Ремонт и восстановление деталей автомобиля
Ремонт деталей представляет собой восстановление всех геометрических размеров детали, ее формы и расположения поверхностей, а также обеспечение физико-механических свойств в сравнении с новой деталью. Кроме этого при ремонте решается задача повышения долговечности и работоспособности детали. При ремонте автомобилей нашли широкое применение следующие способы восстановления деталей: механическая обработка, сварка, наплавка, напыление металлов, химическая и гальваническая обработка.
Механическая обработка применяется для снятия припуска на обработку после наплавки, сварки, напыления и т. д.; для придания детали заданных геометрических форм; для установки дополнительных ремонтных деталей; обработки одной из сопряженных деталей при ремонте под ремонтные размеры. После механической обработки деталь, как правило, имеет необходимые геометрические размеры, но не обладает требуемыми физико-механическими свойствами. Поэтому некоторые детали после механической обработки проходят термическую обработку, в результате которой они приобретают необходимые физико-механические свойства.
Наплавочные работы широко применяются при восстановлении изношенных деталей. Сущность наплавки сводится к тому, что при помощи источника нагрева присадочный металл расплавляется и переносится на наплавляемую поверхность восстанавливаемой детали. При этом происходит частичное расплавление поверхностного слоя основного металла детали, который вместе с расплавленным присадочным металлом образует слой наплавленного металла.
Наплавочные работы могут осуществляться различными способами, основными из которых являются: ручная дуговая наплавка, автоматическая дуговая наплавка под флюсом, наплавка в среде углекислого газа, вибродуговая наплавка, а также плазменная и газовая наплавка.
При большом объеме восстановительных работ рекомендуется применять автоматическую наплавку под флюсом. Сущность такого способа заключается в том, что сварочная дуга горит под слоем флюса, в результате этого выделяется тепло, которое расплавляет электродную, проволоку, слой основного металла детали, а также флюс. Расплавленный металл электрода вступает во взаимодействие с основным металлом детали, в результате этого образуется слой наплавленного металла. С удалением сварочной дуги расплавленный флюс затвердевает, при этом образуется шлаковая корка, которая легко отделяется от металла. На выбор марки электродной проволоки для наплавки влияют требуемые физико-механические свойства металла.
Достаточно широкое применение получила наплавка в среде углекислого газа. Сущность этого метода состоит в том, что сварочная дуга горит в среде углекислого газа, в результате этого расплавленный металл не контактирует с воздухом. Наплавка в среде углекислого газа имеет следующие преимущества перед наплавкой под флюсом: меньший нагрев детали, более высокая производительность, возможность восстановления деталей небольших размеров, возможность совмещения наплавки с термической обработкой. К недостаткам наплавки в среде с углекислым газом относится то обстоятельство, что легирование наплавленного металла ограничивается химическим составом электродной проволоки.
Кроме вышеперечисленных методов наплавки широко применяется метод плазменной наплавки. Сущность этого метода заключается в расплавлении присадочного металла струей плазмы и перенесении его на поверхность восстанавливаемой детали. Достоинствами такого метода наплавки являются возможность регулирования температуры нагрева металла, малая глубина зоны термического влияния, высокое качество наплавляемого металла, а также высокая производительность труда. Недостатком этого способа наплавки являются более высокие требования по электробезопасности при выполнении наплавочных работ.
При ремонте автомобилей достаточно редко применяется способ газовой наплавки металла. Этот способ применяется в основном при индивидуальном выполнении ремонтных работ из-за трудности механизации выполнения работ. Наплавка металла производится при помощи газового пламени, которое образуется при сгорании кислорода в среде ацетилена. Температура пламени в зоне ядра достигает 3100-3200 °С. Достоинством газовой наплавки по сравнению с дуговой наплавкой является возможность регулирования температуры нагрева, а также возможность проведения последующей термической обработки. К недостатку этого способа относится высокая трудоемкость процесса, высокая стоимость, а также большая зона термического влияния.
В зависимости от источника нагрева напыление может быть газопламенным, электродуговым, плазменным и т. д.
При газопламенном напылении расплав напыляемых частиц осуществляется газовым пламенем, а распыление — сжатым воздухом. В роли горючего газа выступает чаще всего пропан-бутан, а также природный газ, ацетилен. В качестве напыляемого материала могут выступать порошок, проволока сплошного сечения, а также порошковая проволока. Достоинства этого метода — в небольшом окислении и в достаточной прочности и долговечности получаемого покрытия. Недостатком этого метода является малая производительность.
При электродуговом напылении распыление расплавленного металла осуществляется при помощи сжатого воздуха, а расплавление проволоки — электрической дугой. Достоинством этого способа является его простота по равнению с другими. Недостатком является низкое качество получившегося покрытия из-за интенсивного окисления, а также выгорание значительного количества материала.
Наиболее широкое применение получил метод плазменного напыления. Расплавление материала осуществляется плазмой. Достоинства плазменного напыления: высокое качество покрытия, высокая производительность, возможность регулирования параметров процесса напыления. Недостатки: невысокий КПД процесса, а также высокая электроопасность.
Гальваническое покрытие получают при переносе металла из раствора электролита на деталь. Этот процесс проходит при пропускании через раствор электролита электрического тока. В роли катода выступает деталь, а в роли анода — металлическая пластина.
Технология восстановления деталей агрегатов автомобиля и трактора
Содержание страницы
Обеспечение ремонтных предприятий запасными частями осуществляется за счет изготовления новых запасных частей и путем восстановления деталей, бывших в эксплуатации. Большую часть номенклатуры восстанавливаемых деталей составляют гладкие и шлицевые валы, оси и крестовины. В большинстве случаев именно эти детали лимитируют ресурс узлов агрегатов машин. При восстановлении этих деталей необходимо обеспечить следующие требования: точные размеры и шероховатость, твердость поверхности, сплошность покрытия, прочность сцепления нанесенных слоёв с основным металлом, а также симметричность и соосность сопрягаемых поверхностей, отсутствие радиального и торцового биений. Из всех известных способов восстановления деталей наплавка способна удовлетворить все вышеперечисленные требования. Этот способ восстановления по сравнению с другими дает возможность получать на поверхности детали слой необходимой толщины и нужного химического состава, высокой твёрдости и износостойкости. Номенклатура основных деталей агрегатов автомобилей, подлежащих восстановлению сваркой и наплавкой, приведена в табл. 1.
Таблица 1
Восстанавливаемые детали автомобиля
Наименование | Восстанавливаемая поверхность |
Поворотная цапфа | Шейки под внутренний и наружный подшипники |
Распределительный вал | Опорные шейки |
Коленчатый вал | Шатунные и коренные шейки вала |
Впускные и выпускные клапаны | Торец клапанов и фаска тарелки |
Блок цилиндров | Опорные поверхности коренных подшипников |
Головка блока цилиндров | Плоскость разъема, отверстия под клапаны |
Гильза цилиндров | Посадочные пояски |
Трансмиссионные валы | Опорные шейки |
Картер коробки передач | Отверстия под подшипники ведущего, ведомого и промежуточного валов |
Картер редуктора заднего моста | Отверстия под подшипники ведущего конического зубчатого колеса. Отверстия под гнезда подшипников ведущего цилиндрического зубчатого колеса. Отверстия под подшипники дифференциала |
Гнездо подшипника ведущего цилиндрического зубчатого колеса редуктора заднего моста. Крестовины карданного вала | Наружные и внутренние посадочные поверхности. Наружные поверхности шипов |
Насос системы охлаждения ДВС | Валик водяного насоса |
В общем виде технология восстановления включает такие основные пункты: мойка, дефектация, подготовка технологических баз, наплавка изношенных поверхностей или заварка трещин, сколов и прочих, механическая, термическая и финишная обработка, контроль качества.
Восстановление валика водяного насоса
Одной из часто восстанавливаемых деталей машин является валик водяного насоса. Валик передает вращение от вала вентилятора к крыльчатке, которая перегоняет охлаждающую жидкость в системе охлаждения ДВС. Крыльчатка крепится к левому концу валика и закрепляется на нем посредством сегментной шпонки и гайки (рис. 1).
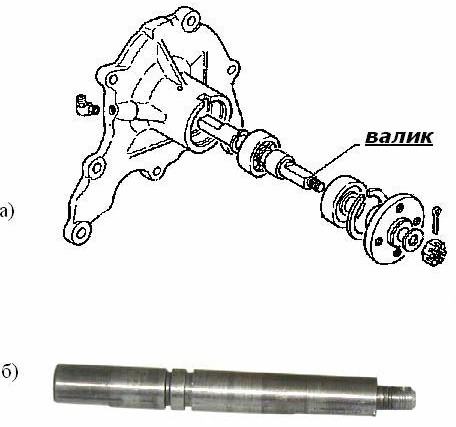
Рис. 1. Валик водяного насоса: а – схема валика в сборке; б – внешний вид
Повышенные требования при эксплуатации и ремонте должны предъявляться к поверхностям под подшипник и сальниковое уплотнение, так как неудовлетворительное (изношенное) состояние данной цилиндрической поверхности может вызвать протекание охлаждающей жидкости и попадание ее в масло, что может вызвать выход двигателя из строя.
Напряжения, которые испытывает валик, носят скручивающий характер.
Валик изготовлен из качественной стали типа Ст45, с твердостью заготовки НВ 241…285, часть данной детали закаливается (ТВЧ) и при этом закаленный слой имеет твердость HRC 52…62.
Анализ дефектов детали и способы ее восстановления приведены в табл. 2.
Таблица 2
Способы восстановления валика
Название дефекта | Метод или прибор контроля | Способ устранения дефектов |
1. Износ поверхности под подшипник и сальниковый уплотнитель | Штангенциркуль | Хромирование в саморегулирующемся электролите |
2. Износ шпоночной канавки | Визуально | Электроимпульсная наплавка |
3. Износ резьбы М14×1,5 кл. 2 | Визуально, резьбовой шагомер | Железнение с нанесением сплава |
Подготовка детали к нанесению покрытия
Подготовка детали включает следующие операции: механическую обработку поверхностей, подлежащих наращиванию; очистку деталей от окислов и предварительное обезжиривание; монтаж деталей на подвесное приспособление; изоляцию поверхностей, не подлежащих покрытию; обезжиривание деталей с последующей промывкой в воде; анодную обработку.
Предварительная механическая обработка детали имеет цель придать восстанавливаемым поверхностям правильную геометрическую форму. Производится эта обработка в соответствии с рекомендациями по механической обработке соответствующего материала. Очистку деталей от окислов с целью «оживления» поверхности проводят шлифовальной шкуркой или мягкими кругами с полировальной пастой. Предварительное обезжиривание деталей производят путем промывки в растворителях. После обезжиривания детали промывают в горячей, а затем в холодной воде. Сплошная, без разрывов, пленка воды на обезжиренной поверхности свидетельствует о хорошем качестве удаления жиров. Декапирование (анодную обработку) производят для удаления тончайших оксидных пленок с поверхности детали и обеспечения наиболее прочного сцепления гальванического покрытия с подложкой. Эта операция непосредственно предшествует нанесению покрытия.
Обработка детали после нанесения покрытия
Обработка включает следующие операции: нейтрализацию деталей от остатков электролита; промывку деталей в холодной и горячей воде; демонтаж деталей с подвесного приспособления и удаление изоляции; механическую обработку детали до требуемого размера; термическую обработку.
Так, если детали подвергались хромированию, то их сначала промывают в ванне с дистиллированной водой (для улавливания электролита), а затем – в проточной воде, после чего погружают на 0,5…1 мин в 3 %-ный раствор кальцинированной соды (для нейтрализации остатков электролита) и окончательно промывают в теплой воде. Затем детали снимают с подвесных приспособлений, удаляют с них изоляцию и сушат в сушильном шкафу при температуре 120…130 С. В некоторых случаях для снятия внутренних напряжений в хромовых покрытиях детали проходят термообработку с нагревом до 180…200 С в масляной ванне и выдержкой при этой температуре в течение 1…2 ч. Последовательность операций восстановления приведена в табл. 3.
