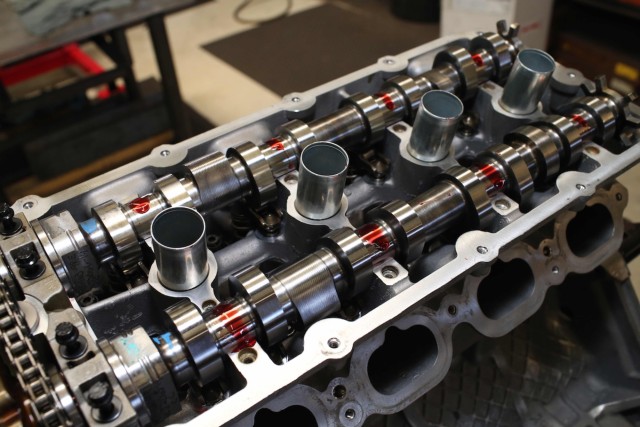
Подведем итоги
Чтобы узел работал исправно, его необходимо вовремя обслуживать. Стоит понимать, что чем сложнее мотор, тем дороже обойдется комплект ГРМ. Но экономить однозначно не стоит. Ведь скупой платит дважды. Поэтому лучше один раз купить дорогие запасные части и спать спокойно. Замену водяной помпы при ее неисправности можно приравнять к полной замене механизма. Далеко не любая конструкция двигателя позволяет допускать такие ошибки, ведь это будет стоить приличных денег. На некоторых силовых агрегатах обрыв ремня не приводит к капиталке, но на это рассчитывать не стоит.
Система изменения фаз газораспределения — Википедия
Система изменения фаз газораспределения (англ. variable valve timing, VVT) в двигателях внутреннего сгорания предназначена для изменения времени открытия клапанов и часто применяется для улучшения показателей эффективности, экономичности и токсичности. Система все более часто используется совместно с системой изменения высоты подъёма клапанов. Изменение фаз газораспределения может достигаться разными способами: полностью механическим, электро-гидравлическим и при конструкции двигателей без использования кулачков. Одной из причин внедрения автопроизводителями систем изменения фаз газораспределения является законодательное ужесточение норм токсичности.
Клапаны в двигателях внутреннего сгорания используются для управления потоками газов, втекающих и истекающих из камеры сгорания. Момент смены состояния клапана (открытие или закрытие), продолжительность нахождения в одном состоянии и высота подъёма этих клапанов в высокой степени оказывают влияние на эффективность двигателя. Без установки системы изменения фаз газораспределения или системы изменения высоты подъёма клапанов момент смены состояния этих клапанов будет независим от скорости и условий работы двигателя, что предполагает усреднённую настройку таких параметров[1]. Система изменения фаз газораспределения позволяет избавиться от этого ограничения, позволяя улучшить эффективность во всем рабочем диапазоне двигателя.
В поршневых двигателях обычно клапаны приводятся в действие посредством распределительного вала. Кулачки открывают (поднимают) клапана на определённый промежуток времени (длительность) во время каждого цикла впуска и выпуска. Момент открытия и закрытия клапанов важен и зависит от положения коленчатого вала. Распределительный вал приводится в движение от коленчатого вала посредством приводного ремня, цепи или зубчатой передачи.
Для работы на высоких скоростях двигателю требуется большой объём воздуха. Однако в таком случае впускные клапана могут закрыться раньше, прежде чем в камеру сгорания поступит необходимое количество воздуха, что снижает эффективность. С другой стороны, при оборудовании двигателя распределительным валом, позволяющим клапанам дольше оставаться открытыми, например, при установке спортивных модификаций кулачков, двигатель будет испытывать проблемы при работе на низких скоростях. Открытие впускных клапанов до закрытия выпускных может приводить к выбросу не сгоревшего топлива из двигателя, что снижает эффективность двигателя и увеличивает токсичность.
Ранние системы изменения фаз газораспределения имели дискретный (ступенчатый) принцип действия. Например, одна настройка момента открытия и закрытия клапанов при работе двигателя на скорости ниже 3500 мин−1, вторая настройка — при работе двигателя на скорости выше 3500 мин−1. Более современные системы производят плавную (бесступенчатую) регулировку момента открытия и закрытия клапанов. Такие системы позволяют производить оптимальную настройку механизма газораспределения для любых скоростей и условий работы двигателя[1][2].
Одной из простейших реализаций системы изменения фаз газораспределения является система сдвига фаз, при которой распределительный вал может быть повёрнут на некоторый угол вперёд или назад относительно положения коленчатого вала. При этом клапана закрываются и открываются раньше или позже, однако высота подъёма клапанов и длительность открытия и закрытия остаются неизменны. Для возможности регулировки длительности в системе изменения фаз газораспределения требуется внедрение более сложных механизмов, включающих, например, несколько кулачковых профилей или колеблющиеся кулачки.
Позднее закрытие впускных клапанов (англ. late intake valve closing, LIVC). Первыми реализациями изменения момента закрытия клапанов были системы, позволяющие оставлять клапан открытым дольше, чем в двигателе, не оборудованном такой системой. В результате был достигнут эффект выталкивания воздуха из цилиндра во впускной коллектор во время цикла сжатия. Вытесненный из цилиндра воздух повышает давление во впускном коллекторе, вследствие чего при следующем открытии впускного клапана воздух в цилиндр будет подаваться по б́ольшим давлением. В результате внедрения позднего закрытия выпускных клапанов достигается снижение потерь до 40 % во впускном тракте, а также снижение выбросов оксидов азота (NOx) до 24 %. Максимальный крутящий момент двигателя при этом снижается приблизительно на 1 %, а выбросы углеводородов не изменяются[2].
Раннее закрытие впускных клапанов (англ. early intake valve closing, EIVC). Другим способом снижения потерь во впускном тракте, применимым на малых скоростях работы двигателя, является создание высокого разрежения во впускном коллекторе, используя раннее закрытие впускных клапанов. Для достижения этого впускные клапаны должны закрываться в ходе цикла впуска. При малой загрузке потребности двигателя в топливо-воздушной смеси небольшие, однако достаточно высоки требования к наполнению ей цилиндров, что возможно достигнуть внедрением раннего закрытия впускных клапанов[2]. Исследования показали, что на двигателях с ранним закрытием впускных клапанов наблюдается снижение потерь во впускном тракте до 40 %, а также увеличение экономичности до 7 %. Также наблюдается снижение выбросов оксидов азота до 24 % в режимах с частичной нагрузкой. Возможной негативной стороной внедрения раннего закрытия впускных клапанов является существенное снижение температуры в камере сгорания, что может вызвать увеличение выбросов углеводородов[2].
Раннее открытие впускных клапанов (англ. early intake valve opening). Ранее открытие впускных клапанов является способом существенного уменьшения токсичности. В традиционном двигателе для управления температурой в цилиндрах используется процесс, известный как перекрытие клапанов. При раннем открытии впускных клапанов часть выхлопных газов, перетекая через впускной клапан, попадает во впускной коллектор, где быстро охлаждается. При впуске инертные отработанные газы в значительной степени заполнят цилиндр, благодаря чему достигается снижение температуры в цилиндре и уменьшение выбросов оксидов азота. Также раннее открытие впускных клапанов улучшает объёмную эффективность, поскольку объём выброса отработанных газов уменьшается в ходе цикла выпуска[2].
Раннее и позднее закрытие выпускных клапанов (англ. early/late exhaust valve closing). Внедрение этих систем позволяет достигать уменьшения токсичности. В традиционном двигателе на цикле выпуска движением поршня отработанные газы выталкиваются в выпускной коллектор и далее в выхлопную систему. Посредством раннего и позднего закрытия выпускных клапанов возможно управлять объёмом отработанных газов, остающихся в цилиндре. Оставляя клапан открытым дольше обычного, достигается более полное его очищение от отработанных газов и заполнение цилиндра б́ольшим объёмом свежей топливо-воздушной смеси. При раннем закрытии выпускных клапанов в цилиндре остаётся больше отработанных газов, благодаря чему увеличивается экономичность. Система позволяет двигателю сохранять эффективность во всех режимах работы.
Основным фактором, препятствующем повсеместному широкому внедрению системы в автомобильной промышленности, является создание экономически эффективных решений по управлению фазами газораспределения в зависимости от условий, имеющихся в двигателе.[источник не указан 354 дня] В двигателе, работающем при 3000 мин−1, распределительный вал должен вращаться со скоростью 25 мин−1, таким образом для получения преимуществ моменты открытия и закрытия клапанов должны выбираться очень точно. Электромагнитные и пневматические системы, не использующие кулачки для привода клапанов, позволяют достичь максимальной точности в управлении моментом открытия и закрытия клапанов, однако, по состоянию на 2016 год не существует экономически эффективных реализаций для производителей массовых транспортных средств.[источник не указан 354 дня]
Паровые двигатели[править | править код]
История поиска методов изменения длительности открытия клапанов начитается во времена паровых двигателей, где изменение длительности открытия клапанов известно как «отсечение пара». В ранних паровозах использовался так называемый редуктор Стивенсона, который и осуществлял изменение «отсечения», то есть изменение времени, после которого поступление пара в рабочий цилиндр прекращалось.
Ранние системы изменения «отсечения» соединяли в себе «отсечение» поступающего пара с разными реализациями отсечения отработанного пара. Разъединение этих систем было произведено с разработкой парового двигателя Корлисса. Его принцип был широко использован в стационарных двигателях, работающих на постоянной скорости с различной нагрузкой. В них управление «отсечением» поступающего пара и, как следствие, крутящего момента, осуществлялось центробежным регулятором и запорными клапанами.
После распространения тарельчатых клапанов была внедрена упрощённая система привода клапанов посредством распределительного вала. В подобных двигателях изменение «отсечения» могло быть достигнуто разным профилем кулачков, которые передвигались по распределительному валу регулятором[3].
Авиация[править | править код]
В раннем экспериментальном двигателе V8 разработки фирмы Clerget-Blin, развивавшем 200 л. с., для изменения момента открытия и закрытия клапаном, использовался скользящий распределительный вал. В некоторых видах звездообразных двигателей фирмы Bristol Jupiter начала 1920-х годов также имеется система изменения момента открытия и закрытия клапанов, которая в основном использовалась на впускных клапанах для достижения б́ольшей компрессии[4]. В двигателе Lycoming XR-7755 была установлена система изменения фаз газораспределения, состоящая из двух кулачков, которые могли быть выбраны пилотом: один для взлёта, ухода от погони и преследования, другой для экономичных полётов.