Таблица 3
Схема технологического процесса
Операция | Оборудование и инструменты |
1. Моечная. Мойка и очистка валика от масла и грязи | Моечная машина. ew 30 olympus optical |
2. Дефектовочная. Выявление изношенных поверхностей и резьбы | Штангенциркуль, шагомер резьбовой |
3. Наплавочная. Наплавка поверхности шпоночной канавки | Установка для автоматической наплавки. Weld Lathe 613 |
4. Предохранительная. Защита поверхностей от действия электролита | Установка для защиты винипластовыми материалами |
5. Наращивающая. Наращивание диаметра вала | Гальваническая ванна |
6. Предохранительная. Защита поверхностей от действия электролита | Установка для защиты винипластовыми материалами |
Операция | Оборудование и инструменты |
7. Наращивающая. Восстановление резьбы | Гальваническая ванна |
8. Слесарная. Правка шпоночной канавки | Слесарный станок и инструмент. |
9. Шлифовальная. Шлифовка валика | Круглошлифовальный станок. BHA75CNC d 75 mm L 150 mm |
10. Резьбонарезная. Прогонка резьбы плашкой | Токарный станок. Pinacho – модель taurus 310 |
Технология восстановления и упрочнения рабочей поверхности крестовины автомобиля КамАЗ
Крестовины карданного вала изготавливаются из стали 18ХГТ и имеют твердость HRC 58…64. Крестовины в процессе работы подвергаются механическому изнашиванию и усталостному разрушению. Усталостное разрушение проявляется в виде трещин и поломок от длительного воздействия переменных нагрузок. Вначале возникают микроскопические трещины, которые затем развиваются вглубь детали, охватывая значительную часть сечения. Вследствие механического изнашивания появляется износ наружных поверхностей шипов.
При восстановлении деталей на ремонтных предприятиях применяются различные способы с помощью наплавки. Для восстановления крестовины рассмотрим вибродуговую наплавку, так как этот способ оказывает наименьшее термическое влияние, вследствие чего деталь практически не деформируется.
Сущность процесса автоматической вибродуговой наплавки была рассмотрена в главе 3 учебного пособия, поэтому здесь приведем только технологический процесс восстановления поверхности изделия.
Деталь закрепляется в центрах токарного станка. Отрицательный полюс источника питания постоянного тока (например, ВС-300) присоединён к детали, положительный полюс соединен с электродом. При включении источника питания между деталью и электродом возбуждается дуга, под действием которой плавится основной металл и металл электрода. Во время наплавки деталь вращается с заданной скоростью, а электродная проволока по мере расплавления непрерывно подается к детали. При этом электрод совершает
также и поступательное движение вдоль оси детали, подобно резцу токарного станка. Металл наплавляется по винтовой линии. В процессе наплавки электрод вибрирует с частотой 50…100 колебаний в секунду. Это достигается с помощью вибратора. По трубке в зону дуги подаётся охлаждающая жидкость. В результате быстрого охлаждения наплавленный слой закаляется, его твёрдость и износостойкость возрастают. Охлаждающая жидкость защищает расплавленный металл от вредного воздействия кислорода и азота воздуха.
Оборудование для наплавки
Вибродуговую наплавку производят на специальных установках, основными элементами которых являются токарный станок с наплавочной головкой вместо резцедержателя и источник питания дуги. Для наплавки может использоваться токарно-винторезный станок модели 1И611П или 1К62. Наплавочная головка – важнейший механизм установки для вибродуговой наплавки. Головка обеспечивает одновременную подачу электродной проволоки к детали и вибрацию конца проволоки. От конструктивного совершенства и качества исполнения головки зависит качество восстановленной детали. Обычно используется наплавочная головка ОКС-6569М.
Подготовка поверхности к наплавке
Состояние наплавляемой поверхности существенно влияет на количество восстановленных деталей. Если поверхность наплавляемой детали загрязнена или покрыта ржавчиной, то в наплавленном металле будут шлаковые включения и несплавления. Наплавка на поверхность, покрытую маслом, приведёт к появлению газовых пор. Все эти дефекты могут стать очагами разрушения детали, причиной её преждевременного выхода из строя. Вот почему наплавляемые места должны предварительно промываться и очищаться с помощью металлических щеток, наждачной бумаги и ветоши.
Установка детали
После того как деталь подготовлена к наплавке, её устанавливают в центрах токарного станка (рис. 2). Для этого используют круглый стержень сплошного сечения диаметром 40 мм. Стержень специально затачивается под отверстие в шипах крестовины. Конусное окончание позволяет закреплять деталь по центру. Стержень зажимается в кулачковом патроне токарного станка. Деталь подпирают центром задней бабки, который также имеет конусное окончание. Такое закрепление является достаточно надежным в данном случае, так как усилия, создаваемые наплавочной головкой, невелики.
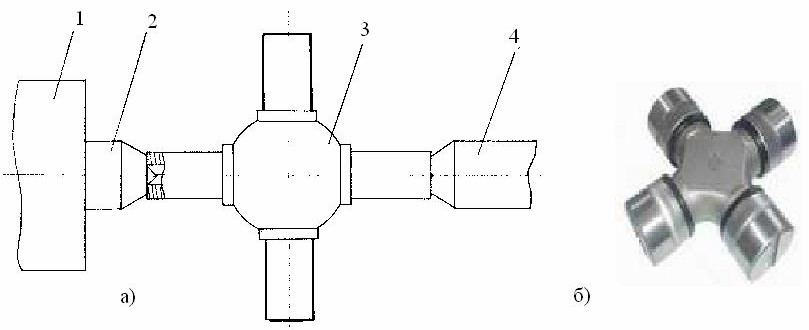
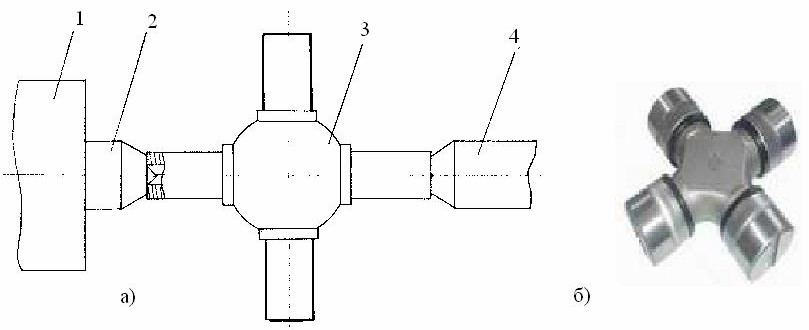
Рис. 2. Восстанавливаемая крестовина карданного вала: а – схема закрепления для наплавки; б – внешний вид крестовины после восстановления; 1 – зажимной патрон; 2 – центр; 3 – крестовина; 4 – задняя бабка станка
Режимы наплавки
Режим вибродуговой наплавки характеризуется силой тока, напряжением на дуге, скоростью подачи и диаметром электродной проволоки, шагом наплавки, расходом охлаждающей жидкости, частотой вибрации электрода. Все эти параметры, как правило, взаимосвязаны, и качество наплавленного слоя определяется именно правильно выбранным соотношением между указанными параметрами.
Вибродуговую наплавку обычно производят при напряжении на дуге от 12 до 40 В. Уменьшение напряжения на дуге приводит к увеличению времени короткого замыкания. Вследствие этого уменьшается общее количество выделяющегося тепла. Это, в свою очередь, приводит к уменьшению степени расплавления основного металла и в конечном счете к полному или частичному несплавлению.
Чрезмерное увеличение напряжения на дуге также приводит к нежелательным результатам: возрастает удар и разбрызгивание металла, деталь перегревается, сильнее коробится. При дальнейшем росте напряжения нарушается равенство в скоростях подачи проволоки и её расплавление. Наплавку постоянным током всегда ведут на обратной полярности: положительный, полюс источника тока присоединяется к электроду, отрицательный к детали.
Скорость подачи проволоки, которая обеспечивает качественный наплавленный слой, находится в пределах 0,9…1,65 м/мин. С увеличением скорости подачи проволоки увеличивается сила тока. Величина сварочного тока определяется внешней вольт-амперной характеристикой источника питания, скоростью подачи и диаметром проволоки. Для вибродуговой наплавки характерны средние значения силы тока 100…200 А.
Размах вибрации электрода выбирается в зависимости от диаметра электродной проволоки и обычно равен ему. Шаг наплавки зависит от диаметра электродной проволоки, напряжения на дуге и скорости ее подачи: обычно он соответствует диаметру проволоки.
От расхода охлаждающей жидкости, подаваемой на деталь, зависят величина ее коробления, твердость наплавленного металла, химический состав, а также вероятность появления пор и трещин. Обычно расход жидкости составляет 0,5…3 л/мин.
Высокое качество наплавки крестовины получают при использовании следующих режимов:
- шаг наплавки – 2,8 мм/об.;
- скорость подачи электрода – 1,25 м/мин;
- частота вибрации – 100 Гц;
- амплитуда колебаний – 1,95…2,6 мм;
- толщина наплавленного слоя, при которой обеспечивается надёжное сплавление – 2,5 мм.
Наплавка
После необходимой подготовки детали и выбора режима наплавки включают установку. Сначала включается двигатель станка и насос, подающий жидкость. Затем устанавливают нужное число оборотов детали, включают источник питания дуги и, руководствуясь показаниями вольтметра, регулируют напряжение. Далее конец электродной проволоки подводится к детали, суппорт станка включается, приводятся в действие вибратор и двигатель, подающий проволоку. Так начинается процесс наплавки. По окончании вибродуговой наплавки подача проволоки выключается. Выключение всех остальных механизмов производится в последовательности, обратной последовательности включения.
Контроль качества
При вибродуговой наплавке контроль осуществляется на всех стадиях процесса. Перед наплавкой внешним осмотром выявляются поверхностные дефекты деталей. В процессе наплавки контролируются расход и место подвода охлаждающей жидкости, напряжение на дуге, наличие проскальзывания электродной проволоки в роликах и т. п. Внешний осмотр и обмер наплавленной детали осуществляются дважды: непосредственно после наплавки и после механической обработки. В первом случае проверяются толщина наплавленного слоя, его чистота, наличие открытых пор, пропусков наплавки, крупных трещин чрезмерного коробления, правильность наплавки галтелей, величина припуска на механическую обработку. Часть обнаруженных дефектов поддается исправлению. Прерывистость слоя легко исправить местной ручной дуговой наплавкой. Недостаточная толщина слоя исправляется путем повторной наплавки. При низком качестве наплавленного слоя его удаляют и производят наплавку заново. Наличие даже легко устраняемых дефектов – явление нежелательное.
После механической обработки наплавленной детали проверяются чистота поверхности и соответствие размеров обработанной детали чертежу. Одновременно выявляются скрытые дефекты: газовые поры, крупные трещины и т. д. Иногда после механической обработки или в её процессе обнаруживается местное несплавление. Его признаки: отслаивание части металла или характерное шелушение наплавленного слоя. Все эти дефекты выявляются при внешнем осмотре.
Наплавка ведущих звездочек бульдозера
Детали ходовой части транспортных гусеничных машин эксплуатируются в условиях интенсивного трения металла о металл при наличии прослойки абразива и испытывают значительные контактные ударные нагрузки, вследствие чего преждевременно изнашиваются. В связи с этим вопрос о выборе способа и технологии упрочнения рабочих поверхностей с целью повышения надежности и долговечности машины весьма актуален. Не менее важно решение проблемы восстановления изношенных деталей для повторного их использования.
Ведущие звездочки бульдозеров на базе тракторов Т-100, ТЦ-130, «Интер», «Камацу» и других работают в тяжелых условиях. Сложный характер изнашивания контактных пар зубья – втулки и наличие вязкого водоэмульсионного слоя с большим количеством частиц кварца различной фракции усиливают истирание рабочих поверхностей, что приводит к изнашиванию закаленного поверхностного слоя примерно в два-три раза быстрее, чем это предусмотрено нормативами. Износ зубьев звездочки достигает 50…60 мм, а впадин составляет 20…25 мм. Такая неравномерность изнашивания криволинейной поверхности значительно усложняет технологию восстановления.
Ведущие звездочки бульдозеров в основном изготавливают из высокоуглеродистых литых сталей, легированных марганцем и молибденом, с закаливанием рабочей поверхности до твердости примерно 420 HV на глубину до 5 мм.
С учетом требований, предъявляемых к материалу звездочек, работающих в контакте с гусеничной цепью, была опробована технология нанесения рабочего слоя оптимальной твердости и высокой износостойкости путем применения легирующих флюсов. Для наплавки под слоем флюса целесообразно использовать наплавочный материал, не содержащий дорогих легирующих элементов (W, Ni, V), но обеспечивающий достаточную износостойкость. Хромомарганцевоборидные сплавы (Fe–C–Cr–Mn–B) являются в этом смысле наиболее приемлемыми.
Установлено, что износостойкость рабочего слоя наиболее высокая при наплавке под механической смесью флюсов (АН348А) + (АНК-18) с добавками легирующих элементов. Наплавку производили сварочной головкой А-1416, дополнительно оборудованной механизмом колебания электрода. Диапазон колебаний от 0 до 140 мм, частота колебаний – регулируемая. Для восстановления звездочек использовали проволоки Св-08Г2С и Нп-30ХГСА диаметром 2 мм. Режим обработки: постоянный ток обратной полярности, номинальный ток 260…300 А, напряжение на дуге 32…35 В, скорость подачи проволоки 119 м/ч, скорость наплавки 20 м/ч, шаг наплавки 6…8 мм.
Зубья наплавлялись методом «горкой» (рис. 3). Наплавку производили в кокиль, одновременно являющийся шаблоном для контроля заданного шага и формы зуба. Поскольку износ у кромки зуба больше – была выбрана кинематическая схема механизма колебания электрода с замедлением в зоне выработки.
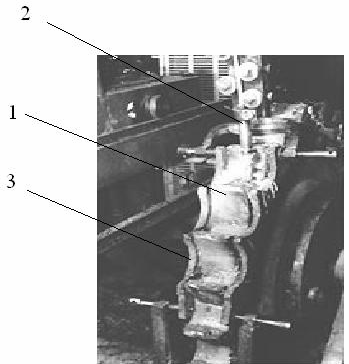
Рис. 3. Наплавка ведущей звездочки бульдозера: 1 – изделие; 2 – наплавочная головка; 3 – кокиль
В зависимости от модели бульдозера выбирают технологию восстановления зубьев: по ширине, шагу, износу и др. После наплавки поверхность зубьев не требует термической и механической обработки. Структура наплавленного металла феррито-перлитная, переходящая в игольчатый троостит. Твердость наплавленного слоя поверхности контакта составляет 400…420 HV. В зоне сплавления отсутствуют трещины и непровары.
Технология восстановления опорного катка гусеничного трактора
Мойка
Детали, поступающие на восстановление, подвергаются очистке, для того чтобы их можно было осмотреть и выявить дефекты. При очистке деталей удаляются продукты коррозии, остатки смазочных материалов и жировых пятен, абразивные и металлические частицы и др. Очистка деталей от загрязнений является специфической операцией процесса восстановления. От качества и полноты её проведения зависит долговечность восстановленных изделий. Так, недостаточно качественно удаленные загрязнения с поверхностей восстанавливаемых деталей приводят при наплавке к образованию в наплавленном материале пор и раковин и как следствие – снижению ресурса их работы.
Для выполнения этой операции необходимо уложить деталь в ванну с 8…10 %-ным раствором кальцинированной соды; удалить продукты загрязнения с помощью металлической щетки; извлечь деталь из ванны и высушить техническим феном до полного удаления влаги с поверхности.
Дефектация
Дефектацию деталей производят с целью определения их технического состояния и выявления следующих дефектов: целостности материала, величины износа и деформации. Измерительный инструмент и деталь должны иметь температуру одного порядка. Универсальные средства измерения выбирают в зависимости от допусков на восстанавливаемые размеры и конструктивные особенности детали.
Осмотреть каток на наличие сколов, смятия, трещин, изломов и других видимых повреждений; определить величину износа рабочих поверхностей при помощи штангенциркуля. Катки с величиной износа рабочих поверхностей по диаметру более 16 мм восстановлению не подлежат.
Установка детали
Установить каток в зажимной патрон наплавочной установки (например, УД-209) с помощью электротали типа ЭТ-300М и троса (рис. 4).
Предварительный подогрев
Предварительный подогрев детали осуществляется, если поверхностная твердость детали превышает НRСэ = 30. Как правило, изделие, изготовленное из стали марки Ст45, имеет твердость поверхности более 30 единиц, даже если оно не подвергалось закалке. Предварительный подогрев делается для того, чтобы предотвратить образование трещин. Подогрев можно осуществлять газовой горелкой ПГУ-40, нагревая деталь до температуры 150…200 °С. Деталь необходимо прогревать равномерно, для этого обеспечить ее вращение в зажимном патроне.
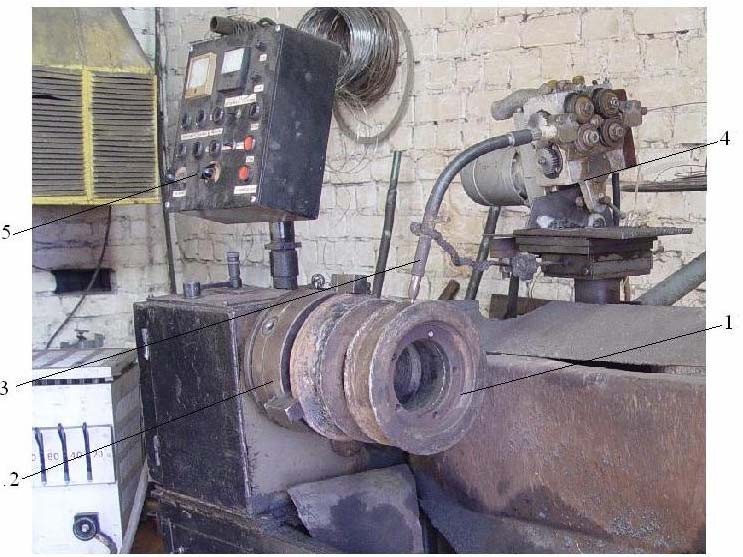
Рис. 4. Наплавка опорного катка гусеничного трактора порошковой проволокой на установке УД-209: 1 – каток; 2 – зажимной патрон; 3 – горелка; 4 – подающий механизм; 5 – пульт управления
Наплавка
Наплавка производится на постоянном токе обратной полярности. В качестве наплавочного материала используется порошковая проволока марки ПП-АН122 диаметром 2,8 мм. Это дает преимущества перед другими материалами:
- можно увеличить силу тока и тем самым повысить производительность процесса наплавки в 2 раза;
- отпадает операция отделения шлаковой корки от детали после наплавки;
- обеспечивается необходимая твердость наплавки НRС = 40…50. Наплавочная головка обеспечивает поперечные колебания элек-
трода с амплитудой до 40 мм в обе стороны. Поэтому можно наплавлять изношенную поверхность по всей ширине за один проход.
Последовательность и режимы наплавки рабочей поверхности:
- наплавитьпервуюрабочуюповерхностькаткадиаметром Ø 170 мм на длине L = 40 мм;
- наплавить вторую рабочую поверхность диаметром Ø 170 мм на длине L = 40 мм.
Режимы наплавки: ток – IН = 300 А; напряжение на дуге – U = 26 B; скорость наплавки – Vнапл = 8 м/ч; амплитуда колебаний – Ак = 20 мм; частота колебаний – fк = 35 кол./мин; скорость подачи проволоки – Vпр = 375 м/ч; вылет электрода – Hэ = 15 мм; угол наклона электрода от вертикальной оси – = 40°; смещение электрода от зенита в сторону, противоположную вращению детали, – L = 8 мм.
После наплавки рабочих поверхностей необходимо наплавить реборды.
Последовательность и режимы наплавки реборд:
- наплавить одну реборду по диаметру от 170 до 200 мм, угол реборды 30°;
- наплавить вторую реборду по диаметру от 170 до 200 мм;
- валики (4 штуки) накладывать друг на друга без поперечных колебаний электрода. Высота каждого наплавленного валика – 4 мм; ширина – 5 мм.
Режимы наплавки: ток – IН = 300 А; напряжение – U = 26 B; скорость наплавки – Vнапл = 30 м/ч; скорость подачи проволоки – Vпр = 375 м/ч; вылет электрода – Hэ = 15 мм; угол наклона электрода α = 40°; смещение электрода от зенита в сторону, противоположную вращению детали, – L = 8 мм.
Механическая токарная обработка
С помощью электротали ЭТ-300М и троса снять каток с наплавочной установки и установить его на токарно-винторезный станок 1К625Д.
Токарная обработка наплавленной детали необходима для обеспечения требуемых геометрической формы, размеров и шероховатости поверхностей. Поскольку твердость поверхности изделия из Ст45 после наплавки достаточно высока, то для точения наружной цилиндрической поверхности и реборд используют резец из твёрдого сплава Т15К6. Обработку ведут в один проход: число оборотов шпинделя станка – n = 315 oб./мин; подача резца – S = 0,3 мм/об.; глубина резания – t = 1,5 мм.
Калибровка внутреннего диаметра катка
С помощью электротали ЭТ-300М и троса снять каток со станка и установить каток вертикально в специальную оснастку для калибровки внутреннего диаметра. Калибровку внутреннего диаметра проводят для восстановления первоначальных размеров, так как после наплавки происходит усадка и внутренний диаметр становится меньше. Для калибровки внутреннего отверстия катка используют сверлильный станок 2М112 (2М-112) и специальную фрезу диаметром 50 мм. Калибровку (расточку) ведут на режимах: скорость вращения шпинделя станка –n = 190 oб./мин; подача фрезы –S = 0,5 мм/об. Контроль всех размеров восстановленного катка проводят с помощью штангенциркуля.
Технология восстановления шарнирной трубы трактора К-700
Мойка и дефектация. Уложить деталь в ванну с 8–10 %-ным раствором кальцинированной соды; удалить продукты загрязнения с помощью металлической щетки; извлечь деталь из ванны и высушить техническим феном.
Дефектацию деталей производят с целью определения их технического состояния и выявления следующих дефектов: целостности материала изделия, величины износа поверхностей и степени ее деформации. Необходимо осмотреть деталь на наличие сколов, смятия, трещин, изломов, царапин и других видимых повреждений; определить величину износа рабочих поверхностей при помощи штангенциркуля ШЦIII со шкалой 0–500 мм (0,1 мм).
Установка и предварительный подогрев детали
Установить деталь в патрон наплавочной установки УНВ 3-31 с помощью электротали ЭТ-300М и троса, при установке контролировать надежность сцепки между шарнирной трубой и тросом и закрепить деталь задней бабкой (рис. 5).
Газовой горелкой ПГУ-40 нагреть деталь до температуры 150…200 °С. Восстанавливаемые поверхности детали прогревать равномерно, вращая деталь в патроне установки.
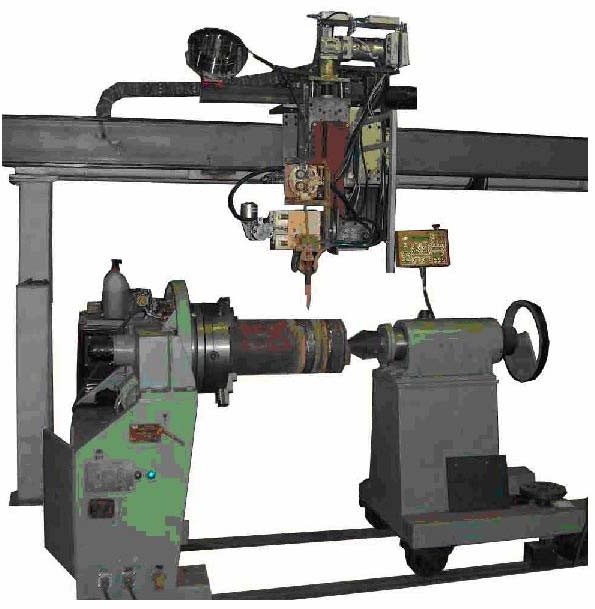
Рис. 5. Установка для наплавки УНВ 3-31
Наплавка
Наплавка производится на постоянном токе обратной полярности. Источником питания для электрической дуги может служить универсальный выпрямитель ВДУ-1202. В качестве наплавочного материала также может использоваться порошковая проволока марки ПП-АН122 диаметром 2,8 мм. Наплавка этой порошковой проволокой может выполняться без дополнительной защиты сварочной ванны флюсом или газом.
Наплавить первую рабочую поверхность диаметром Ø 300 мм на длине L = 150 мм; наплавить вторую рабочую поверхность диаметром Ø 300 мм на длине L = 150 мм; контролировать качество наплавки. Ток наплавки IН = 280…300 А.Напряжение U = 26…28 B.