Автомобили[править | править код]
Желательность наличия системы, позволяющей изменять продолжительность открытия клапанов для его соответствия скорости вращения двигателя, стала очевидной в 1920-х годах, когда предел максимально достижимых рабочих оборотов двигателя стал увеличиваться. К тому времени обороты двигателя на холостом ходу и при его загрузке отличались несущественно, поэтому не было необходимости в изменении длительности открытия клапанов. Незадолго до 1919 года Лоуренс Помрой (англ. Lawrence Pomeroy), главный конструктор компании Vauxhall, разработал двигатель H-Type объёмом 4,4 л, предназначенный для замены существовавшей в то время модели 30-98[5]. В нём единственный распределительный вал мог перемещаться продольно, что позволяло использовать на нём различные профили. Первые патенты на системы изменения длительности открытия клапанов были выданы в 1920 году, например, патент США U.S. Patent 1 527 456.
В 1958 году компания Porsche подала в Германии, а также в Великобритании заявку на патент, который был опубликован под номером GB861369 в 1959 году. Патент Porsche описывал систему с колеблющимися кулачками, которые используются для увеличения высоты подъёма клапанов и времени их открытия. Десмодромные клапана приводятся в действие движущейся вверх-вниз тягой, соединённой с эксцентриковым валом или шайбовым механизмом. Неизвестно, был ли изготовлен хоть один рабочий прототип.
Первой компанией, запатентовавшей практически реализуемую на автомобилях систему изменения момент открытия и закрытия клапанов, включавшую систему изменения высоты подъёма клапанов, была Fiat. В системе, разработанной Джованни Торацца (итал. Giovanni Torazza) в конце 1960-х годов, гидравлическое давление использовалось для изменения точки опоры толкателей клапанов (U.S. Patent 3 641 988)[6]. Гидравлическое давление изменяется в зависимости от скорости работы двигателя и давления воздуха во впускном тракте. Обычное изменение момента открытия было 37 %.
Первой компанией, начавшей установку изменения момента открытия и закрытия клапанов на серийно изготовляемые автомобили, стала Alfa Romeo (U.S. Patent 4 231 330)[7]. Автомобили с системой впрыска топлива модели Alfa Romeo Spider в 1980-х годах комплектовались механической системой изменения фаз газораспределения. Она была разработана Джампаоло Гарчеа (итал. Giampaolo Garcea) в 1970-х годах[8]. Модели Alfa Romeo Spider, начиная с 1983 года, комплектуются электронной системой изменения фаз газораспределения[9].
В 1987 году свою систему изменения момента открытия и закрытия клапанов N-VCT представила компания Nissan для своих двигателей VG20DET и VG30DE[источник не указан 354 дня]. В 1989 свою систему VTEC также представила Honda[10]. Если ранние системы N-VCT от Nissan исключительно смещали фазы газораспределения, то в системе VTEC происходит переключения на другой профиль кулачка на высоких скоростях работы двигателя, чтобы увеличить максимальную мощность двигателя. Первым двигателем от Honda с системой VTEC был B16A, который устанавливался на модели Integra, CR-X и хэтчбеки Civic, поставляемые в Европу и Японию[источник не указан 354 дня].
В 1992 году Porsche представила систему VarioCam, которая стала первой системой с плавным изменением фаз газораспределения (все предыдущие системы были со ступенчатым их изменением). Система начала устанавливаться на автомобили Porsche 968 и работала только на впускных клапанах.
Мотоциклы[править | править код]
Системы изменения фаз газораспределения устанавливались на мотоциклетные двигатели, однако были приязненны бесполезными «техническими образцами» в конце 2004 года из-за увеличения веса при установке системы[11]. После этого были выпущены следующие мотоциклы с системами изменения фаз газораспределения: Kawasaki 1400GTR/Concours 14 (2007 г.), Ducati Multistrada 1200 (2015 г.) и BMW R1250GS (2019 г.).
Корабли и суда[править | править код]
Системы изменения фаз газораспределения имеют слабое распространение на корабельных двигателях. Корабельные двигатели от Volvo Penta с 2004 года комплектуются системой изменения фаз кулачков, управляемой ЭБУ двигателя, плавно изменяющей опережение или запаздывание распределительного вала[12].
Дизельные двигатели[править | править код]
В 2007 году Caterpillar разработал двигатели Acert серий С13 и С15, в которых система изменения фаз газораспределения используется для снижения выброса оксидов азота с целью избежать использования системы рециркуляции выхлопных газов после введения требований EPA в 2002 году[13].
В 2009 году компания Mitsubishi разработала и начала серийное производство двигателей I4 модели 4N13 с двумя распределительными валами объёмом 1,8 л. Этот двигатель стал первым в мире дизельным двигателем для легковых автомобилей с системой изменения фаз газораспределения[14].
У каждого производителя двигателей данная технология имеет своё название.