Наплавка широкослойная с амплитудой колебаний электрода Ак = 30 мм. Частота колебаний fк = 32 кол./мин. Скорость наплавки Vнапл = 6…8 м/ч. Скорость подачи проволоки Vпр = 370…380 м/ч. Вылет электрода Hэ = 10…15 мм. Угол наклона электрода α = 40…45° от вертикальной оси. Смещение электрода от центра детали в сторону, противоположную ее вращению при наплавке, L = 10…12 мм.
Токарная обработка
С помощью электротали ЭТ-300М и троса снять каток с наплавочной установки и установить каток на токарно-винторезный станок 1К625Д.
Для обтачивания наружной цилиндрической поверхности используют резец из твёрдого сплава Т15К6. Обработку ведут в два прохода: первый черновой при числе оборотов шпинделя n1 = 215 oб./мин; подач и резца S1 = 0,6 мм/об. и глубине резания t1 = 1,5 мм.
Второй проход – чистовой на следующих режимах: n2 = 600 oб./мин, подача S2 = 0,2 мм/об., глубина резания t2 = 0,5 мм. После точения необходимо проконтролировать все размеры шарнирной трубы на соответствие их чертежу детали.
Восстановление шлицевых валов и осей
Наибольшее распространение шлицевые соединения получили в элементах трансмиссии – полуоси приводов ведущих мостов, валы со скользящими муфтами переключения, компенсирующие устройства. Надежность этих соединений, заложенная при конструировании узлов, снижается вследствие изнашивания деталей, коррозии, усталости и старения материала (рис. 6). Восстановление изношенных деталей, узлов и механизмов способствует успешному решению проблемы снабжения автохозяйств и ремонтных предприятий запасными частями и ежегодно дает большую экономию различных материалов и средств.
При ремонте валов и осей вначале выполняют сварочные и слесарные работы, так как при их осуществлении возможны деформации детали и могут быть повреждены чисто обработанные поверхности.
Ремонтную сварку и наплавку шлицевых поверхностей выполняют, как правило, с помощью автоматической или полуавтоматической сварки стальной проволокой в среде защитных газов на специальных манипуляторах-вращателях. Если размер диаметра вала не превышает 30 мм (шлицевая ось), то для восстановления шлицевой поверхности применяют метод вибродуговой наплавки, который обеспечивает минимальный разогрев самой детали, а соответственно, уменьшает изменение формы детали. Зачастую перед выполнением наплавочных работ изношенные шлицы снимают токарной обработкой, а затем производят наплавку слоя металла определенной толщины по винтовой линии или по образующей поверхности для последующего изготовления шлицов (рис. 7).
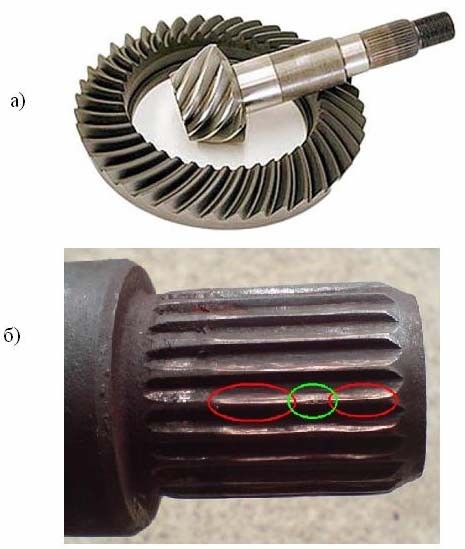
Рис. 6. Внешний вид шлицевого вала: а – шлицевой вал-шестерня; б – износ шлицов на валу
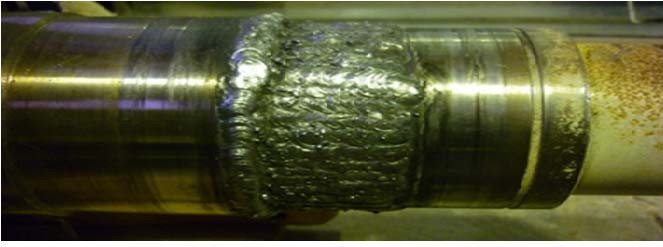
Рис. 7. Наплавленная поверхность шлицевого вала
Технология наплавки крупногабаритных валов, изготовленных из высокоуглеродистой стали, предусматривает их предварительный подогрев газовой горелкой с целью предотвращения сколов наплавленного слоя вследствие высоких внутренних (закалочных) напряжений.
После сварочных и наплавочных работ валы и оси подвергают правке и предварительной механической обработке. Чистовая обработка рабочих поверхностей вала должна выполняться в последнюю очередь. Для обеспечения неизменяемости формы вала и снятия внутренних напряжений после правки производят термическую обработку, состоящую в выдержке вала при температуре 400…500 °С в течение 0,5…1 ч.
Значительные прогибы валов устраняют горячей правкой под прессом, для чего место изгиба вала нагревают до 600 °С в горне или пламенем газовой горелки. После правки необходимо повторно проверить вал на биение и, если изгиб полностью не устранен, повторить операцию правки.
Шлицы на валах могут образовываться путем холодного накатывания, осуществляемого на шлиценакатных станках, подобных зубонакатным, или нарезаться фрезерованием дисковыми или червячными фрезами. Последний способ, выполняемый обычно на шлицефрезерных станках (рис. 8), подобных зубофрезерным, более точный и производительный, чем первый, выполняемый на горизонтально-фрезерных станках с применением делительных головок.
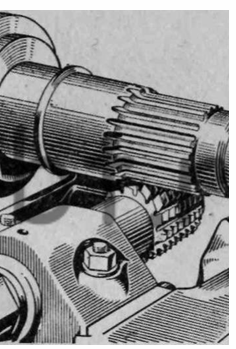
Рис. 8. Схема нарезки шлицов червячной фрезой
Просмотров: 377
Способы восстановления деталей
В ремонтной практике применяются следующие основные способы восстановления изношенных деталей: механическая и слесарная обработка, сварка, наплавка, металлизация, хромирование, никелирование, осталивание, склеивание, упрочнение поверхности деталей и восстановление их формы под давлением. Как правило, после восстановления детали одним из способов ее подвергают механической или слесарной обработке, что необходимо для восстановления посадок сопряженных деталей, устранения овальности или конусности их поверхностей, обеспечения требуемой чистоты обработки.
Механической и слесарной обработкой восстанавливают детали с плоскими сопрягаемыми поверхностями (направляющие станин, планки, клинья). При износе направляющих до 0,2 мм их восстанавливают шабрением, при износе до 0,5 мм — шлифованием, а при износе более 0,5 мм — строганием с последующим шлифованием или шабрением.
При ремонте валов, осей, винтов и т. п. в первую очередь проверяют и восстанавливают их центровые отверстия. После этого поверхности, имеющие незначительный износ (царапины, риски, овальность до 0,02 мм), шлифуют, а при более значительных износах наращивают, обтачивают и шлифуют до ремонтного размера.
При ремонте изношенных деталей нередко возникают трудности при выборе способа базирования детали для обработки в связи с изменением основной установочной базы изношенной детали. В таких случаях ориентируются не на основные установочные, а на вспомогательные базы, и от них ведут обработку рабочих поверхностей. Наряду с восстановлением деталей механической обработкой при ремонте негодную часть детали иногда заменяют новой.
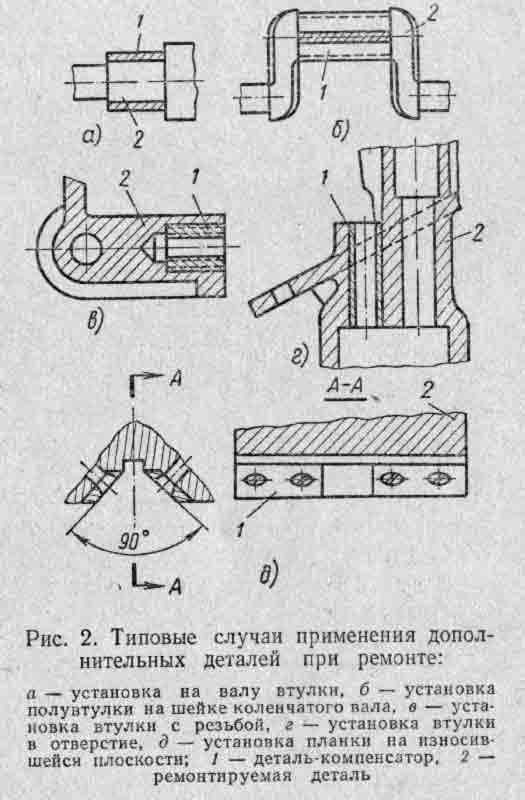
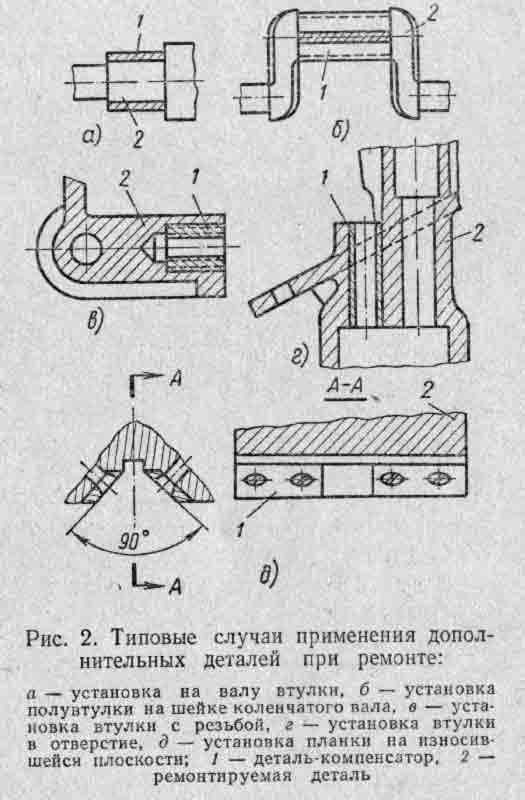
Применение компенсаторов износа. Чтобы восстановить первоначальные посадки сопряженных деталей, при их значительном износе применяют детали-компенсаторы. Одну из сопрягаемых деталей обрабатывают до ближайшего ремонтного размера и во вторую вставляют промежуточную деталь-компенсатор. Детали-компенсаторы могут быть сменными и подвижными. Сменные компенсаторы устанавливают в сопряжении, в котором износ появился к моменту ремонта. Подвижные компенсаторы устанавливают тогда, когда можно, не производя ремонта, соответствующим перемещением компенсатора относительно основных деталей устранить зазор, образующийся вследствие износа деталей. Сменными компенсаторами для цилиндрических деталей служат втулки и кольца, а для плоских— планки. Для наиболее распространенных узлов станков сменные детали-компенсаторы целесообразно заготавливать заранее в соответствии со шкалой ремонтных размеров.
Типовые случаи применения деталей-компенсаторов, используемых для устранения износа сопряжений, показаны на рис.2. При износе наружной цилиндрической поверхности вала на него напрессовывают или сажают на клей втулку (рис. 2, а). На износившуюся шейку коленчатого вала устанавливают полувтулку (рис. 2, б). Если в отверстии «разработалась» резьба, то в него ввертывают дополнительную втулку (ввертыш) с вновь нарезанной резьбой (рис. 2,в). При износе внутренней цилиндрической или конусной поверхности в деталь также вставляют втулку (рис. 2,г). Износ плоскостей чаще всего компенсируют планкой (рис. 2, д), которую привинчивают к ремонтируемой детали. Как видно из примеров, сменные детали в большинстве случаев скрепляют с одной из деталей сопряжения при помощи прессовой посадки, винтов, сваркой или универсальным клеем.
Ремонт повреждений и заделка трещин. Дефекты, возникающие в деталях в результате действия внутренних напряжений, больших усилий или из-за механических повреждений (трещины, пробоины, значительные задиры, царапины и выкрашивания), устраняют слесарно-механической обработкой. Трещины и пробоины запаивают, заваривают, заливают, металлизируют, ставят штифты и заплаты. Заплаты применяют для заделки пробоин и больших трещин, соединяя заплату с основной деталью винтами или заклепками. Для чугунных и дюралюминиевых деталей используют винты, а для стальных — еще и заклепки.