- AVCS (Subaru)
- AVLS (Subaru)
- CPS (Proton), однако на новых моделях с 2016 года Proton называет технологию VVT
- CVTCS (Nissan, Infiniti)
- CVVT (разработана компаниями Hyundai и Kia, также встречается на Geely, Iran Khodro, Volvo)
- DCVCP (General Motors)
- DVT (Ducati)
- DVVT (Daihatsu, Perodua, Wuling)
- MIVEC (Mitsubishi)
- MultiAir (Fiat/FPT)
- N-VCT (Nissan)
- S-VT (Mazda)
- Ti-VCT (Ford)
- VANOS (BMW)
- VALVETRONIC (BMW, PSA)
- VarioCam (Porsche)
- VCT (Alfa Romeo)
- VTEC, i-VTEC (Honda, Acura)
- VTi, (Citroen, Peugeot, BMW)
- VVC (MG Rover)
- VVL (Nissan)
- Valvelift (Audi)
- VVA (Yamaha)
- VVEL (Nissan, Infiniti)
- VVT (Chrysler, General Motors, Proton, Suzuki, Isuzu, Volkswagen Group, Toyota)
- VVT-i, VVTL-i (Toyota, Lexus)
Переключение кулачков[править | править код]
В этой реализации используются разные профили кулачков. В определённый момент (как правило, при определённой скорости работы двигателя) при помощи привода происходит переключение между профилями. При таком способе реализации изменения фаз газораспределения также возможно изменение высоты подъёма клапаном и изменение длительности открытия клапанов, однако это изменение всегда происходит ступенчато и плавным быть не может. Первым серийным представителем таких систем стала система VTEC компании Honda. В системе VTEC при помощи изменения гидравлического давления приводится в действие штырь, замыкающий в работу коромысло, отвечающее за высокий подъём клапанов и большое время открытия, с находящимся вблизи коромыслом, отвечающим за низкий подъём клапанов и малое время открытия.
Фазировка кулачков[править | править код]
Многие изготовляемые системы изменения фаз газораспределения работают по типу изменения фазировки кулачков посредством устройств, известных как жарг. фазовращатели (англ. variator). Это позволяет производить плавную регулировку, однако многие ранние подобные системы могли выполнять только ступенчатую регулировку. Однако, регулировка длительности открытия и высоты подъёма невозможна.
Колеблющиеся кулачки[править | править код]
В этой реализации используются колебательные или качающиеся движения частей кулачков[источник не указан 352 дня], которые выступают в роли толкателей. В свою очередь, толкатели открывают и закрывают клапана. В некоторых реализациях таких систем используется как традиционный профиль кулачков, так и эксцентриковые профили, и соединительные тяги. Принцип их действия подобен паровым двигателем, где объём пара, поступающего в рабочий цилиндр, регулируется моментом «отсечки» пара. Преимуществом таких систем заключается в плавном характере регулирования высоты подъёма клапанов и длительности открытия. Недостатком же является то, что подъём клапанов пропорционален длительности открытия, и их независимая регулировка невозможна.
Примерами подобных систем являются Valvetronic (BMW)[15], VVEL (Nissan) и Valvematic (Toyota), в них системы колеблющихся кулачков устанавливаются только на впускных клапанах.
Эксцентриковый привод кулачков[править | править код]
Системы с эксцентриковым приводом кулачков работают посредством эксцентрикового дискового механизма, который уменьшает и увеличивает угловые скорости профиля кулачков при их вращении. Уменьшение этой скорости во время, когда клапан открыт, соответствует увеличению длительности открытия клапана. Преимуществом такой системы является возможность независимой регулировки длительности открытия клапанов и высоты подъёма[16] (однако, в них невозможна регулировка подъёма). К недостаткам этих систем относится их сложность (необходимо устанавливать два эксцентриковых привода и два их контроллера на каждый цилиндр — по одной паре устройств на впускные и выпускные клапана), что увеличивает стоимость системы.
Единственным производителем, внедрившим такую системы, стал MG Rover.[источник не указан 352 дня]
Трёхмерный профиль кулачков[править | править код]
В этих системах кулачки имеют профиль, который также изменяется по их длине в форме[17], подобной конической. На одном конце кулачка представлен профиль с малой высотой подъёма клапанов и малым временем открытия, на другом конце — профиль с большой высотой подъёма клапанов и увеличенным временем открытия. В средней части длины кулачка осуществляется плавный переход между этими профилями. Плавная регулировка высоты подъёма клапанов и длительности открытия может быть осуществлена смещением места контакта толкателя клапана с профилем кулачка. Это достигается путём осевого перемещения распределительного вала («скольжением» вдоль двигателя), таким образом неподвижный толкатель клапанов будет контактировать с разными участками профиля кулачка, благодаря чему достигаются разные значения высоты подъёма клапанов и длительности открытия. Недостатком этих систем является крайне сложное проектирование профиля кулачков, поскольку конструкция должна обеспечивать минимальные контактные напряжения, возникающие из-за изменений профиля.
Обычно к использующим такую систему относят Ferrari[18][19], тем не менее остаётся доподлинно неизвестным, используются ли подобные системы в её серийных моделях.
Двухвальный комбинированный профиль кулачков[править | править код]
Об использовании этих систем в серийных двигателях информация отсутствует.
Система состоит их двух близко расположенных распределительных валов и поворотного толкателя, который приводится в действие обоими распределительными валами. Движение этого толкателя передаёт движение профилей кулачков обоих распределительных валов одновременно. Каждый распределительный вал оборудуется своей системой изменения фаз газораспределения, которых позволяют изменят угловое положение распределительных валов относительно коленчатого вала. Профиль кулачков на одном распределительном валу управляет закрытием клапанов, а профиль кулачков на другом распределительном валу — закрытием тех же клапанов. Таким образом, регулировка длительности открытия клапанов регулируется интервалом между этими событиями.
Среди недостатков таких систем можно выделить:
- При большой длительности открытия высота профиля на одном кулачке может начать уменьшаться, в то время как на другом — увеличиваться. Это будет приводить к суммарному уменьшению высоты профиля кулачков и может вызывать недостатки в динамике двигателя. Имеются патенты, посвящённые решению в некоторой степени проблемы неравномерной высоты открытия клапанов, тем самым делающие возможной работу системы на полной высоте профиля кулачков при большой длительности открытия клапанов[20][21][22].
- Из-за наличия в системе двух распределительных валов увеличиваются размеры системы, толкателей и других элементов.
Двухвальный комбинированный профиль кулачков с соосным расположением валов[править | править код]
Об использовании этих систем в серийных двигателях информация отсутствует.
Принцип работы системы также состоит в том, что один толкатель приводится в действие профилями кулачков, расположенных на двух разных распределительных валах. С точностью до ограничения по углу, обусловленного радиусом оконечного закругления толкателя, толкатель «ощущает» комбинацию поверхностей двух профилей кулачков как плавную, непрерывную поверхность. Когда вращение кулачков максимально выровнено, длительность открытия клапана минимальна и соответствует профилю каждого кулачка по отдельности. Наоборот, когда угол между кулачками при вращении наибольший, длительность открытия клапана максимальна. Основным ограничением подобных систем является то, что возможно только регулировка длительности открытия клапанов, равная (в градусах движения распределительного вала) закруглению профиля острого конца кулачка.
Подобный принцип лёг в основу, вероятно, первой запатентованной в 1925 году Ведомством по патентам и товарным знакам США системы изменения кулачков (U.S. Patent 1 527 456). Также к данном типу относится так называемый «распределительный вал Клемсона»[23].
Спиральный распределительный вал[править | править код]
Также «Двухвальный комбинированный профиль кулачков с соосным расположением валов и спиральным движением», об использовании этих систем в серийных двигателях информация отсутствует.
Принцип аналогичен ранее рассмотренному, в нём могут использоваться такого же профиля длительности. Однако вместо простого плоского поворота кулачков для регулировки используется совокупность осевого и поворотного движений, что является трёхмерным спиральным движением. Посредством такого движения преодолеваются ограничения, связанные с длительностью в ранее рассмотренной системе. Длительность открытия клапанов при этом теоретически не ограничена, однако обычно не составляет более 100 градусов движения распределительного вала, чего достаточно для работы в большинстве ситуаций.
По сообщениям, кулачки для таких системы сложны и затратны в изготовлении, требуется очень высокая точность при изготовлении спиральных элементов, а также должна быть обеспечена бережная сборка.
Двигатели без кулачков[править | править код]
К таким двигателям относятся те двигатели, которым не требуется распределительный вал для управления клапанами. Клапана в таких системах обладают высокой гибкостью для регулирования фаз газораспределения и высоты подъёма клапанов. Тем не менее, по состоянию на 2019 год не существует подобных систем, предназначенных для транспортных средств для дорог общего пользования.
Выделяют следующие типы двигателей без кулачков:
- электромеханические (с использованием электромагнитов)
- гидравлические
- пневматические
- с использованием шаговых двигателей.
- ↑ 1 2 Wu, B. (2007). A simulation-based approach for developing optimal calibrations for engines with variable valve actuation. Oil and Gas Science and Technology, 62(4), 539—553.
- ↑ 1 2 3 4 5 Hong, H. (2004). Review and analysis of variable valve timing strategies — eight ways to approach. Proceedings of the Institution of Mechanical Engineers, Part D: Journal of Automobile Engineering, 218(10), 1179—1200.
- ↑ Variable Valve Timing — 1886 — Practical Machinist (неопр.). Practical Machinist. Дата обращения 4 апреля 2010.
- ↑ Arthur W., Gardiner REPORT No. 272: THE RELATIVE PERFORMANCE OBTAINED WITH SEVERAL METHODS OF CONTROL OF AN OVERCOMPRESSED ENGINE USING GASOLINE (неопр.) (PDF). Langley Research Center/Langley Aeronautical Laboratory (25 февраля 1927).
- ↑ Coomber, Ian. Vauxhall: Britain’s Oldest Car Maker (неопр.). — Fonthill Media, 2017. — С. 46. — ISBN 978-1781556405.
- ↑ VALVE-ACTUATING MECHANISM FOR AN INTERNAL COMBUSTION ENGINE (неопр.). freepatentsonline.com. Дата обращения 12 января 2011.
- ↑ Timing variator for the timing system of a reciprocating internal combustion engine (неопр.). freepatentsonline.com. Дата обращения 12 января 2011.
- ↑ Alfa Romeo Spider FAQ (неопр.) (PDF). alfaspiderfaq.org. Дата обращения 29 ноября 2008.
- ↑ Rees, Chris. Original Alfa Romeo Spider (неопр.). — MBI Publishing 2001. — С. 102. — ISBN 0-7603-1162-5.