Восстановление деталей сваркой и наплавкой
При ремонте оборудования сварку применяют: для получения неразъемных соединений при восстановлении разрушенных и поврежденных деталей, для восстановления размеров изношенных деталей и повышения их износостойкости путем наплавки более стойких металлов.
Автоматизированные процессы сварки и наплавки являются более совершенными и экономически эффективными по сравнению с ручными способами. Наибольшее распространение в ремонтной практике получила автоматическая и полуавтоматическая дуговая сварка и наплавка под слоем флюса. Ручные способы сварки и наплавки менее совершенны, но являются незаменимыми при ремонте деталей машин в неспециализированных ремонтных предприятиях благодаря маневренности, универсальности и простоте процесса.
Газовую сварку применяют для восстановления деталей из серого чугуна. Детали малого размера и веса сваривают без предварительного подогрева, а крупные детали предварительно нагревают.
Электродуговая сварка более экономична и создает более надежное сварное соединение по сравнению с газовой сваркой.
Правильная подготовка детали к сварке обеспечивает высокое качество наплавленного слоя и прочное сцепление его с основным металлом. Перед сваркой детали очищают и разделывают их кромки. Поверхность деталей очищают стальной щеткой, напильником, наждачным полотном, абразивным кругом, пескоструйным аппаратом, затем промывают бензином или керосином, а также подвергают щелочному травлению. Кромки листов свариваемых встык разделывают (скашивают) под углом (60—70°), а края изломов и пробоин выравнивают.
Наплавка является одним из основных методов восстановления деталей. Она широко применяется в тех случаях, когда трущимся поверхностям необходимо придать большую износоустойчивость. Наплавляют два, три и более слоев часто твердыми сплавами, позволяющими увеличить срок службы деталей в несколько раз. Качество наплавки в значительной степени зависит от состояния восстанавливаемой поверхности. Чугунные и стальные детали из малоуглеродистой стали перед наплавкой обезжиривают с целью удаления масла из пор и трещин. Для этого поверхность детали обжигают газовой горелкой, паяльной лампой или в нагревательных печах. Копоть налет окислов после обжига удаляют с поверхности детали наждачным полотном или ветошью, смоченной керосином или бензином. Участок детали под наплавку обрабатывают стальными щетками или абразивными кругами.
Восстановление деталей металлизацией
Металлизацией называется нанесение расплавленного металла на поверхность детали. Расплавленный металл в специальном приборе — металлизаторе струей воздуха или газа распыляется на мельчайшие частицы и переносится на предварительно подготовленную поверхность детали. Нанесенный слой не является монолитным, а представляет собой пористую массу, состоящую из мельчайших окисленных частиц.
Способом металлизации восстанавливают размеры посадочных мест для подшипников качения, зубчатых колес, муфт, шеек коленчатых валов и т. п. Чтобы металлизационный слой прочно соединился с поверхностью детали, поверхность очищают от грязи и масла и подвергают пескоструйной обработке.
Твердость металлизационного покрытия определяется качеством наносимого материала.
Гальванические покрытия
Для повышения поверхностной твердости деталей и увеличения их сопротивления механическому износу, а также для восстановления размеров деталей их покрывают слоем хрома (хромируют) толщиной 0,25 и 0,3 мм.
Твердые хромовые покрытия подразделяются на два вида: гладкое и пористое. При гладком хромировании смазка на поверхности детали не удерживается из-за плохой «смачиваемости». При работе деталей возникает сухое трение, на трущихся поверхностях появляются задиры. Для устранения этого недостатка применяют пористое хромирование. В порах и каналах, образующихся на наружной поверхности детали, задерживается смазка, снижающая износ и удлиняющая срок службы деталей. Твердое гладкое хромирование применяют для восстановления размеров деталей, работающих с неподвижными посадками, а пористое — для деталей, работающих при значительных удельных давлениях, повышенных температурах и с большими скоростями скольжения. Поры и каналы в хромовых покрытиях чаще всего образуются электрохимическим способом, при помощи анодного травления.
Восстановление деталей путем гальванического наращивания слоя стали (осталивание, или железнение) — один из эффективных методов современной технологии ремонта. Осталивание в отличие от хромирования позволяет наносить слой металла значительно большей толщины (2—3 мм и более). Этим способом целесообразно восстанавливать; детали с неподвижными посадками или детали с невысокой поверхностной твердостью; детали, работающие на трение при величине износа более 0,5 мм; детали, работающие одновременно на удары и истира ние.
Твердое никелирование. Повышенная твердость никелевых покрытий достигается за счет применения электролитов специального состава, обеспечивающих получение осадков никеля с фосфором. Никелевые покрытия с содержанием фосфора обычно называют никельфосфорными покрытиями, а процесс их получения — твердым никелированием. Твердое никелирование может осуществляться электрическим и химическим способами. Химическое никелирование является более простым и осуществляется путем выделения никеля из растворов его солей с помощью химических препаратов — восстановителей.
Восстановление изношенных деталей давлением
Поврежденные и изношенные детали можно восстанавливать давлением. Этот способ основан на использовании пластичности металлов, т. е. их способности под действием внешних сил изменять свою геометрическую форму, не разрушаясь. Детали восстанавливают до номинальных размеров при помощи специальных приспособлений, путем перемещения части металла с нерабочих участков детали к ее изношенным поверхностям. При восстановлении деталей давлением изменяется не только их внешняя форма, но также структура и механические свойства металла. Применяя обработку давлением, можно восстанавливать детали, материал которых обладает пластичностью в холодном или нагретом состоянии. Изменение формы детали и некоторых ее размеров в результате перераспределения металла не должно ухудшать их работоспособность и снижать срока службы. Механическая прочность восстановленной детали должна быть не ниже, чем у новой детали.
К основным видам восстановления различных деталей давлением относятся:
- осадка при восстановлении втулок, пальцев, зубчатых колес;
- раздача при восстановлении пальцев поршней, роликов автоматов и т. п.;
- обжатие при восстановлении вкладышей подшипников и втулок;
- вдавливание при восстановлении зубчатых колес и шлицевых валиков;
- правка для выправления гладких и коленчатых валов и рычагов;
- накатка для увеличения диаметра шеек и цапф валов за счет поднятия гребешков металла при образовании канавок.
Метод пластического деформирования при ремонте деталей применяется не только для восстановления размеров изношенных деталей, но и с целью повышения их прочности и долговечности. Поверхностное упрочнение деталей повышает износостойкость и прочность деталей.
Пластическое деформирование деталей производят также обработкой стальной или чугунной дробью, чеканкой, обкаткой роликами или шариками.
Восстановление и склеивание деталей с использованием пластмасс
Для восстановления изношенных деталей при ремонте металлорежущих станков применяют пластмассы. В качестве клея пластмассы широко используются для склеивания поломанных деталей, а также для получения неподвижного соединения деталей, изготовленных из металлических и неметаллических материалов. При ремонте металлорежущих станков наибольшее распространение получили такие пластмассы, как текстолит, древеснослоистые пластики и быстро твердеющая пластмасса— стиракрил. Текстолит и древеснослоистые пластики применяются для восстановления изношенных поверхностей направляющих станков, изготовления зубчатых колес, подшипников скольжения, втулок и других деталей с трущимися рабочими поверхностями.
Одним из эффективных способов получения неподвижных соединений является склеивание деталей. По сравнению с клепкой, сваркой и сбалчиванием клеевые соединения имеют такие преимущества, как соединение материалов в любом сочетании, уменьшение веса изделий, герметичность клеевых швов, антикоррозионную стойкость и во многих случаях снижение стоимости ремонта изделия. В практике ремонта металлорежущих станков широко используется карбинольный клей и клей типа БФ. Детали, склеенные карбинольным клеем с наполнителем из непористого материала, устойчивы против действия воды, кислот, щелочей, спирта, ацетона и подобных растворителей. Различные марки клея БФ отличаются содержанием компонентов и назначением.
Процесс восстановления деталей склеиванием состоит из трех этапов: подготовки поверхности, склеивания и обработки швов. Поверхности деталей, подлежащих склеиванию, очищаются от масла, загрязнений и хорошо пригоняются. Клей наносят кистью или стеклянной палочкой. Жидкий клей наносят на обе соединяемые поверхности.
Для склеивания деталей, работающих при температуре 60—80° С, применяют клей БФ-2. Для склеивания деталей, работающих в щелочной среде, — клей БФ-4. Клеем БФ-6 приклеивают ткани и резину к металлу.
Клей БФ наносят на склеиваемые поверхности в два слоя с перерывом примерно в 1 ч 15 мин. Соединяемые детали принимают одну к другой (1 — 15 кГ/см2) и выдерживают под прессом.
Выдержка склеенных деталей под прессом
Марка клея | БФ-2 | БФ-4 | БФ-6 |
Температура, °С | 120—200 | 60—90 | 150—200 |
Длительность выдержки, ч | 1—3 | 3—4 | 0,25—1 |
Чтобы разобрать склеенные детали, их необходимо нагреть до 200° С и выше.


Восстановление деталей автомобилей с использованием синтетических материалов
Содержание страницы
Ремонт деталей и узлов синтетическими материалами находит все более широкое применение в ремонтном производстве. В качестве синтетических материалов используются составы на основе эпоксидной смолы, различные пластмассы и клеи. Нанесение синтетических материалов на поверхность изношенных или поврежденных деталей в основном осуществляется двумя способами: покрытие из раствора кистью и покрытие литьем под давлением. Нанесение покрытий из раствора кистью используют для восстановления изношенных или поврежденных поверхностей крупногабаритных, а также сложных по конфигурации деталей. Склеивать можно различные материалы, соединять которые другими способами затруднительно или даже невозможно. При этом не меняется структура материалов и их физические свойства, так как отсутствует тепловое воздействие. Клеи должны выдерживать вибрации и значительные температуры, быть водои маслостойкими и затвердевать достаточно быстро. Клеи нужны для заделывания трещин и проломов, соединения деталей, защиты и выравнивания поверхностей, восстановления изношенных мест, изготовления и закрепления деталей и уплотнения соединений.
1. Ремонт деталей с применением капрона
В ремонтной практике наибольшее распространение получил капрон марок А и В. Это твердый материал белого цвета с желтым оттенком, имеющий высокую прочность, износостойкость, маслои бензостойкость, а также хорошие антифрикционные свойства. Поставляется он в виде гранул размером 7…8 мм. Основными недостатками капрона являются низкая теплопроводность, теплостойкость и усталостная прочность. Максимально допустимая рабочая температура капроновых покрытий составляет от минус тридцати до плюс восьмидесяти градусов Цельсия. Покрытием из капрона ремонтируют поверхности втулок валов, вкладышей и других деталей. Ремонт изношенных поверхностей деталей с применением капрона в большинстве случаев производят литьем под давлением на специальных литьевых машинах. Капрон (в виде порошка размером 0,2…0,3 мм) можно наносить на поверхность детали напылением. Сущность этого способа состоит в том, что на подготовленную и подогретую поверхность детали наносится порошкообразный капрон. Ударяясь о разогретую деталь, частицы порошкообразного капрона плавятся, образуя пластмассовое покрытие.
2. Ремонт деталей с применением капрона литьем под давлением
На специально подготовленную изношенную поверхность детали наносят под давлением слой капрона. Деталь устанавливают в прессформу и в образовавшийся зазор между деталью и стенкой пресс-формы нагнетают под давлением расплавленный капрон (рис. 1). Затем пресс-форму раскрывают, снимают деталь, удаляют с нее литники и облой. При необходимости капроновое покрытие механически обрабатывают до получения требуемых размеров. Для улучшения качества готовую деталь термически обрабатывают в ванне с маслом при температуре 185…190 °С и выдерживают при этой температуре в течение 10…15 мин. При нанесении капрона его нагревают до 240…250 °С и подают под давлением 4…5 МПа (40…50 кгс/см2). Пресс-форму совместно с деталью предварительно подогревают до температуры 80…100 °С. Толщина покрытия рекомендуется от 0,5 до 5 мм. Литье под давлением проводится на термопластавтоматах ДБ-3329, литьевых машинах ПЛ-71 и др. Этот способ технологически прост, не требует сложного оборудования и оснастки.