- ↑ asia.vtec.net
- ↑ Wade, Adam. Motorcycle Fuel Injection Handbook (неопр.). — MotorBooks International (англ.)русск., 2004. — С. 149—150. — ISBN 1610590945.
- ↑ Volvo Penta Variable Valve Timing (VVT) (неопр.). www.marineenginedigest.com. Дата обращения 27 октября 2012.
- ↑ [1]
- ↑ «Geneva 2010: Mitsubishi ASX (Outlander Sport) Debuts in Geneva», autoguide.com
- ↑ Autospeed Valvetronic Article (неопр.). Дата обращения 17 января 2012.
- ↑ Rover VVC Article (неопр.). Дата обращения 17 января 2012.
- ↑ howstuffworks.com
- ↑ Lumley, John L. Engines — An Introduction (неопр.). — Cambridge UK: Cambridge University Press, 1999. — С. 63—64. — ISBN 0-521-64277-9.
- ↑ HowStuffWorks — Ferrari 3D cam article (неопр.). Дата обращения 17 января 2012.
- ↑ USPTO 5052350 (неопр.). Дата обращения 17 января 2012.
- ↑ USPTO 5642692 (неопр.). Дата обращения 17 января 2012.
- ↑ Mechadyne VLD (неопр.). Дата обращения 17 января 2012.
- ↑ USPTO 4771742 (неопр.). Дата обращения 17 января 2012.
Преимущества и недостатки верхнего расположения клапанов
Стр 1 из 4Следующая ⇒ЛАБОРАТОРНАЯ РАБОТА № 3.
МЕХАНИЗМ ГАЗОРАСПРЕДЕЛЕНИЯ
Преимущества и недостатки верхнего расположения клапанов
К недостаткам верхнего расположения клапанов следует отнести усложнение механизма газораспределения при нижнем расположении распределительного вала или усложнение привода к нему при верхнем расположении последнего, а также увеличение высоты головки цилиндра, что при вертикальном расположении цилиндров приводит к увеличению высоты, а при горизонтальном – ширины двигателя. В короткоходных двигателях последний недостаток сказывается меньше вследствие небольшой высоты блока и картера. При верхнем расположении клапанов камера сгорания получается более компактной, с относительно малой поверхностью охлаждения, вследствие чего уменьшаются потери в систему охлаждения и увеличивается индикаторный КПД двигателя. Компактность камеры сгорания уменьшает опасность детонации и позволяет при том же октановом числе бензина увеличить степень сжатия примерно на пол-единицы по сравнению с двигателями, имеющими нижние клапаны, что также оказывает положительное влияние на увеличение индикаторного КПД. Все это вместе взятое, а также применение высокооктанового бензина позволяет в настоящее время достигнуть высокой топливной экономичности автомобильных бензиновых двигателей, приближающейся к экономичности дизелей с разделенными камерами сгорания. Простая форма впускного канала с малым гидравлическим сопротивлением, а также возможность увеличения площади проходного сечения клапанов за счет увеличения числа клапанов или расположения их под углом к оси цилиндра повышают коэффициент наполнения на 5–7%, что создает более широкие возможности для форсирования двигателя по числу оборотов.
Как отличить впускной и выпускной каналы по размерам, почему они различаются?
Что бросается в глаза — это неточная стыковка отверстий каналов коллекторов и ГБЦ. Любые «ступеньки» в канале рождают паразитные завихрения, заметно тормозящие поток, поэтому от них необходимо избавиться. Убираем нестыковки, одновременно доработав прокладки под коллектора (дабы пресловутых ступенек не создавали и они). Настоятельно рекомендую перед удалением нестыковок каналов сделать следущее — посадить коллектора на штифты. Причиной тому служит крепёж коллекторов на отечественных автомобилях, допускающий некоторое смещение плоскостей коллекторов и ГБЦ друг относительно друга. Чем это грозит, предельно ясно — немного сместив коллектора при крепеже после удаления нестыковок, мы самостоятельно убиваем плоды своей же работы. Штифтов достаточно по два на коллектор — по краям. Ищем место на ГБЦ и коллекторе, где можно безопасно всверлиться. В ГБЦ прочно сажаем металлический штифт, на который легко, но без особых люфтов должен надеваться коллектор — вуаля, точное позиционирование коллекторов относительно ГБЦ нам гарантировано. Не забудьте только сделать несколько дополнительных отверстий в прокладке. Отмечу так же, что если диаметр канала впускного коллектора меньше диаметра канала ГБЦ на 1-1,5 мм при нормальной соосности каналов, то это не создаст измеримого сопротивления прохождению потока, поэтому филигранной подводкой диаметров каналов в этом случае можно принебречь. На выпуске аналогично, только наоборот — выпускной канал в ГБЦ может быть несколько меньше канала в выпускном коллекторе. Более того, т.к. называемые «обратные ступеньки» на выпуске используют для борьбы с некоторыми негативными явлениями настроенной выпускной системы, но сейчас разговор не об этом.
Перечислите преимущества и недостатки нижнего расположения клапанов
Нижнее расположение клапанов применялось только в карбюраторных и газовых двигателях. При этом высота головки цилиндров и всего двигателя уменьшается, а привод распределительного вала и клапанов упрощается, но ограничивается возможность повышения степени сжатия (до 7,5) и ухудшаются технико-экономические показатели двигателя.
Нижние клапаны размещают с одной стороны блока цилиндров в один ряд и обычно чередуют так же, как и верхние клапаны при расположении их в один ряд.
Почему невозможно применение нижнего расположения клапанов в дизелях?
В дизелях возможно только верхнее расположение клапанов, так как относительно малый объем камеры сгорания, получающийся при высоких значениях степени сжатия, не позволяет разместить клапаны сбоку цилиндра. В бензиновых двигателях возможно как верхнее, так и нижнее расположение клапанов.
Какая основная причина обусловливает верхнее расположение распредилительного вала?
В современных высокооборотных двигателях легковых автомобилей ВАЗ «распределительный вал установлен на головке блока цилиндров, что упрощает кинематическую связь между кулачками и клапанами. Такое расположение распределительного вала называется верхним, оно позволяет упростить блок цилиндров и уменьшить шум при работе механизма газораспределения. При верхнем расположении распределительный вал приводится цепью или зубчатым ремнем.
Как регулируется тепловой зазор при непосредственном приводе клапанов от распределительного вала?
Тепловые зазоры между кулачками и рычагами впускных и выпускных клапанов должны быть равны:
– 0,15 мм – на холодном двигателе;
– 0,20 мм – на прогретом двигателе.
ПОРЯДОК ВЫПОЛНЕНИЯ
— Снять крышку головки блока цилиндров с прокладкой.
— Вращая коленчатый вал (специальным ключом) по часовой стрелке, совместить установочную метку (1) на звездочке распределительного вала с установочным приливом (2) на корпусе подшипников распределительного вала. При этом поршень четвертого цилиндра находится в ВМТ в конце такта сжатия и оба клапана закрыты.
— Отрегулировать зазоры между рычагами и кулачками распределительного вала у выпускного клапана четвертого цилиндра (восьмой кулачок) и впускного клапана третьего цилиндра (шестой кулачок).
— Для этого необходимо ослабить контргайку (3) регулировочного болта и, вращая регулировочный болт (2), проверить требуемый зазор плоским щупом (1), вставленным между кулачком и рычагом.
— Удерживая в этом положении ключом регулировочный болт, затянуть контргайку и вновь проверить зазор. Щуп должен перемещаться в зазоре с легким защемлением.
— Проворачивая коленчатый вал на 1/2 оборота, отрегулировать зазоры в определенной последовательности.
— Установить крышку на место.
Перечислите преимущества наклонного расположения клапанов по отношению к оси цилиндра
В случае верхнего расположения клапанов коэффициент наполнения может быть на 5—7% больше, чем при нижнем расположении клапанов. Это достигается с помощью увеличения числа клапанов или расположения их под углом к оси цилиндра.
С какой скоростью вращается распределительный вал двух и –четырехтактного двигателя по отношению к коленчатому валу?
ТНВД точно так же как и коленчатый вал, для синхронности и сохранения фазы впрыска , ну а распределительный вал в 2 раза медленнее.
Почему для дизельного двигателя предпочтительным является расположение впускных и выпускных каналов на противоположных сторонах головки цилиндров?
Впускные и выпускные каналы выведены на противоположные боковые стороны головки. В местах выхода каналов предусмотрены фланцы и резьбовые отверстия для крепления впускного и выпускного коллекторов. Охлаждающая жидкость поступает в головку цилиндров из блока цилиндров через сверления в нижней плите головки (по три отверстия на каждый цилиндр).
Одно отверстие каждой группы выходит в поперечный канал, создающий направленный поток охлаждающей жидкости к наиболее нагретым местам головки между стаканом форсунки и выпускным клапаном. Отводится охлаждающая жидкость от головки через отверстия со стороны воздушного кол-Лектора. В этом месте на боковой плоскости головки предусмотрены фланцы и резьбовые отверстия для крепления водоотводящей трубы.
ЛАБОРАТОРНАЯ РАБОТА № 3.
МЕХАНИЗМ ГАЗОРАСПРЕДЕЛЕНИЯ
Преимущества и недостатки верхнего расположения клапанов
К недостаткам верхнего расположения клапанов следует отнести усложнение механизма газораспределения при нижнем расположении распределительного вала или усложнение привода к нему при верхнем расположении последнего, а также увеличение высоты головки цилиндра, что при вертикальном расположении цилиндров приводит к увеличению высоты, а при горизонтальном – ширины двигателя. В короткоходных двигателях последний недостаток сказывается меньше вследствие небольшой высоты блока и картера. При верхнем расположении клапанов камера сгорания получается более компактной, с относительно малой поверхностью охлаждения, вследствие чего уменьшаются потери в систему охлаждения и увеличивается индикаторный КПД двигателя. Компактность камеры сгорания уменьшает опасность детонации и позволяет при том же октановом числе бензина увеличить степень сжатия примерно на пол-единицы по сравнению с двигателями, имеющими нижние клапаны, что также оказывает положительное влияние на увеличение индикаторного КПД. Все это вместе взятое, а также применение высокооктанового бензина позволяет в настоящее время достигнуть высокой топливной экономичности автомобильных бензиновых двигателей, приближающейся к экономичности дизелей с разделенными камерами сгорания. Простая форма впускного канала с малым гидравлическим сопротивлением, а также возможность увеличения площади проходного сечения клапанов за счет увеличения числа клапанов или расположения их под углом к оси цилиндра повышают коэффициент наполнения на 5–7%, что создает более широкие возможности для форсирования двигателя по числу оборотов.