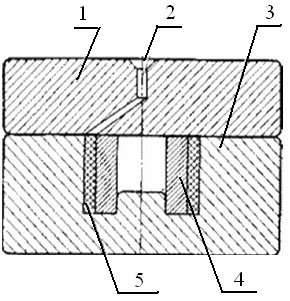
Рис. 1. Схема нанесения капрона на изношенную поверхность детали литьем под давлением: 1 – верхняя часть пресс-формы; 2 – литниковый канал; 3 – нижняя часть пресс-формы; 4 – ремонтируемая деталь; 5 – слой капрона
3. Виды напыления полимерных композиций в виде порошков
Газоплазменное напыление широко применяют для устранения вмятин и неровностей на кузовах и оперении машин. Подготовленный участок поверхности нагревают пламенем газовой горелки до температуры 200 °С. Затем специальной установкой УПН порошок воздушно-ацетиленовой струей подается на ремонтируемую поверхность. В процессе ремонта наносимый материал периодически уплотняют и формуют стальными ручными роликами.
При вихревом напылении в камеру установки загружают порошок с размером частиц 0,1…0,15 мм. Нагретую до температуры 300 °С деталь опускают в камеру, а под слой порошка вакуум-насосом подают азот. Порошок переходит в псевдосжиженное состояние, его частицы, оседая на поверхности детали, расплавляются и покрывают ее ровным слоем.
Для вибрационного напыления разогретую деталь вводят в сосуд с порошком, при этом вся система подвергается вибрации с частотой колебания 50…100 Гц; толщина слоя покрытия до 1,5 мм.
При вибровихревом напылении слой псевдосжиженного газом полимерногопорошкаподвергаютколебаниямсчастотой 50…100 Гц. При этом повышается качество покрытия. Перспективным является вибровихревое напыление на предварительно нагретую деталь. Ее устанавливают в патроне токарного станка, в резцедержателе суппорта закрепляют приспособление так, чтобы распылитель оказался выше детали (при покрытии наружных поверхностей) или внутри детали (при покрытии внутренних поверхностей). Полимерный порошок насыпают на всю длину наплавляемой поверхности и оплавляют теплом, аккумулированным металлом детали.
4. Ремонт деталей с применением составов на основе эпоксидной смолы
Главный связующий компонент этих составов – эпоксидная смола марки ЭД-6 или ЭД-5. Чаще применяют смолу ЭД-6. Это прозрачная вязкая масса светло-коричневого цвета. Для приготовления состава на основе смолы ЭД-6 на 100 частей (по массе) смолы вводят 10…15 частей дибутилфталата (пластификатор), до 160 частей наполнителя и 7…8 частей полиэтиленполиамина (отвердитель). В качестве наполнителя используют стальной порошок (160 частей), алюминиевый порошок (25 частей), цемент марки 500 (120 частей). Эпоксидную смолу разогревают в таре до температуры 60…80 °С, добавляют пластификатор, затем наполнитель. Отвердитель вводят непосредственно перед употреблением, так как после этого состав необходимо использовать в течение 20…30 мин. Составы на основе эпоксидных смол применяются для ремонта деталей, работающих при температурах от минус 70 до +120 °С. Эпоксидные смолы применяют для заделки трещин и пробоин в корпусных деталях, для восстановления неподвижных посадок и резьбовых соединений.
5. Технология заделки трещин
При заделке трещин определяют их границы и подготавливают поверхности (рис. 2). Границы трещины обычно засверливают сверлом диаметром 2…3 мм и снимают фаски под углом 60…70° на глубину 2…3 мм вдоль трещины на всей ее длине. Поверхность зачищают на расстоянии 40…50 мм по обе стороны трещины до металлического блеска и делают насечки. Затем обезжиривают ацетоном. Заплату вырезают из стеклоткани такого размера, чтобы она перекрывала трещину на 20…25 мм. Состав на основе эпоксидных смол готовят непосредственно перед его применением и наносят кистью или шпателем на поверхности толщиной около 0,1…0,2 мм. После этого накладывают заплату и прокатывают роликом. Составы затвердевают при температуре 18…20 °С в течение 24 часов. При повышении температуры время на отвердевание сокращается.
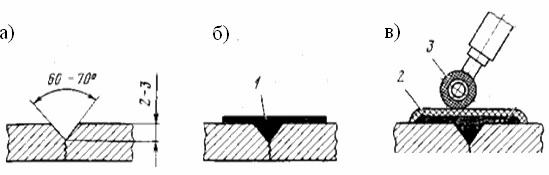
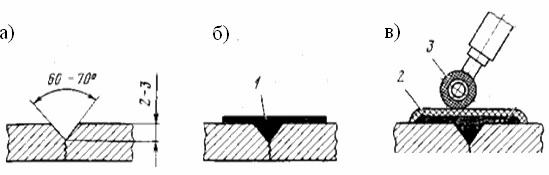
Рис. 2. Схема заделки трещины эпоксидной смолой: а – разделка трещины; б – заполнение составом эпоксидной смолы; в – прокатывание накладки роликом; 1 – слой смолы с отвердителем; 2 – накладка; 3 – ролик
6. Ремонт деталей с применением клеев
В ремонтной практике наибольшее применение получили клеи ВС-10Т, ВС-350 и № 88Н. Клей ВС-10Т – прозрачная однородная жидкость темно-красного цвета. Им можно склеивать между собой и в любом сочетании различные металлы и неметаллические материалы (сталь, чугун, алюминий, медь, стеклотекстолит, асбоцементные материалы и др.). Клеевой шов устойчив против воды, нефтепродуктов, холода. Температура отвердевания клея 180 °С. Давление при сжатии склеиваемых деталей равно 0,2…0,5 МПа (2…5 кгс/см2). Время выдержки для склеивания примерно 2 часа. Клей ВС-350 – многокомпонентный жидкий раствор, применяется для склеивания деталей из стали, меди, дюралюминия и теплостойких пластмасс. Диапазон рабочих температур клея от минус 60 до +100 °С. Клей устойчив к действию топлива, масел, органических растворителей, вибрации. Температура отвердевания клея равна 200 °С, давление при сжатии склеиваемых деталей 0,1…0,3 МПа (1,0…3,0 кгс/см2), время выдержки для склеивания составляет два часа.
Клей № 88Н применяют для соединения холодным способом вулканизированных резин и тканей с металлами, деревом и другими материалами. Клеевое соединение не разрушается от воздействия воды, холода, слабых растворов кислот и может выдержать температуру не более 60…70 °С. Стойкость клея по отношению к маслам, жидким топливам и растворителям неудовлетворительная.
Синтетические клеи используют для восстановления неподвижных соединений, наклейки фрикционных накладок (вместо клепки), заделки трещин. Приклеивание фрикционных накладок по сравнению с клепкой в 3 раза снижает трудоемкость ремонта, дает возможность полнее использовать фрикционные накладки, экономит значительное количество цветного металла.
Пример технологического процесса склеивания
Технологический процесс склеивания состоит из подготовки деталей, соединения их, сжатия, выдержки при заданной температуре (склеивания) и последующей обработки (при необходимости).
Для приклеивания фрикционных накладок к стальным дискам муфты сцепления сначала удаляют старые накладки. Поверхность диска очищают от грязи и ржавчины стальной щеткой, наждачной шкуркой или на шлифовальном круге. Затем обезжиривают поверхность диска ацетоном или бензином. Фрикционные накладки со стороны, обращенной к стальному диску, также обезжиривают ацетоном или бензином. На поверхность дисков и фрикционных накладок широкой кистью наносят первый тонкий слой клея ВС-10Т и дают ему подсохнуть на воздухе в течение 10…20 мин. На первый слой наносят второй. После этого фрикционные накладки устанавливают на диск и плотно прижимают к нему, обеспечивая давление сжатия 0,2…0,3 МПа. Накладки к диску прижимают в специальном приспособлении. Диски с прижатыми накладками помещают в сушильный шкаф, где их выдерживают при температуре 180 °С в течение 45…60 мин, а затем медленно охлаждают. Полностью остывшие диски освобождают от прижимов и удаляют с них наплывы клея, проверяют диски на коробление, торцовое биение и на суммарную толщину с накладками.
Преимущества способов ремонта деталей с использованием синтетических материалов: способы просты и надежны, имеют низкую себестоимость. При этом обеспечивается высокая износостойкость, антифрикционные свойства, достаточная прочность отремонтированных деталей и созданных клеевых соединений. В большинстве случаев не требуется сложного оборудования.
К недостаткам ремонта деталей с применением синтетических материалов следует отнести низкую теплопроводность и теплостойкость, низкую твердость и возможность изменения физико-механических свойств с изменением времени и температуры самих синтетических материалов, недостаточную усталостную прочность.
7. Организация рабочих мест для проведения ремонта
Участок ремонта деталей синтетическими материалами является изолированным производственным помещением. В его состав входят непосредственно помещение, где выполняется технологический процесс, и бытовые помещения (гардероб для одежды, душевая кабина, помещение для переодевания, гардероб для спецодежды, туалет, умывальник с холодной и горячей водой).
При использовании эпоксидных смол в небольших количествах разрешается работа с ними в общем помещении на постах, оборудованных приточно-вытяжной вентиляцией.
Если для отвердения синтетических материалов используются нагревательные устройства, то для них необходимо выделять отдельное помещение, так как некоторые вещества, используемые в процессе склеивания и нанесения паст, являются взрывоогнеопасными (ацетон, бензин и т. п.).
Для обдува деталей к рабочим местам должна быть подведена магистраль сжатого воздуха. Детали, подлежащие ремонту, необходимо хранить на стеллажах. Для хранения инструмента около каждого рабочего места устанавливают инструментальные шкафы.
Просмотров: 351
Восстановление запчастей — Википедия
Восстановление запчастей — комплекс мероприятий, направленных на возврат деталям, узлам, механизмам и агрегатам, которые вышли из строя во время эксплуатации или аварии подверглись естественному износу, их оригинальных характеристик, геометрических параметров и физических свойств; а также отрасль восстановительного производства, которая занимается обменом, выкупом, переработкой и повторным выпуском деталей, бывших в употреблении.
Отличие восстановления от обычного ремонта заключается в том, что в восстановленных механизмах замене на новые подлежат все детали, которые подвергались износу в процессе эксплуатации, в то время как отремонтированному изделию только возвращается работоспособное состояние[источник не указан 393 дня].
Типы запчастей, подлежащих восстановлению[править | править код]
На современном этапе разработаны технологии восстановления почти полной номенклатуры запчастей. Это обусловлено в основном двумя факторами: экологическими стандартами, которые устанавливают производителю регулирующие органы (в частности Всесторонние рекомендации по закупкам Управления по охране окружающей среды — Comprehensive Procurement Guideline (CPG)
Чаще всего применяют для восстановления дорогостоящих комплектующих
- двигатели (как бензиновые ДВС, так и дизельные) и их компоненты: блоки цилиндров, головки блоков (ГБЦ), распределительные и коленчатые валы, турбины, топливные насосы (в том числе высокого давления — ТНВД)
- трансмиссия: механические и автоматические коробки передач (МКПП и АКПП), раздаточных коробки, муфты включения полного привода
- электрооборудование: стартеры и генераторы
- компоненты рулевого управления: рулевые рейки, гидравлические усилители руля (ГУР), рулевые валы
- компоненты тормозной системы: главные и рабочие тормозные цилиндры, диски и колодки, суппорты и направляющие тормозов
Также применяются технологии реставрации к повреждению лако-красочного покрытия (ЛКП), деформированных кузвоных деталей и т. п.