Какими достоинствами и недостатками обладает ГРМ с нижним расположением распредвала и верхним расположением клапанов ?
Такой привод распределительного вала не требует регулировки и бесшумен при работе, имеет большой ресурс. Однако верхнее расположение клапанов приводит к усложнению их привода от распредвала, введение в конструцию штанг толкателей, коромысел…
вот тя прет! что не учишь теорию совсем! мозги всем паришь
Это просто конструктивное различие. А плюсы и минусы есть везде.
самый большой недостаток- большие инерционные массы и много деталей
ГРМ состоит из следующих основных элементов : распределительного вала, толкателей, штанг, одно- или двуплечих рычагов (коромысел) , клапанов и их пружин. Распределительный вал имеет кулачки — выступы определенного профиля, задающие порядок и время открытия и закрытия клапанов. Он может быть расположен в нижней части блока цилиндров (нижнее расположение) или в его головке (верхнее расположение) и приводится во вращение от коленчатого вала. При нижнем расположении распредвала усилие, необходимое для открытия клапанов, передается к ним от кулачков через толкатели, штанги и коромысла. В ГРМ с верхним расположением распределительного вала привод клапанов осуществляется кулачком либо непосредственно через толкатели, либо через рычаги или коромысла. В процессе прогрева двигателя (от температуры окружающего воздуха до рабочей температуры) детали ГРМ нагреваются, что вызывает увеличение их размеров. Это может привести к тому, что клапан перестанет плотно закрываться. Чтобы избежать такого эффекта, в клапанном механизме предусмотрен тепловой зазор (для впускных клапанов — от 0,15 до 0,25 мм, для выпускных — от 0,20 до 0,35 мм и более) . При эксплуатации двигателя происходит износ деталей ГРМ, приводящий к увеличению теплового зазора. Поэтому периодически возникает необходимость в его регулировке, операции довольно трудоемкой и ответственной. Неправильно установленный тепловой зазор приводит к неплотному закрыванию клапанов или характерному металлическому стуку, вызывающему повышенный износ деталей ГРМ и как следствие — ремонт автомобиля. Гидравлические компенсаторы зазоров в ГРМ обеспечивают его безударную работу и полное закрытие клапанов.
Сейчас двигатели с нижним расположением распредвала наверное уже не выпускают. Слишком много там деталей, регулировок .
В обоих вариантах есть и преимущества и недостатки. Сейчас по моему с нижним расположением и не выпускают, а основное его преимущество отсутствие ремня. Крутящий момент передается от вала к распредвалу шестерней. А плохая сторона, нет возможности ремонта клапанов без снятия двигателя. Ремонт верхнего расположения намного облегчен.
В чем различие ГРМ с верхним и нижним расположением клапанов ?
нижним расположением клапанов в блоке (газ-69 или газ 51 и зил 120), верхнее -в головке (зил-130, газ-53, волга). Есть еще нижнее и верхнее расположение распредвала (газ-24 и москвич-412, ваз 2101).
Газораспределительными механизмами с верхним расположением клапанов оснащены практически все современные двигатели. Эта конструкция постепенно сменила нижнеклапанную в середине шестидесятых годов, в начале «гонки за лошадиными силами». Применение верхнеклапанного механизма позволило избавиться от лишних передаточных деталей. Кулачки распредвала, надавливающие непосредственно на штоки клапанов, позволили обеспечить устойчивую работу двигателя на высоких оборотах. Кроме того, верхнее расположение клапанов позволило упростить ремонт и обслуживание двигателя. Верхнее расположение распредвала позволило уменьшить массу двигателя и снизить уровень шума при его работе. В конечном итоге, благодаря переходу на верхнеклапанную конструкцию, инженерам удалось увеличить количество клапанов (16, 24 и более), установив вместо одного распредвала два — для каждой группы клапанов. Единственным минусом конструкции можно считать только относительную сложность привода, который осуществляется ремнем или цепью. если подробно и с картинками-то тут <a rel=»nofollow» href=»http://dobrovolskij.ru/index.php/obuchayushchemusya/ustrojstvo-to-i-remont-avtomobilej/soderzhanie-obucheniya-na-1-kurse/36-tema-13-gazoraspredelitelnyj-mekhanizm.html» target=»_blank»>http://dobrovolskij.ru/index.php/obuchayushchemusya/ustrojstvo-to-i-remont-avtomobilej/soderzhanie-obucheniya-na-1-kurse/36-tema-13-gazoraspredelitelnyj-mekhanizm.html</a>
Если кратко, то нижние распредвалы устанавливались на низкооборотистых двигателях прошлого века. Они имели длинные штанги (тяги) привода клапанов, что утяжеляло вес, ухудшало вибробаланс, что не мало важно в более оборотистых двигателях….
В том что различные ролики отвечают каждый за свое положение и натяжители там разные. На <a rel=»nofollow» href=»https://karpoff.com.ua» target=»_blank»>https://karpoff.com.ua</a> не так давно покупал комплект ГРМ и могу сказать что отличия в роликах всегда заметны невооруженным глазом даже. Так что мой совет вам у мастеров поставить этот ремень что бы не было никаких проблем.