Восстановленная Головка блока цилиндров Nissan X-Trail
Обменный фонд восстановленных коробок передач
Восстановленный рычаг подвески Merсedes Benz W220
Трансмиссия | Ходовая часть | Двигатель | Тормозная система | Электро оборудование | Рулевое управление | Топливная система | Системы управления |
---|---|---|---|---|---|---|---|
АКПП | Амортизатор | Блок цилиндров | Скоба суппорта | Генератор | Рейка рулевая | Дроссельная заслонка | ЭБУ |
Гидротрансформатор | Рычаг | ГБЦ | Суппорт тормозной | Электродвигатель привода | Вал рулевой | Инжектор | Система круиз контроль |
Коробка раздаточная | Тяга продольная | ДВС | Трубка тормозная | Стартер | Колонка рулевая | ТНВД | Система управления впрыском |
МКПП | Тяга поперечная | Турбина | Главный тормозной цилиндр | Компрессор кондиционера | Наконечник рулевой | Бензонасос | Система управления светом |
Редуктор заднего моста | Тяга реактивная | Вал коленчатый | Тормозной цилиндр | Ролик кондиционера | Насос гидравлического усилителя руля | Трубка топливная | Система ABS |
Редуктор переднего моста | Опора шаровая | Вал распределительный | Диск тормозной | Ролик натяжной | Трубка гидравлическая | ||
Трубка сцепления | Диск колесный | Компрессор | Барабан тормозной | Ролик обводной | Тяга рулевая | ||
Актуатор | Опора верхней стойки | Подушка двигателя | |||||
Вал приводной | Подвеска пневматическая | ||||||
Вал карданный | Стойка стабилизатора | ||||||
Муфта полного привода | |||||||
Цилиндр сцепления рабочий | |||||||
Цилиндр сцепления главный | |||||||
ШРУС | |||||||
Диск сцепления |
Согласно рекомендациям Ассоциации Восстановителей Автозапчастей (англ. — Automotive Parts Remanufacturers Association, APRA), существуют следующие стадии восстановления, которые отличаются процентом замены изношенных деталей новыми :
- Переработанные — Remanufactured это наибольшая степень восстановления запчастей, которая применяется в основном предприятиями-производителями оригинального оборудования (OEM). Эти предприятия внедряют программы выкупа или обмена у владельцев поврежденных запчастей с целью восстановления и повторного выпуска. Восстановленные таким образом запчасти имеют фактически те же характеристики, что и заново выпущеные. Преимущественно применяется в Европе.
- Пересобранные — Rebuilt — высокая степень восстановления агрегатов и механизмов с применением оргинальних ремкомплектов на сертифицированных производителем предприятиях. Восстановленная деталь должна пройти проверку на соответствие условиям и стандартам производителя, после чего может попасть в продажу с маркировкой «Х» («икс»). Распространено преимущественно на американском вторичном рынке.
- Отреставрированные — Recovered — промежуточный вариант восстановления, обычно без соблюдения стандартов производителя, направленный прежде всего на замену поврежденных узлов и механизмов. Еще один вид реставрации — воссоздание дорогостоящих и раритетных запчастей, которые давно сняты с производства и не могут быть заменены новыми, например, для не серийных старинных автомобилей. В этом случае больше всего ценятся приближения отреставрированной детали к оригиналу.
- Отремонтированые — Repaired — восстановленные этим методом запчасти, механизмы и агрегаты преимущественно не отличаются высокой надежностью, ведь обычно происходит не замена поломанных или изношенных деталей новыми, а возвращение им первоначальной формы и параметров. Цель ремонта не полное восстановление ресурса, а лишь устранение неисправности и возврата запчасти в работоспособное состояние. Именно такой тип получил распространение на территории бывшего СССР.
- Бывшие в употреблении — Used — снятые с машин детали, которые понесли потерю ресурса в ходе эксплуатации, но сохранили работоспособность. Продаются в большей степени на авторозборках.
Мощные производители оригинального оборудования (ОЕМ) а также автоконцерны разработали и внедряют коммерческие модели и технологии восстановления произведенных на их предприятиях запчастей. Типичная схема такого сотрудничества между производителем и потребителем — это создание программ замены изношенных запчастей на новые/восстановленные через сеть дилеров и официальных сертифицированных представителей. В этом случае владельцу поврежденного или изношенного агрегата предлагается вернуть его производителю в счет уплаты за новую запчасть. Например, компания Bosch предлагает замену отработавших стартеров, генераторов, компонентов дизельных систем и электрооборудования по программе Bosch eXchange[2]. Условиями не принятия по этой программе считаются сильная коррозия, неполная комплектация агрегата или его разборка или механическое повреждение.
Далее поврежденные детали возвращаются на предприятия изготовителя для восстановления или переработки. Некоторыми автоконцернами созданы специализированные заводы, которые занимаются исключительно восстановлением бывших в употреблении и возвращенных запчастей. Так концерн VAG построил завод в городе Кассель, который специализируется на восстановлении трансмиссий — на нем занято 16107 работников.
Компания Renault восстанавливает компоненты ходовой, двигателей, трансмиссии и электрооборудования на своем заводе в городе Шуази-ле-Руа: за год здесь разбираются, тестируются, реставрируются и собираются заново до 15 000 двигателей и до 18 000 КПП. Полученные таким образом изделия имеют те же гарантийные показатели, что и новые при цене меньшей на 40 %[3]
Ford на своем заводе внедрил восстановления бензиновых и дизельных двигателей на которые после восстановления предоставляется гарантия от 2 до 3 лет независимо от пробега. Используя бывшие в употреблении агрегаты, компания экономит на сырье и энергии, а также уменьшает выброс металлолома на свалку. По этой технологии восстанавливаются блоки цилиндров, головки блоков (ГБЦ), коленчатые и распределительные валы, шатуны, а замене на новые детали подлежат: поршни, поршневые кольца, подшипники, выпускные клапаны, прокладки и уплотнения.
Кроме собственного перевыпуска на своих мощностях автопроизводителями также получили распространение специализированные предприятия, которые профессионально занимаются восстановлением запчастей и имеют сертификаты авторизованных партнеров от автопроизводителей, но формально являются независимыми коммерческими предприятиями.
Примером восстановительного производства по такой схеме является британское предприятие Shaftec из города Бирмингем, которое восстанавливает в промышленных масштабах детали ходовой, рулевой и тормозной систем для различных моделей автомобилей для реализации на вторичном рынке Aftermarket. Наибольшим спросом пользуются тормозные суппорты, рулевые рейки и насосы гидравлического усилителя руля.
Некоторые известные производители запчастей ОЕМ предлагают также своим клиентам Aftermarket под собственным брендом восстановленные запчасти. По такой схеме действует итальянский производитель тормозов Brembo, который восстанавливает тормозные суппорты. Особенность этой схемы заключается в том, что восстанавливаются запчасти только собственного производства.
Компания TRW владеет заводом в Чехии, на котором осуществляет восстановление рулевых реек и насосов усилителя руля. Это производство внедрено в рамках большой программы концерна ZF[4] по восстановлению запчастей.
Стартер Mazda 3, который был поврежден во время эксплуатации (вверху) и восстановленный стартер (внизу)- Пантелеенко Ф. Ы. Восстановление деталей машин: Справочник М: Машиностроение, 2003. — 672 с.[1]
- Бобович Б. Бы. Утилизация автомобилей и автокомпонентов. М: МГИУ, 2010. — 176 с.[2]
- Восстановление автомобильных деталей. Технология и оборудование: учебник для высш. учеб. заведенный / У. Е. Канарчук, А. Д. Чигринец, А. Л. Голяк, П. М. Шоцкий. — М.: Транспорт, 1995. — 301 c.[3]
- Молодык Н. В., Зенкин А. С. Восстановление деталей машин Справочник. — М.: Машиностроение, 1989. — 480 с.: ил
- Канарчук В. Е. и др. Восстановление автомобильных деталей: Технология и оборудование Учеб. для вузов. — М.: Транспорт, 1995. — 303 с.
- ↑ Пантелеенко, Ф.И. Восстановление деталей машин: Справочник М: Машиностроение, 2003. — 672 с (неопр.). — М, 2003. — С. 672 с..
- ↑ Бобович, Б.Б. Утилизация автомобилей и автокомпонентов. М: , 2010. — 176 с (неопр.). — Москва: МГИУ, 2010. — С. 176. — ISBN 978-5-2760-1830-0.
- ↑ Канарчук В.Е. Чигринец Голяк Шоцкий, А.Д. О.Л. П.М. Восстановление автомобильных деталей. Технология и оборудование: учебник для высш. учеб. заведений (неопр.). — М: Транспорт, 1995. — С. 301.
СПОСОБЫ ВОССТАНОВЛЕНИЯ ДЕТАЛЕЙ
В ремонтной практике применяются следующие основные способы восстановления изношенных деталей: механическая и слесарная обработка, сварка, наплавка, металлизация, хромирование, никелирование, осталивание, склеивание, упрочнение поверхности деталей и восстановление их формы под давлением. Как правило, после восстановления детали одним из способов ее подвергают механической или слесарной обработке, что необходимо для восстановления посадок сопряженных деталей, устранения овальности или конусности их поверхностей, обеспечения требуемой чистоты обработки.
Механической и слесарной обработкой восстанавливают детали с плоскими сопрягаемыми поверхностями (направляющие станин, планки, клинья). При износе направляющих до 0,2 мм их восстанавливают шабрением, при износе до 0,5 мм — шлифованием, а при износе более 0,5 мм — строганием с последующим шлифованием или шабрением.
При ремонте валов, осей, винтов и т. п. в первую очередь проверяют и восстанавливают их центровые отверстия. После этого поверхности, имеющие незначительный износ (царапины, риски, овальность до 0,02 мм), шлифуют, а при более значительных износах наращивают, обтачивают и шлифуют до ремонтного размера.
Применение компенсаторов износа. Чтобы восстановить первоначальные посадки сопряженных деталей, при их значительном износе применяют детали-компенсаторы. Одну из сопрягаемых деталей обрабатывают до ближайшего ремонтного размера и во вторую вставляют промежуточную деталь-компенсатор. Детали-компенсаторы могут быть сменными и подвижными. Сменные компенсаторы устанавливают в сопряжении, в котором износ появился к моменту ремонта. Подвижные компенсаторы устанавливают тогда, когда можно, не производя ремонта, соответствующим перемещением компенсатора относительно основных деталей устранить зазор, образующийся вследствие износа деталей. Сменными компенсаторами для цилиндрических деталей служат втулки и кольца, а для плоских— планки. Для наиболее распространенных узлов станков сменные детали-компенсаторы целесообразно заготавливать заранее в соответствии со шкалой ремонтных размеров.
Типовые случаи применения деталей-компенсаторов, используемых для устранения износа сопряжений, показаны на рис.2. При износе наружной цилиндрической поверхности вала на него напрессовывают или сажают на клей втулку (рис. 2, а). На износившуюся шейку коленчатого вала устанавливают полувтулку (рис. 2, б). Если в отверстии «разработалась» резьба, то в него ввертывают дополнительную втулку (ввертыш) с вновь нарезанной резьбой (рис. 2,в). При износе внутренней цилиндрической или конусной поверхности в деталь также вставляют втулку (рис. 2,г). Износ плоскостей чаще всего компенсируют планкой (рис. 2, д), которую привинчивают к ремонтируемой детали. Как видно из примеров, сменные детали в большинстве случаев скрепляют с одной из деталей сопряжения при помощи прессовой посадки, винтов, сваркой или универсальным клеем.
Ремонт повреждений и заделка трещин. Дефекты, возникающие в деталях в результате действия внутренних напряжений, больших усилий или из-за механических повреждений (трещины, пробоины, значительные задиры, царапины и выкрашивания), устраняют слесарно-механической обработкой. Трещины и пробоины запаивают, заваривают, заливают, металлизируют, ставят штифты и заплаты. Заплаты применяют для заделки пробоин и больших трещин, соединяя заплату с основной деталью винтами или заклепками. Для чугунных и дюралюминиевых деталей используют винты, а для стальных — еще и заклепки.
ВОССТАНОВЛЕНИЕ ДЕТАЛЕЙ СВАРКОЙ И НАПЛАВКОЙ
При ремонте оборудования сварку применяют: для получения неразъемных соединений при восстановлении разрушенных и поврежденных деталей, для восстановления размеров изношенных деталей и повышения их износостойкости путем наплавки более стойких металлов.
Газовую сварку применяют для восстановления деталей из серого чугуна. Детали малого размера и веса сваривают без предварительного подогрева, а крупные детали предварительно нагревают.
Электродуговая сварка более экономична и создает более надежное сварное соединение по сравнению с газовой сваркой. Правильная подготовка детали к сварке обеспечивает высокое качество наплавленного слоя и прочное сцепление его с основным металлом. Перед сваркой детали очищают и разделывают их кромки. Наплавка является одним из основных методов восстановления деталей. Она широко применяется в тех случаях, когда трущимся поверхностям необходимо придать большую износоустойчивость. Наплавляют два, три и более слоев часто твердыми сплавами, позволяющими увеличить срок службы деталей в несколько раз. Качество наплавки в значительной степени зависит от состояния восстанавливаемой поверхности. Чугунные и стальные детали из малоуглеродистой стали перед наплавкой обезжиривают с целью удаления масла из пор и трещин. Для этого поверхность детали обжигают газовой горелкой, паяльной лампой или в нагревательных печах. Копоть налет окислов после обжига удаляют с поверхности детали наждачным полотном или ветошью, смоченной керосином или бензином. Участок детали под наплавку обрабатывают стальными щетками или абразивными кругами.
ВОССТАНОВЛЕНИЕ ДЕТАЛЕЙ МЕТАЛЛИЗАЦИЕЙ
Металлизацией называется нанесение расплавленного металла на поверхность детали. Расплавленный металл в специальном приборе — металлизаторе струей воздуха или газа распыляется на мельчайшие частицы и переносится на предварительно подготовленную поверхность детали. Нанесенный слой не является монолитным, а представляет собой пористую массу, состоящую из мельчайших окисленных частиц.
ГАЛЬВАНИЧЕСКИЕ ПОКРЫТИЯ
Для повышения поверхностной твердости деталей и увеличения их сопротивления механическому износу, а также для восстановления размеров деталей их покрывают слоем хрома (хромируют) толщиной 0,25 и 0,3 мм.
Твердые хромовые покрытия подразделяются на два вида: гладкое и пористое. При гладком хромировании смазка на поверхности детали не удерживается из-за плохой «смачиваемости». При работе деталей возникает сухое трение, на трущихся поверхностях появляются задиры. Для устранения этого недостатка применяют пористое хромирование. В порах и каналах, образующихся на наружной поверхности детали, задерживается смазка, снижающая износ и удлиняющая срок службы деталей. Твердое гладкое хромирование применяют для восстановления размеров деталей, работающих с неподвижными посадками, а пористое — для деталей, работающих при значительных удельных давлениях, повышенных температурах и с большими скоростями скольжения. Поры и каналы в хромовых покрытиях чаще всего образуются электрохимическим способом, при помощи анодного травления.
Восстановление деталей путем гальванического наращивания слоя стали (осталивание, или железнение) — один из эффективных методов современной технологии ремонта. Осталивание в отличие от хромирования позволяет наносить слой металла значительно большей толщины (2—3 мм и более). Этим способом целесообразно восстанавливать; детали с неподвижными посадками или детали с невысокой поверхностной твердостью; детали, работающие на трение при величине износа более 0,5 мм; детали, работающие одновременно на удары и истира ние.
Твердое никелирование. Повышенная твердость никелевых покрытий достигается за счет применения электролитов специального состава, обеспечивающих получение осадков никеля с фосфором. Никелевые покрытия с содержанием фосфора обычно называют никельфосфорными покрытиями, а процесс их получения — твердым никелированием. Твердое никелирование может осуществляться электрическим и химическим способами. Химическое никелирование является более простым и осуществляется путем выделения никеля из растворов его солей с помощью химических препаратов — восстановителей.
ВОССТАНОВЛЕНИЕ ИЗНОШЕННЫХ ДЕТАЛЕЙ ДАВЛЕНИЕМ
Поврежденные и изношенные детали можно восстанавливать давлением. Этот способ основан на использовании пластичности металлов, т. е. их способности под действием внешних сил изменять свою геометрическую форму, не разрушаясь. Детали восстанавливают до номинальных размеров при помощи специальных приспособлений, путем перемещения части металла с нерабочих участков детали к ее изношенным поверхностям. При восстановлении деталей давлением изменяется не только их внешняя форма, но также структура и механические свойства металла
ВОССТАНОВЛЕНИЕ И СКЛЕИВАНИЕ ДЕТАЛЕЙ С ИСПОЛЬЗОВАНИЕМ ПЛАСТМАСС
Для восстановления изношенных деталей при ремонте металлорежущих станков применяют пластмассы. В качестве клея пластмассы широко используются для склеивания поломанных деталей, а также для получения неподвижного соединения деталей, изготовленных из металлических и неметаллических материалов. При ремонте металлорежущих станков наибольшее распространение получили такие пластмассы, как текстолит, древеснослоистые пластики и быстро твердеющая пластмасса— стиракрил. Текстолит и древеснослоистые пластики применяются для восстановления изношенных поверхностей направляющих станков, изготовления зубчатых колес, подшипников скольжения, втулок и других деталей с трущимися рабочими поверхностями.
Способы восстановления деталей | Обслуживание и ремонт автомобиля
Авторемонтное производство располагает большим числом различных способов восстановления деталей, которые позволяют не только возвратить им свойства новых, но и в ряде случаев даже улучшить их.
Многочисленность технологических способов, применяемых при восстановлении деталей, объясняется разнообразием производственных условий и дефектов, для устранения которых они применяются. В зависимости от характера устраняемых дефектов все процессы восстановления деталей группируются в две основные группы: восстановление деталей с механическими повреждениями и восстановление деталей с изношенными поверхностями (с изменением размеров рабочих поверхностей деталей). К первой группе относят способы восстановления деталей, имеющих трещины, пробоины, изломы, деформации, а также коррозионные повреждения. Ко второй — имеющих изменение размеров и геометрической формы рабочих поверхностей в виде овальности, конусообразности, корсетности и др.
Применение того или иного способа восстановления зависит также от материала, из которого изготовлена восстанавливаемая деталь.
Наиболее распространенными в авторемонтном производстве способами восстановления деталей являются сварка и наплавка. Этими способами восстанавливают около 40% деталей. Широкое применение сварки и наплавки обусловлено простотой технологического процесса и используемого оборудования, возможностью восстановления деталей из большинства применяемых в автомобилестроении металлов и сплавов, высокой производительностью и низкой себестоимостью.
При восстановлении деталей находят применение следующие виды и способы сварки и наплавки: ручная дуговая сварка, газовая сварка, полуавтоматическая сварка в среде углекислого газа, полуавтоматическая сварка проволокой ПАНЧ-11, полуавтоматическая сварка порошковой проволокой, вибродуговая наплавка, автоматическая наплавка под слоем флюса, электроконтактная сварка. Другие способы и виды сварки и наплавки при восстановлении автомобильных деталей применяются редко.
Наиболее широкими возможностями обладает ручная электродуговая сварка. При восстановлении деталей ее применяют для заварки трещин, приварки обломанных частей и заплат на пробоины, заплавки изношенных отверстий, наращивании изношенных кулачков и зубьев и т.д. Ручную дуговую сварку применяют для устранения повреждений в деталях из алюминиевых сплавов, чугуна, стали.
При ручной электродуговой сварке больше, чем при любом другом процессе, применяемом при восстановлении деталей, успех дела зависит от квалификации сварщика, от его умения правильно выбрать марку и диаметр электрода, режим сварки, приемы манипулирования концом электрода.
Газовая сварка в авторемонтном производстве применяется при ремонте кабин, кузовов, а также при восстановлении деталей для заплавки изношенных отверстий, наращивании обломанных ушков. Она основана на использовании тепла, выделяющегося при сгорании ацетилена или других горючих газов в смеси с кислородом. При восстановлении автомобильных деталей чаще всего в качестве горючего газа применяют ацетилен. Температура ацетилено-кислородного пламени в самой его горячей точке равна 3000-3150°С. При газовой сварке скорость нагрева и расплавления металла значительно меньшая, чем при дуговой, а зона термического влияния значительно больше, поэтому не рекомендуется применять газовую сварку для устранения повреждений, находящихся в замкнутых контурах малопластичных металлов (например, чугуна).
Дуговая сварка в среде углекислого газа — это один из наиболее эффективных процессов для устранения повреждений в тонколистовых стальных деталях. Она все больше и больше вытесняет газовую и ручную электродуговую сварку при ремонте кабин, кузовов. Сварка в среде углекислого газа отличается высокой производительностью, хорошим формированием сварного шва, легкостью ведения процесса во всех пространственных положениях, концентрацией тепла в зоне сварки.
Полуавтоматическая сварка проволокой ПАНЧ-11 — это в сущности та же полуавтоматическая сварка в среде углекислого газа, только защита зоны горения дуги при этом процессе не требуется, так как эту роль выполняют специальные элементы, входящие в состав проволоки ПАНЧ. Этот способ сварки применяют в основном для устранения сложных повреждений в деталях из чугуна, где другими способами восстановить деталь затруднительно. Полуавтоматическую сварку проволокой ПАНЧ-11 отличает высокая производительность, прочность сварных соединений, плотность сварных швов, хорошая обрабатываемость наплавленного металла.
Полуавтоматическая сварка порошковой проволокой — это сравнительно новый процесс в авторемонтном производстве. Сущность способа заключается в том, что в качестве электродного материала применяют специальную проволоку, в состав которой наряду с легирующими элементами введены защитные газо- и шлакообразующие вещества, благодаря чему достигаются высокая твердость и износостойкость наплавленного металла. Для наплавки порошковой проволокой применяются те же автоматы и полуавтоматы, что и для сварки и наплавки сплошными электродными проволоками под слоем флюса. Наплавку порошковой проволокой рекомендуется применять, прежде всего, для восстановления деталей с большими износами.
Вибродуговая наплавка является разновидностью автоматической электродуговой наплавки. Она ведется колеблющимся электродом, что дает возможность наплавлять металл при низком напряжении источника тока. Благодаря этому образуется минимально возможная сварочная ванна, мелкокапельный переход металла с электрода на деталь. При вибродуговой наплавке получается достаточно хорошее сплавление основного металла с электродным, небольшой нагрев детали и малая по глубине зона термического влияния. Наиболее широкое применение получила вибродуговая наплавка в среде охлаждающей жидкости. Процесс применяют при восстановлении изношенных поверхностей очень широкой номенклатуры деталей.
Автоматическая наплавка под слоем флюса обеспечивает наиболее высокое качество наплавленного металла, так как сварочная дуга и ванна жидкого металла полностью защищены от вредного влияния кислорода воздуха, а медленное охлаждение способствует наиболее полному удалению из наплавленного металла газов и шлаковых включений. При автоматической наплавке заданный режим почти не изменяется. Наплавку под флюсом применяют при восстановлении шеек коленчатых валов двигателей, шлицевых поверхностей и других деталей автомобилей.
Электроконтактная сварка имеет три разновидности: точечную, шовную и стыковую. В авторемонтном производстве наиболее широкое применение находит точечная сварка, при которой соединяемые детали зажимают между двумя электродами и через место контакта пропускают ток большой силы. Точечную сварку применяют при ремонте кузовов и кабин для соединения деталей, изготовленных из тонколистовой стали.
Находит также применение способ восстановления деталей контактной приваркой металлической ленты. Для того чтобы исключить нагрев детали и улучшить условия закалки приваренного слоя, в зону сварки подают охлаждающую жидкость.
Пайка чаще всего применяется при восстановлении неразъемных соединений. Сущность метода заключается в том, что детали соединяются при помощи вводимого в зазор промежуточного металла или сплава (припоя), взаимодействующего с основным металлом и образующего жидкую металлическую прослойку, кристаллизация которой приводит к образованию паяного шва между соединяемыми деталями.
Очень перспективным является способ восстановления деталей методом нанесения газотермических покрытий, при котором на изношенную поверхность может быть нанесен слой толщиной от 0,03 мм до нескольких миллиметров, не вызывая перегрева металла. Сущность процесса заключается в плавлении исходного материала (порошка или проволоки) и переносе его на восстанавливаемую поверхность детали струей газа (воздуха).
Большое число деталей восстанавливают методом нанесения гальванических покрытий, основанным на процессе осаждения металлов на деталь из электролитов. В ремонтной практике наиболее широко применяют электролитическое хромирование, осталивание и электронатирание.
Все шире применяются при восстановлении деталей полимерные материалы. Их применяют при устранении механических повреждений на деталях, при компенсации износа рабочих поверхностей деталей (композиции на основе эпоксидных смол), а также при соединении деталей склеиванием, например, приклеивание фрикционных накладок.
Весьма широкое, применение при восстановлении автомобильных деталей получили различные виды слесарно-механической обработки. Обработкой деталей под ремонтный размер восстанавливают геометрическую форму их рабочих поверхностей. Постановка дополнительных ремонтных деталей обеспечивает восстановление изношенных поверхностей до размеров новых деталей. Детали восстанавливают также пластическим деформированием (правкой), которое основано на использовании пластических свойств материала детали. В зависимости от конструкции деталей применяют такие виды пластической деформации, как обжатие, накатку, осадку, вытяжку и др.
Вариантом ремонта методом постановки дополнительной ремонтной детали является способ ремонта заменой изношенной или поврежденной части детали на специально изготовленную дополнительную деталь.
Другие статьи по теме:
с вашего сайта.